Ferrous Scrap
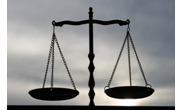
Price: Scrap is part of the solution, not a limitation
Written by Alan Price & Ted Brackemyre
July 5, 2024
North America has one of the most robust steel scrap markets in the world. There has been a long history of steel production, significant imports of steel and steel-containing products, and mature steel consumption. Due to this, the reservoir of scrap available to be recycled each year in the US and other North American markets is substantial and growing. Indeed, the American steel industry is one of the lowest emitting in the world because of its unique focus on recycling – and scrap-based steelmaking. Going forward, the availability of scrap in North America will not limit US decarbonization efforts or impede greater electric furnace deployment, including for the most advanced grades and types of steel.
Scrap is a powerful raw material when it comes to steel decarbonization. Pathways to decarbonization that focus on other raw materials pale in comparison in terms of scope and ambition, all the while requiring far greater capital expenditures. Scrap-based steelmaking in an electric furnace emits nearly 70% less than ore-based steelmaking in a blast furnace. And when coupled with green energy, the gap grows even wider. The fundamental advantage of decarbonizing using an electric furnace is that scrap can comprise up to 100% of the raw metallics. In contrast, a blast furnace can typically only use up to 30% scrap in its raw materials mix. While the amount of scrap available varies by region, in the US and North America, there is enough scrap available to support our path to decarbonization, including greater use of electric furnaces.
In fact, in a recent presentation, the largest integrated steelmaker in the US – Cleveland-Cliffs – projected electric furnace-based steelmaking to increase its share of the domestically produced steel in the US light vehicle market from 39% to 68% between 2020 and 2030. Over the same period, the domestic blast furnace-based share of the light vehicle market would decrease from 61% to 32%. These numbers show what the industry already knows – decarbonization through greater scrap use is happening. And it is possible for all types and grades of products, including demanding automotive steels. While Cliffs’ calculations are opaque, the rapid change they project recognizes that there is substantial scrap available in the US market, that scrap quality is not impeding this transition, and that electric furnaces will produce increasing quantities of the most advanced automotive steels.
This should not be a surprise. The Organization for Economic Cooperation and Development (OECD) recently projected that, even with growing scrap consumption, annual global scrap supply will exceed scrap demand through 2050. Further, the US is a significant net exporter of scrap, exporting more than three times as much as scrap as it imports each year, according to recent data from the Bureau of International Recycling. The OECD has also calculated that 87% of the scrap imported into the US in 2022 was from either Canada or Mexico. And nearly all other scrap imports were from the EU or the United Kingdom. This means that, if needed, there is minimal supply chain risk in sourcing certain quantities or grades of scrap through imports.
Recent studies have shown that many scrap availability calculations actually underestimate scrap supply because they rely on the outdated assumption that the average steel product life-span is 40 years. For instance, one study demonstrates that, based on the actual experience of the industry, the typical life-span is much lower. It’s far below 40 years and as low as 25 years in some countries. The steel in the average light vehicle, for example, is recycled every 10 to 12 years, meaning that steel is recycled more than three times in a 40-year period. In other words, those arguing that there is not enough scrap greatly underestimate how often steel products are recycled and, thus, how much steel scrap is available for recycling.
Steel scrap is also a globally traded commodity with more than 100 million tons being exported worldwide each year. Further, due to the significant growth in Chinese steel production since 2000, the Chinese government and many industry analysts project a substantial increase in Chinese scrap availability. This is especially true from 2030 onwards, as unprecedented quantities of Chinese scrap will enter the market each year.
Those arguing to preserve old ways of steelmaking, and impugn scrap use, often resort to claims about limited prime scrap supply in the US. However, the availability of prime scrap does not restrict the ability of steelmakers to transition towards greater scrap-based steelmaking. Many integrated steelmakers worldwide are in the process of converting towards electric furnaces and greater scrap usage. This is because different input recipes can be used to achieve the same metallurgies demanded by customers. Especially with the increased use of direct-reduced iron, low-copper shred, and other inputs, electric furnaces can use much less or even no prime scrap in their product mix to produce the highest quality steels.
Similarly, the concerns raised about copper and other residuals limiting increased scrap use for demanding applications are being addressed. Recent technological advancements allow processors to produce low-copper scrap from high-copper sources that can substitute for prime scrap. And, as the demand for both ferrous and non-ferrous metals (e.g., copper, aluminum) rises, even more will be invested into scrap-upgrading processes. Especially as companies and governments pursue policies to decarbonize and support scrap collection systems, the economic incentives to collect and process scrap of all types will increase significantly.
In short, let us not pretend that steel scrap availability in the US is a serious constraint on decarbonization. Or, that it’s a justification for applying more lenient emissions standards to high-emissions steel products made in ore-based blast furnaces. In this country, growing scrap-based steelmaking has been and will continue to be the principal path towards our decarbonization, including for the most advanced grades and types of steel.
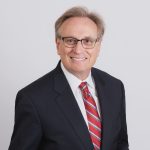
Alan Price
Read more from Alan Price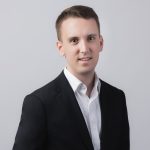
Ted Brackemyre
Read more from Ted BrackemyreLatest in Ferrous Scrap
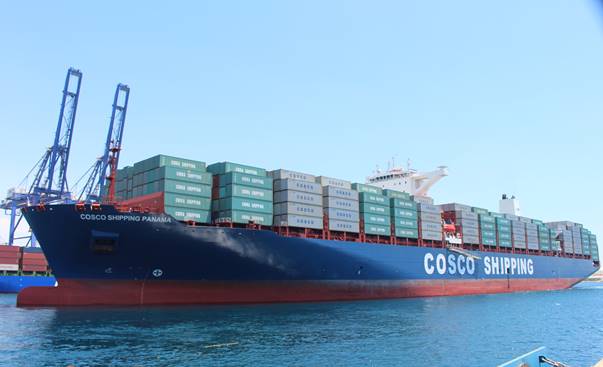
Ferrous scrap export activity resumes
Ferrous scrap export activity has picked up steam.
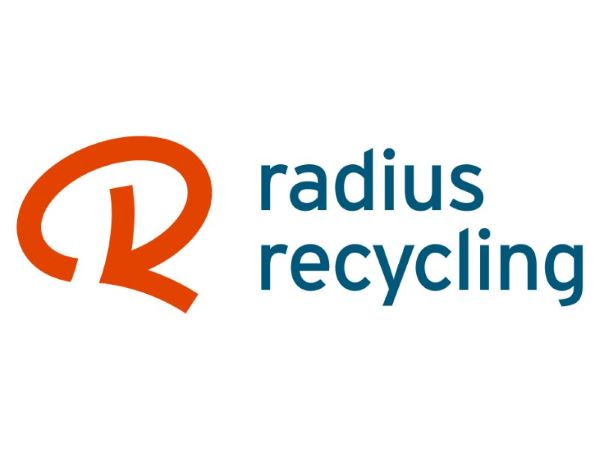
Radius loss narrows, volumes climb in ‘healthy’ West Coast market
Stronger steel demand in the Western US, rising scrap flows, and improved rolling mill utilization drove sequential gains for Portland, Ore.-based Radius Recycling.
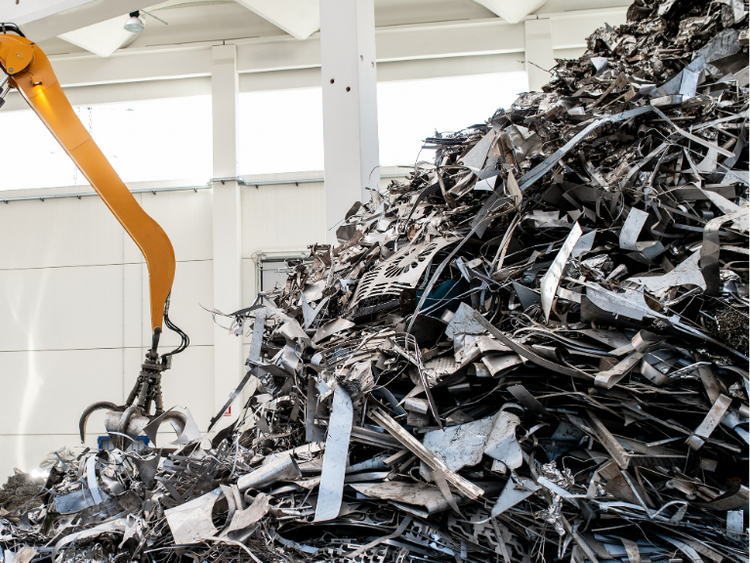
Ferrous scrap mart enters ‘summer doldrums’
Summer doldrums hit the US ferrous scrap market.
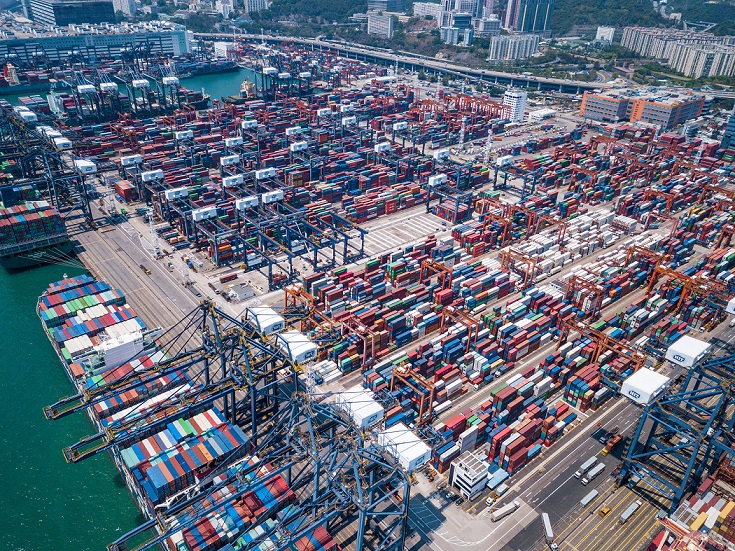
Bulk freight increases complicate ferrous trade flows
Freight rates have risen $30-$50 on transatlantic cargoes, depending on the final destination.
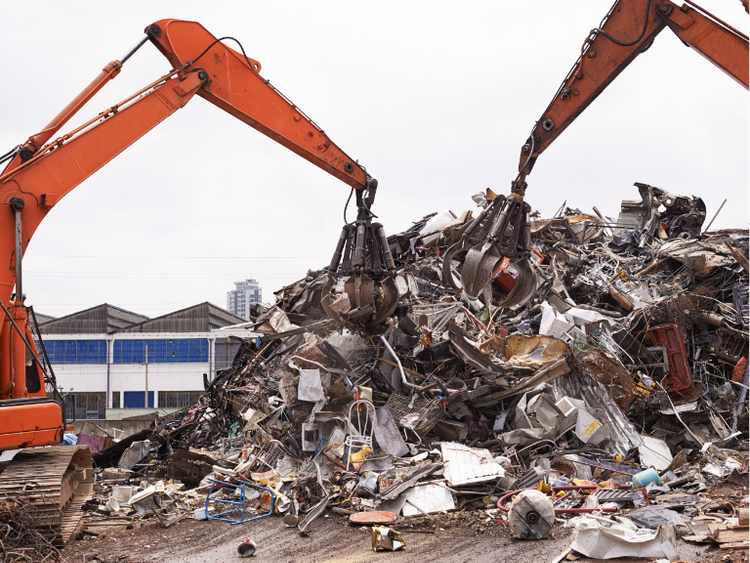
Ferrous scrap market outlook brightens
Ferrous scrap sentiment picks up.