Environment and Energy
Price: Blast furnaces aren’t necessary to make most advanced steels
Written by Alan Price & Ted Brackemyre
June 7, 2024
When it comes to steel decarbonization, we do not need to compromise our climate ambition to make the types of demanding steel products needed for our 21st-century economy. Nevertheless, many of the world’s highest-emitting steel producers and their allies would have you believe that one cannot be done without the other. They are wrong. They have created a false trade-off between our climate and our economic goals. We can transition to low emitting technologies while still meeting demand for the most advanced and highest quality steels, such as exposed automotive, high strength, electrical, and tin mill steels.
Unfortunately, the notion that high-emissions blast furnace production (BF) must be sustained in order to make high-quality steel products has taken root throughout parts of Washington, D.C., and the international community. In pushing this narrative, many large steel manufacturers and their advocates have successfully lobbied for different (i.e., more lenient) emissions standards to be applied to steel made in high emitting BFs than to steel made through low emissions processes, such as in an electric furnace (EF).
The reasons they give for treating BFs more favorably are two-fold. First, they claim that EFs cannot produce the most advanced steel grades, such as those used for exposed automotive products. Second, they argue that there is not enough steel scrap available to support a transition towards greater scrap-based steelmaking in EFs.
They are wrong on both counts, and neither of their arguments reflect the modern reality of the global steel industry. We focus on refuting their first claim here but will return to the scrap availability issue on another day.
The suggestion that EFs cannot be used to produce the most advanced types of steel products is simply not true. This was not always the case, but the world has changed, and the industry today knows that furnace type does not limit the grades of steel a particular facility can make.
Indeed, the actions of many of the largest steelmakers in the world reflect this as they are investing heavily to transition to EF and direct-reduced iron (DRI) operations. And they are doing it for the express purpose of producing the same types of advanced steels that some still argue cannot be produced in EFs.
For example, the Biden Administration recently awarded up to $500 million in grants to the largest US integrated steel producer – Cleveland-Cliffs – to replace the BF at its Middletown, Ohio, facility with a hydrogen-ready DRI plant and two electric-melt furnaces that will link with its existing mill equipment. In touting this project, Cleveland-Cliffs explains that the investment will allow it to “maintain the level of quality of the steel produced {and} the company’s leading position in the automotive end market.” In fact, in their latest earnings call, the CEO of Cleveland-Cliffs comments that the Middletown project will allow it to continue serving “the highest quality demand in end markets, like the automotive.”
Similarly, as illustrated below, many Canadian and European steel producers are investing billions of dollars to replace their existing BFs with EFs and DRI operations.
Company | Investment size (USD) | Capacity (mt/year) | Date online |
Algoma (Canada) | $875 million | 3.7 million | 2024 |
ArcelorMittal (Canada) | $1.31 billion | 2.4 million | 2028 |
ArcelorMittal (Belgium) | $1.3 billion | 2.5 million | 2030 |
ArcelorMittal (France) | $1.95 billion | 2.5 million | 2027 |
ArcelorMittal (Germany) | $1.6 billion | 3.5 million | 2025 |
ArcelorMittal (Spain) | $1.1 billion | 1.1 million | 2025 |
Blastr (Finland) | $4.24 billion | 2.5 million | 2026 |
British Steel (UK) | $1.6 billion | – | 2025 |
H2 Green Steel (Spain) | $2.5 billion | 2 million | 2025-26 |
H2 Green Steel (Sweden) | >$5 billion | 5 million | 2025 |
Liberty Steel (Romania) | $1 billion | 1 million | 2030 |
Saarstahl (Germany) | $3.67 billion | 3.5 million | 2027 |
Salzgitter (Germany) | >$2 billion | 1.9 million | 2025 |
SSAB (Finland) | $4.75 billion | 2.6 million | 2030 |
SSAB (Sweden) | $4.75 billion | 2.7 million | 2026 |
Tata Steel (Netherlands) | >$2 billion | 3 million | 2030 |
Tata Steel (UK) | $1.55 billion | – | – |
ThyssenKrupp (Germany) | >$3 billion. | 2.5 million | 2026 |
voestalpine (Austria) | $1.6 billion | 2.5 million | 2027 |
In making these substantial investments, many of these and other leading producers brag about how their EF conversion projects will allow them to transition away from BFs and still produce the most advanced steel grades and products. Among these other producers are Algoma Steel, ArcelorMittal Dofasco, AM/NS Calvert, U.S. Steel Europe, JFE Steel, Nippon Steel, Posco, SSAB, and Salzgitter. For instance, ArcelorMittal boasts that, when its Dofasco conversion project in Canada is completed that “all ArcelorMittal facilities in North America that make automotive steel will utilize an EAF-based process” and its new EF and DRI operations at Dofasco will be able to support “the most demanding product segments including automotive exposed, advanced high strength steels, and consumer packing.”
These projects illustrate that the production capabilities of a BF or an EF have nothing to do with the type of furnace, but rather they are determined by the casting, rolling, and finishing facilities attached to it. The industry agrees on that point – just follow where the money is being spent. Companies like ArcelorMittal are replacing BFs with EFs and using the same casting, rolling, and finishing mills to make the same types of advanced, exposed automotive steels that they were making before.
If an EF facility cannot make a particular product, it is entirely unrelated to the fact that it is an EF. Rather, it is because there is not the casting, rolling, and finishing equipment needed to produce that product at that facility. From this perspective, there is simply no reason to treat steel made in a BF as special or to label it as clean when its actual embodied emissions say otherwise.
Unfortunately, the outdated and inaccurate reasons given for favoring BF production have been embraced by parts of the US government and co-opted into American industrial policy. This is bad information fueling bad policy. As we noted in our prior commentary, the General Service Administration (GSA) has adopted a dual emissions standard that will favor certain higher emissions products as part of its Buy Clean program, despite the fact that the statute clearly limits GSA purchases under this program to products with “substantially lower” emissions. The Federal Highway Administration’s (FHWA) Buy Clean program is subject to the same statutory mandate, and fortunately, the FHWA has the opportunity to avoid making the GSA’s mistake and to focus its program on purchasing products with the lowest actual emissions.
In taking its approach, the GSA has repeated the same misplaced reasons to justify prioritizing BFs over EFs. But even if those claims were true for certain advanced steels, they are certainly not true for the construction-grade steel products – such as plate and structural pipe – that are being purchased through the GSA program. Not only can EFs make all construction-grade products, but they comprise virtually all the US construction market. As the CEO of Cleveland-Cliffs said in a 2022 earnings call: “We are not a supplier of steel for the construction markets . . . . That’s the biggest difference between us and our competition. It’s not EAF against blast furnace, it is the market that we serve.”
Given that the largest BF producer in the US acknowledges that they do not primarily serve the construction market, why then has the GSA created this distinction between BFs and EFs for construction products? It is not clear to us. Rather, the GSA appears to have gotten it wrong twice. They have adopted a broken logic and they have applied it in a context where – even if true – it does not make any sense. Accordingly, as we have commented previously, it is critical that the US government – including the GSA and the FHWA – avoid emissions policies that use dual standards. As shown above, there is a proven pathway for decarbonization, and it entails using EFs and DRI.
Lest we seem unreasonable, we do not advocate for an approach that would shut down every high-emissions producer or BF overnight. We acknowledge that such a dramatic solution is neither feasible nor desirable from a social and economic perspective. And an ample transition period may be necessary. We also recognize that some number of BFs may still operate in a low-carbon world. They may find a path to significantly lower their emissions, and there may still be room for a small number of BFs in a green steel industry. However, it is inconceivable that a decarbonized steel sector would contain as many BFs as it does now. For instance, the US exposed automotive market is approximately 3 million tons per year. This means that, even if these arguments were true, they would only justify keeping open two or three BFs in the US. There is no reason why the overwhelming majority of domestic BF production (nearly 22 million tons in 2023) cannot be shifted to EFs and other emerging technologies.
So, let us find sensible and climate-focused trade and industrial policies that set aside false attempts to label dirty as clean by having two sets of emissions standards. And let us avoid policies that would minimize the pressure on the highest emitters to decarbonize and penalize many of the producers with the lowest actual emissions.
Editor’s note: This is an opinion column. The views in this article are those of an experienced trade attorney on issues of relevance to the steel market. They do not necessarily reflect those of SMU. We welcome you to share your thoughts as well at info@steelmarketupdate.com.
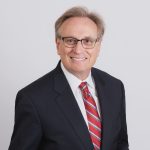
Alan Price
Read more from Alan Price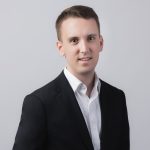
Ted Brackemyre
Read more from Ted BrackemyreLatest in Environment and Energy
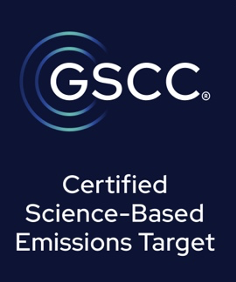
Global Steel Climate Council certifies eight SDI, ASA HR products
GSCC certifies eight products from Steel Dynamics and Arkansas Steel Associates.
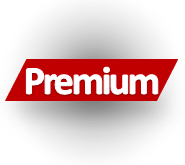
June energy market update
In this Premium analysis we examine North American oil and natural gas prices, drill rig activity, and crude oil stock levels. Trends in energy prices and rig counts serve as leading indicators for oil country tubular goods (OCTG) and line pipe demand.
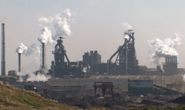
EPA deregulation proposals win praise from steel advocates
Two industry groups are applauding two EPA proposals that would support domestic steel production.
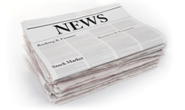
Met coal receives critical materials status
The US Department of Energy (DOE) adds metallurgical coal to the nation’s list of Critical Materials, following its designation by US Secretary of Energy, Chris Wright’s announcement on May 22.
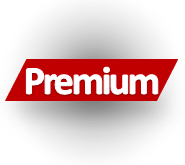
May energy market update
An analysis of the North American energy market in May.