Features
SMU Explains: A Brief History of the US Pig Iron Market
Written by Stephen Miller
October 13, 2023
The pig iron trade is an important element to the US steel and foundry industry. The electric-arc furnace (EAF) thin-slab casting steelmakers need pig iron to make drawing quality steels for several consumers they are trying to serve.
The ferrous scrap available to them contains higher levels of copper, aluminum, and other elements. These have to be neutralized by adding virgin iron units, namely basic pig iron and/or direct-reduced iron (DRI)/hot-briquetted iron (HBI). The iron foundry industry relies on pig iron to make their various grades of iron castings. These foundries supply parts and products to virtually every sector of the US economy.
Since the early 1990s, the US ferrous industry has imported between 4-7 million metric tons per year of pig iron from mainly three countries: Brazil, Russia, and Ukraine. Having access to these amounts of virgin iron units is critical to these industries.
One may ask, why do we have to rely on imports to meet these critical needs? After all, pig iron is made in blast furnaces that smelt iron ore into pure iron. Why couldn’t we make that product here?
The truth is we did have a thriving pig iron business in the US for years. There were depots located across the country where foundries could source their needs with reasonable freight costs. In the 1950s, there existed over 3,000 foundries making castings, mostly iron castings. Today only 600-700 are still operating. So, what happened?
The answer is technological advancements in steelmaking changed the course of our domestic pig iron business. The advancement was the shifting to the Basic Oxygen Furnace (BOF) from the Open Hearth Furnace to refine iron from the blast furnace into crude steel. The Open Hearth used tremendous amounts of scrap in their process, whereas the BOF used minimal amounts of scrap.
This conversion had the effect of leaving much of the country’s scrap supply looking for a home. Consequently, the price of scrap spiraled downward for years.
Meanwhile, our foundries, feeling pressure from imports, were looking for ways to lower costs and domestic pig iron was relatively expensive. They noticed the price of scrap was more than reasonable and they engaged with the scrap facilities in their area to supply them with segregated grades of scrap to replace, at least partially, the need for pig iron. Starting in the 1950s, this changeover spread around the country until the last merchant pig iron producer closed its doors in 1992. This was due to poor demand from an ever-shrinking foundry market.
Another significant aspect of the Open Hearth to BOF conversion is it gave rise to the mini-mills. Companies, like Nucor, using an EAF, utilized the excess scrap available is the US, to make long products and compete with the integrateds.
Eventually, technological advancements made it possible to make flat-roll steels in the scrap-based EAFs, but they needed pig iron to do it. Today, approximately 70% of steel production in the US is made in electric furnaces.
Ironically, in 1993, the first EAF thin-slab casting mill opened for business. This was followed by a host of others, all needing low residual scrap and pig iron or HBI. But pig iron was the material of choice. This is why we had to import pig iron from Brazil and the Commonwealth of Independent States (CIS) region to drive this new technology. And we still do today!
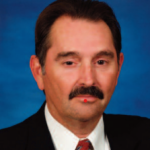
Stephen Miller
Read more from Stephen MillerLatest in Features
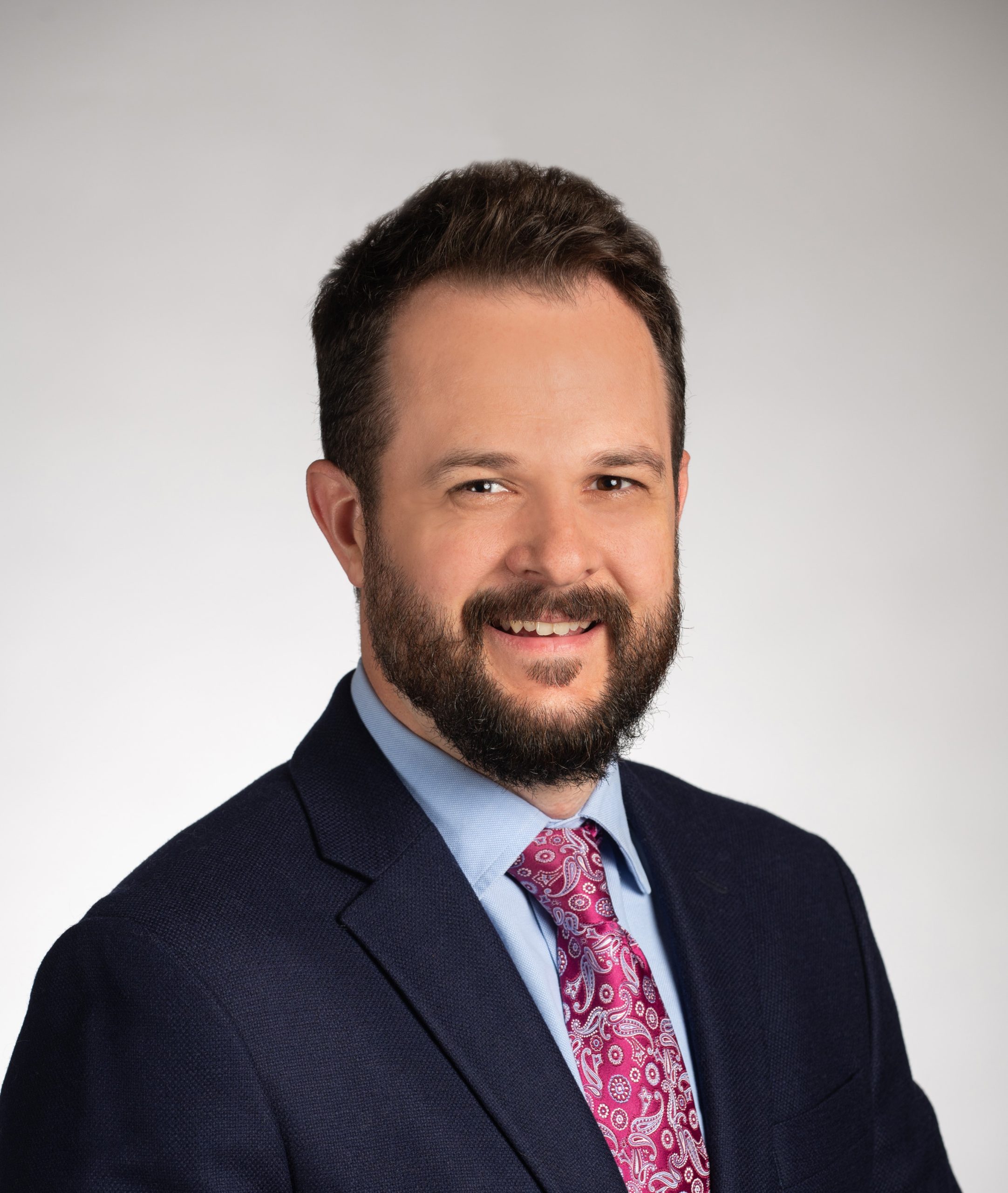
Final Thoughts
President Trump’s tariff policies have a lot more in common with a roundabout than you’d think.
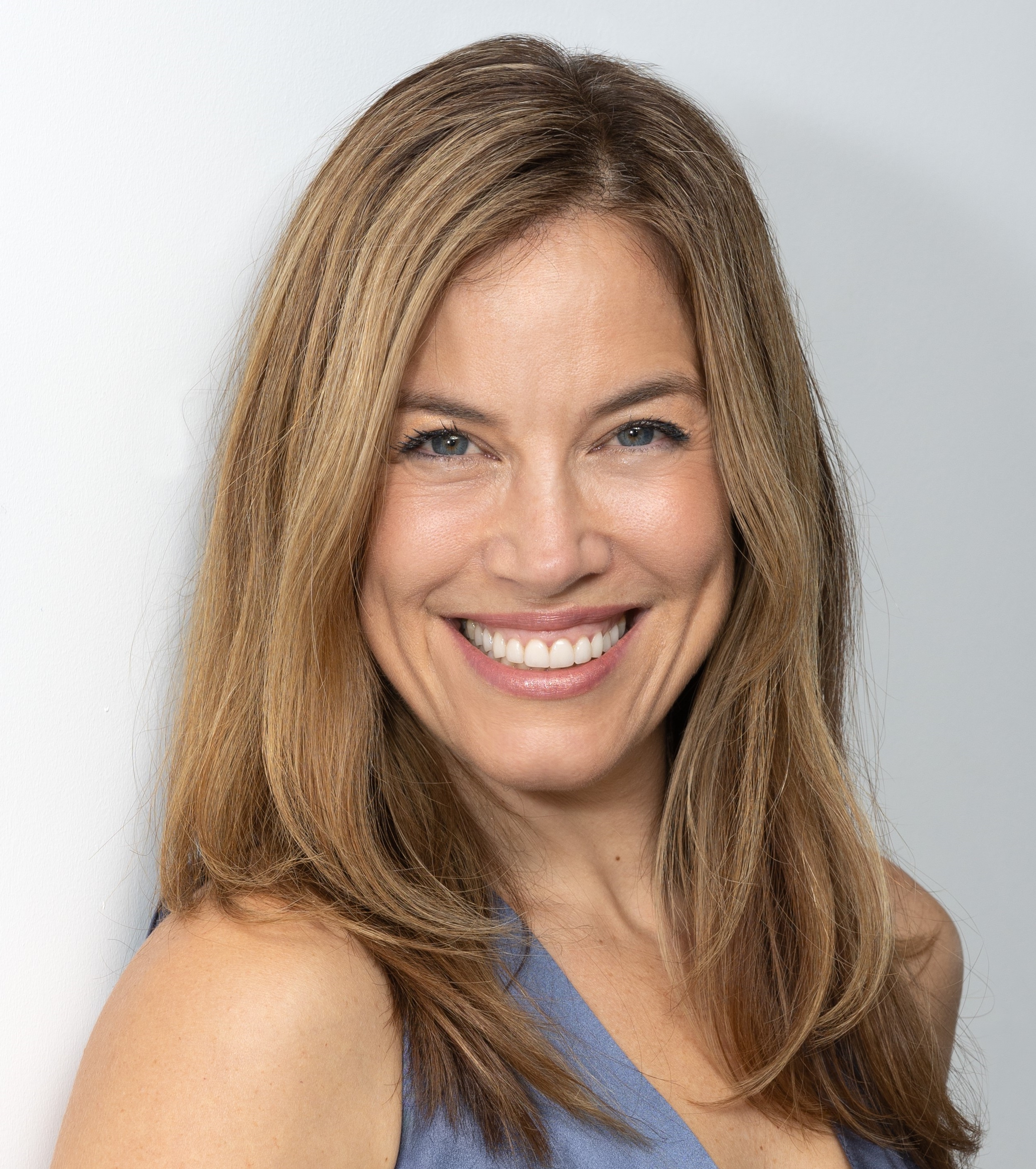
Timna Tanners joins Wells Fargo as managing director, equity research
Mining metals analyst Timna Tanners has joined Wells Fargo as managing director of equity research, according to a post on her LinkedIn profile.
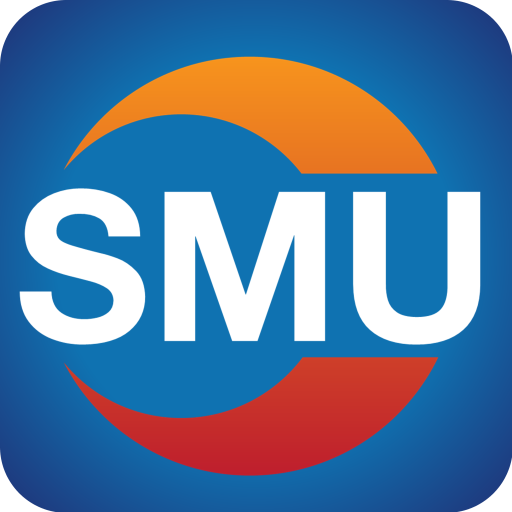
SMU’s Week in Review: July 4-11
A roundup of steel industry news that happened this week, as reported by Steel Market Update.
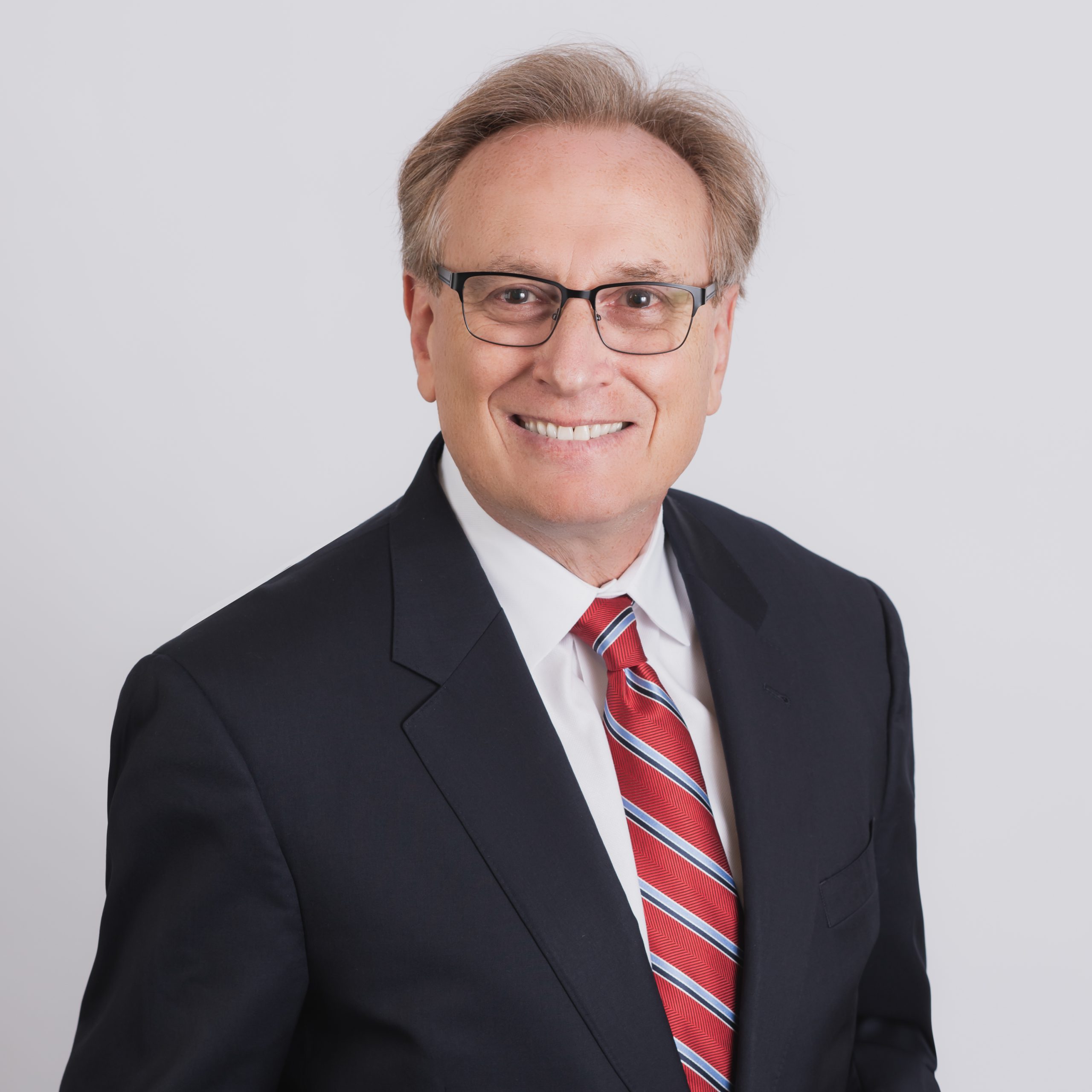
Price: Reciprocal tariff changes and potential new tariffs for Brazil, Canada, others
Trade issues do not seem poised to leave the headlines anytime soon. And as recent developments show, the administration’s tariff policy remains ever-changing.
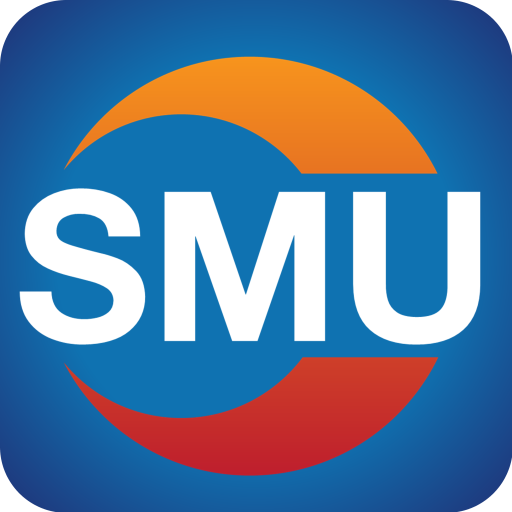
SMU Scrap Survey: Sentiment Indices rise
Both current and future scrap sentiment jumped this month, though survey participants reported responses before key trade news was announced.