Steel Mills
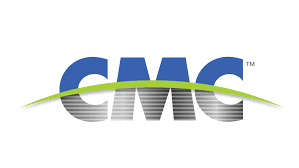
CMC Reports Strength in North America as Europe Struggles
Written by Laura Miller
October 12, 2023
CMC
Fourth quarter ended Aug. 31 | 2023 | 2022 | % Change |
---|---|---|---|
Net sales | $2,209.2 | $2,407.1 | -8% |
Net income (loss) | $184.2 | $288.6 | -36% |
Per diluted share | $1.56 | $2.40 | -35% |
Full fiscal year ended Aug.31 | |||
Net sales | $8,799.5 | $8,913.5 | -1% |
Net income (loss) | $859.8 | $1,217.3 | -29% |
Per diluted share | $7.25 | $9.95 | -27% |
Earnings Results
With solid demand and attractive margins, the North American market has been helping to prop up CMC’s results as its European operations struggle with weaker demand amid challenging market conditions.
CMC’s fiscal fourth-quarter sales were down 8%, while net income declined 36% (see chart). For fiscal year 2023, sales were down just 1% from the prior year, while net income dropped 29%, the Irving, Texas-based longs producer and metal recycler said.
In North America, Q4 finished steel volumes were up 2% year over year (YoY), while average selling prices were down by $172 per ton YoY. The cost of scrap utilized dropped by $49 per ton. This resulted in steel product margins over scrap declining by $123 per ton YoY.
Q4 steel tonnages of 758,000 tons in North America were down 4% sequentially but up 8% YoY. Average selling prices of $932 per ton for its rebar and merchant bar products were 5% lower than the previous quarter and 16% lower than the year-ago quarter.
Raw material shipments in North America were 16% lower sequentially and 4% lower YoY at 344,000 tons. The average selling price of raw materials was $838 per ton in Q4, a slight increase from $833 per ton in the prior quarter but a 12% decline from Q4 2022.
In Europe, where CMC operates a mill in Poland, net sales declined 15% quarter on quarter and 27% YoY to $301.3 million. Steel shipments of 389,000 tons were 9% lower than both the prior and year-ago quarters.
Outlook
“Strong pricing and demand conditions for domestic rebar have started to diverge from the weaker global environment, and growth within the US construction sector similarly stands in contrast to most other global regions,” commented CMC president and CEO Peter Matt on the company’s earnings call with analysts on Thursday, Oct. 12.
“This robust relative demand has attracted rebar imports from nontraditional suppliers who have put pressure on domestic pricing in recent months. Despite these more challenging conditions, we expect CMC’s North American business to continue generating margins well in excess of historical average levels but down from the record highs of recent quarters,” Matt added.
In the current quarter, CMC expects seasonally lower shipments, margin compression in steel products in North America, and challenging market conditions to persist in Europe.
CMC’s backlog has reduced in volume and value due to a slowdown in the rate at which contracts are awarded, Matt said on the call. Driving this is tightness in the construction labor market and a tighter credit market for many types of commercial projects, he said.
Infrastructure spending has been slow to materialize, but executives on the call said they expect to see more money flowing starting next calendar year.
“The US is in the early stages of massive investment trends that are intended to remake large portions of our economy by extensively upgrading infrastructure, realigning global trade patterns and reorienting automotive production to electric vehicles, and transitioning the electricity grid to greener sources of energy. Construction makes all this possible,” Matt stated.
As a key supplier to the construction markets, Matt said CMC is well positioned “to be both a primary beneficiary of the expected growth and a key solution provider to our customers.”
Operations Update
During Q4, CMC had a major planned outage at its flagship Steel Alabama merchant bar mill. This resulted in lower total quarterly merchant bar shipments: 216,000 tons vs. 248,000 tons in the prior quarter and 249,000 tons in the year-ago quarter.
CMC’s Arizona 2 micro mill began operations in June “and is making steady progress in ramping up production,” the company said. It is targeting a full run rate of 500,000 tons – 350,000 tons of rebar and 150,000 tons of merchant bar. For fiscal 2024, the mill’s production is anticipated to hit 400,000 tons. Some of those tons will be incremental, while others will replace tonnages currently supplied by other CMC mills, Matt said on the call.
CMC broke ground on its Steel West Virginia project this summer. CMC’s total cap-ex spending in 2024 and 2025 will likely remain elevated due to that project, CFO Paul Lawrence said.
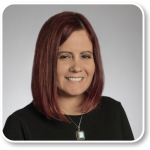
Laura Miller
Read more from Laura MillerLatest in Steel Mills
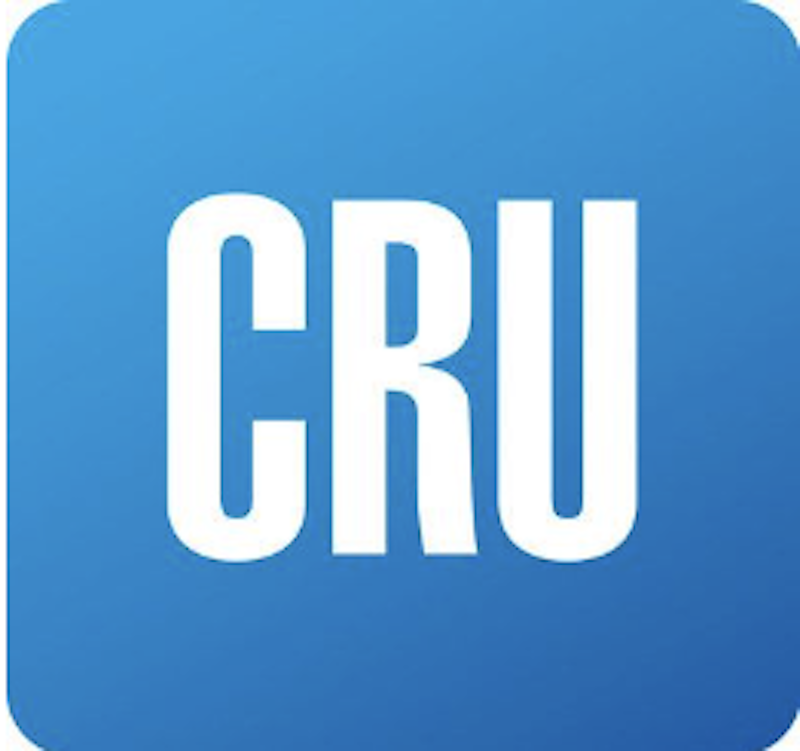
CRU: Tata Steel looks to shed 1,600 jobs in the Netherlands
The company said, “The challenging demand conditions in Europe driven by geopolitical developments, trade and supply chain disruptions and escalating energy costs have affected the operating costs and financial performance."

Reports: Federal funding for Cliffs’ project could be slashed
Elon Musk's DOGE is determining which Department of Energy grants to advance and which ones to terminate, according to several media outlets
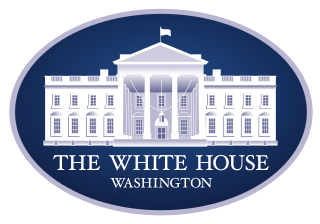
Trump still against selling USS to Japanese firm: Report
Despite ordering a new review of Nippon Steel’s bid for U.S. Steel, President Trump said he is still against selling USS to a Japanese company, according to media reports.
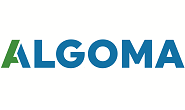
Algoma looks to sell more steel in Canada in wake of Trump’s tariffs
The Canadian steelmaker said its absorbing higher tariffs as it moves forward.
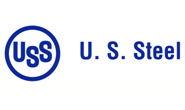
Ancora abandons plan to take over leadership of USS
Investment firm Ancora Holdings Group has halted its play for U.S. Steel's board, citing Nippon Steel’s proposed bid for USS “gaining momentum.”