Steel Mills
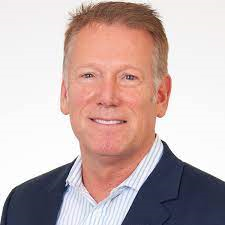
SSAB Q&A, Round Two: Fossil-Free Steel Coming in Early '22
Written by Michael Cowden
June 29, 2021
SSAB Americas President Chuck Schmitt joined SMU for a Community Chat webinar last week during which we talked plate, renewable energy and fossil-free steelmaking.
We also got to some good questions from you about the hydrogen-based steelmaking SSAB is undertaking in Sweden through its HYBRIT partnership with iron ore miner LKAB and power producer Vattenfall. As often happens, we didn’t get to all of your questions in our allotted 45 minutes online.
So Schmitt was kind enough to take some time to answer the questions we didn’t get to. Not only about fossil-free steel but also about more conventional stuff like Section 232 and lead times.
Below is a lightly edited version of Q&A, Round 2 with SSAB. We think you’ll find it useful.
Are there ongoing efforts to use renewable energy at the Mobile, Ala., plant?
We regularly engage with our electricity supplier on their portfolio of energy sources, and we are aware of their plans around renewable fuels, including hydrogen. It’s a strong business relationship, with a benefit being they understand our need for renewable energy, and they are working on it. The provider to our Mobile plant has set a target to be carbon neutral by 2050.
Can you please share more information on the SSAB Iowa relationship with MidAmerican Energy, and their focus on renewable energy? Is it wind, solar or both?
MidAmerican and the state of Iowa are leaders in wind energy development. They are using predominately wind to generate electricity for our facility. Additionally, we also enjoy the circular relationship by manufacturing wind tower plates for a number of fabricators that serve the Iowa wind energy market as well as the rest of the U.S.
What investments is SSAB contemplating in the U.S. relative to GHG emission reductions and producing fossil-free steel?
We continue to study scope 2 and 3 emission sources in addition to conducting trials around biofuels, reducing charge carbon and possible hydrogen use ahead of running trials of the HYBRIT sponge iron. When we run HYBRIT trials (in the U.S.), we intend to deploy some of these alternative fuels at the same time. Pending the success of these trials, we are prepared to invest in new technology – including equipment and services that will produce fossil-free steel.
What have been the major tech initiatives of SSAB, in existing production plants, in achieving low emissions?
There are a number of initiatives coming out of our R&D facility in Iowa working on lowering emissions. There is a steering group in the Americas around fossil-free steelmaking in coordination with Sweden. This is in preparation of us producing fossil-free steel in the U.S. Some of these include how we will melt it, with what kind of scrap, and other areas we can reduce fossil fuel use in the process. The goal is for us to get closer and closer to fossil-free steel. Development of HYBRIT ironmaking is not the only step. Replacement of fossil fuels in electric arc furnace (EAF) steelmaking poses technical and economic challenges. Biologically based alternatives to coal exist. But finding the right material and adapting processes to account for the differences with coal is a significant project.
How will/do SSAB’s plant melt/use carbon-free direct-reduced iron (DRI)?
It would be a very similar process to how we consume typical hot-briquetted iron (HBI). We will use HYBRIT sponge iron, and we will use it very similarly to HBI.
Is sponge iron made from scrap?
No. Sponge iron is made from iron ore.
Will you/do you export steel from the U.S.?
Yes. We have been exporting from our U.S. operations for over a decade into Canada, Mexico, South America and Asia. That’s consistent with our go-to-market strategy for premium products produced by SSAB Americas and SSAB Special Steels.
What is SSAB’s lead-time in the U.S.?
Our lead time and order intake are currently managed month-to-month. It’s approximately 10-12 weeks.
Do you feel the cost associated with going fossil free will allow SSAB to be competitive pricewise, or will the changes drive production costs – and selling prices – significantly higher?
We know some costs will increase in the process. But we don’t know how much that will be until we get into commercial production. Fossil-free steel is intended to be a premium product for identified applications. That’s consistent with how we already approach some of our current premium products.
Have any of the domestic auto manufacturers in the U.S. shown interest, as Volvo has in Sweden, for fossil-free steel?
We have seen a great deal of interest for a number of applications for fossil-free steel, including from domestic auto and truck manufacturers.
Do you have any plans for fossil-free steel or hydrogen-based steelmaking in the U.S.?
We intend to be making our first trial of fossil-free steel in the U.S. in early 2022. And we expect full production capabilities by 2026.
North American end users and service centers are being placed on allocation. So some are starting to look to Europe and Asia for steel. Will Section 232 tariffs in the U.S. or Canadian safeguard measures still be in place in fall and winter?
In light of the ongoing problem of global overcapacity in steel, a number of governments around the world – including the U.S., EU and Canada – have imposed tariffs, safeguards or other similar trade measures. These measures address the impact of the global overcapacity on domestic steel producers in North America and Europe. These trade measures are likely to continue in some form into next year while governments continue to undertake efforts to address the underlying causes of global steel excess capacity.
Can you elaborate on your moving your corporate headquarters from Lisle, Ill., to Mobile, Ala.? What is SSAB’s relationship with this very steel-intensive state?
Our move to Mobile was completed a little over two years ago, and it has been a good one. The state, county and city elected leadership have worked closely with us. And we are certainly enjoying the synergies of being closer to our manufacturing base.
By Michael Cowden, Michael@SteelMarketUpdate.com

Michael Cowden
Read more from Michael CowdenLatest in Steel Mills
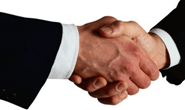
POSCO inks MoU with Hyundai on Louisiana EAF mill
POSCO has signed a Memorandum of Understanding (MoU) with Hyundai Motor Group that includes an equity investment in Hyundai’s previously announced EAF mill set to be built in Louisiana.
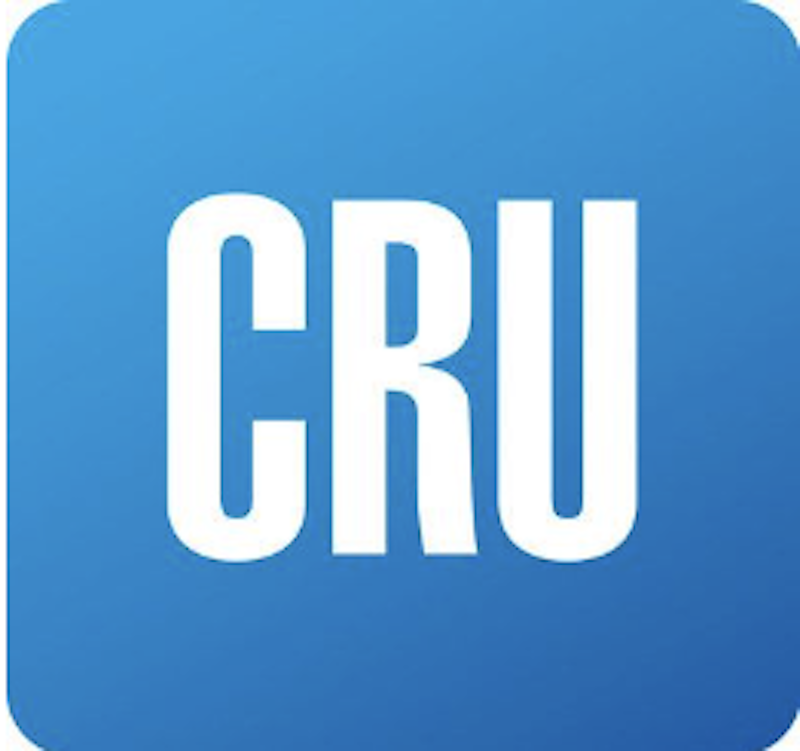
CRU: Tata Steel looks to shed 1,600 jobs in the Netherlands
The company said, “The challenging demand conditions in Europe driven by geopolitical developments, trade and supply chain disruptions and escalating energy costs have affected the operating costs and financial performance."

Reports: Federal funding for Cliffs’ project could be slashed
Elon Musk's DOGE is determining which Department of Energy grants to advance and which ones to terminate, according to several media outlets
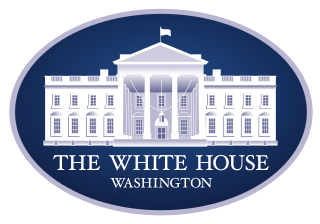
Trump still against selling USS to Japanese firm: Report
Despite ordering a new review of Nippon Steel’s bid for U.S. Steel, President Trump said he is still against selling USS to a Japanese company, according to media reports.
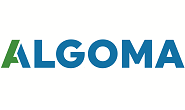
Algoma looks to sell more steel in Canada in wake of Trump’s tariffs
The Canadian steelmaker said its absorbing higher tariffs as it moves forward.