Steel Mills
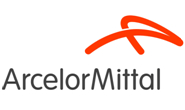
CRU Decarb Conference: ArcelorMittal Takes Kitchen Sink Approach to Carbon Neutrality
Written by Michael Cowden
July 1, 2021
ArcelorMittal wants to be carbon neutral by 2050, but reaching that goal will hinge on developing new ways to take fossil fuels – namely, coal and natural gas – out of the steelmaking process, a company executive said.
It will also require that key technologies – carbon capture and storage (CCS), biofuels and other renewable energies – become less expensive and more widely available, ArcelorMittal Chief Technology Officer Pinakin Chaubal said.
“If hydrogen is made available at large scale and at the right prices, we can also bring hydrogen,” Chaubul said.
He made the comments during a keynote speech at CRU’s Steel Decarbonisation Strategies 2021 conference, which was held virtually.
Both integrated and electric arc furnace (EAF) steelmaking will be necessary to allow steelmakers to achieve carbon neutrality while also churning out high-quality products, Chaubul said.
That’s because steel demand is expected to increase, in part because lower carbon sources of energy generation are more steel intensive than traditional sources. It’s also because scrap supplies are not infinite, he said.
“Even if we use all the scrap that is available, we still will need the other routes to completely decarbonize,” Chaubul said.
The problem: Increased scrap usage – among the low hanging fruits when it comes to decarbonizing – means that available scrap will have more impurities as recycling rates approach almost 100%. Impurities like copper can make steel brittle.
And the scrap alternatives used to dilute such impurities – think direct-reduced iron (DRI), hot-briquetted iron (HBI) and pig iron – are all ore-based metallics. The consequence: “a significant pressure on the iron ore base,” he said.
The blast furnace route tends to get the most attention among culprits for CO2 emissions because of its reliance on coking coal. But the EAF-DRI route also entails significant carbon emissions because it is generally powered by natural gas, Chaubul said.
That’s why it’s important to make technologies such as carbon capture and storage – siphoning off carbon via pipeline and/or liquifying it and moving it elsewhere – more widely available and more efficient.
Other solutions being studied by ArcelorMittal include recycling CO2 gasses generated in the steelmaking process as well as using carbon dioxide and carbon monoxide to make industrial chemicals such as ethanol, which is used to make a range of downstream products including plastics and biofuels.
And when it comes to replacing the coal used to make coke, the steelmaker is looking at ways to increase the use of “sustainable biomass” – think recycled wood and agricultural waste – that could be converted into “biocoal” or “biochar,” he said.
“We are also experimenting with technologies that allow us to completely move away from the carbon process,” Chaubal said.
One example: ArcelorMittal is eyeing technologies that resemble aluminum smelting more than traditional steelmaking. Namely, converting iron oxide directly into iron via an electrochemical process, he said.
That would reduce direct emissions, although electrolysis would also require significant amounts of electricity, which would increase indirect emissions.
These studies are not all theoretical. ArcelorMittal is already putting them into practice across its European operations, Chaubul noted.
Case in point: The steelmaker is working to build a DRI plant in Hamburg, Germany – where it already operates one DRI furnace – designed to run on hydrogen. The new DRI plant, expected to have production capacity of 100,000 tonnes per year, will initially use hydrogen extracted from the off gasses of the existing DRI facility. If hydrogen becomes more widely available, then the quantity of H2 the new DRI unit consumes will be increased, he said.
Another example: ArcelorMittal is building a commercial scale bioethanol plant at its steel mill in Ghent, Belgium, that will be fueled by waste gas generated at the mill.
While there are many possibilities in theory and several already in place in practice, “significant challenges” remain to reaching carbon neutrality. “It’s absolutely important that we have developments of pioneering, very innovative technology,” Chaubal said.
By Michael Cowden, Michael@SteelMarketUpdate.com

Michael Cowden
Read more from Michael CowdenLatest in Steel Mills
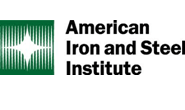
AISI: Raw steel production backs off multi-year high
US raw steel output edged lower last week after hitting a multi-year high in mid-June, according to the American Iron and Steel Institute (AISI).
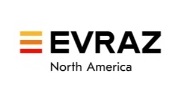
Private equity firm Atlas Holdings to acquire Evraz North America
Atlas Holdings said it has signed a definitive agreement to acquire Evraz North America (Evraz NA). The Greenwich, Conn.-based private equity firm said it expects the deal for the Chicago-based steelmaker to close in the second quarter of 2025 subject to various closing condition.
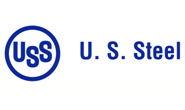
Granite City Works must remain open and other terms of the Nippon-USS deal
SEC documents also name Trump specifically as having veto power certain decisions are part of the “Golden Share” provision.
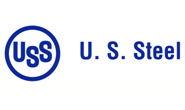
USS shuffles some leadership roles after close of Nippon deal
USS shuffles leadership deck after deal closes with Nippon.
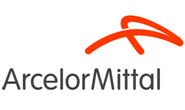
ArcelorMittal fires up steelmaking at Calvert mill
With the marking of the EAF’s first heat earlier this month, the mill has moved from a rerolling and finishing mill to a full steelmaking facility.