Steel Mills
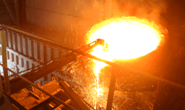
Idled Blast Furnaces Leave ~5.5M Ton Hole for New EAFs to Fill
Written by Michael Cowden
May 21, 2021
Much attention has been paid to how much new electric-arc furnace (EAF) flat-rolled steel capacity is being added to the North American market. Less has been written about how many tons of integrated steelmaking capacity have been taken out.
An analysis by Steel Market Update indicates that the latter figure is perhaps equally significant. It also provides necessary context when considering the potential impact of new capacity on the domestic flat-rolled steel market.
The figures referenced in this article come from SMU’s blast furnace status table, which you can access by clicking here.
There are 20 blast furnaces operating or undergoing maintenance in North America. That number shrinks to 15 when one looks only at the U.S. – where eight are run by Cleveland-Cliffs and seven by U.S. Steel.
Cliffs’ eight furnaces, all of which are operating now, have a combined capacity of 52,200 tons of iron per day – or 19.05 million tons per year, per SMU calculations.
U.S. Steel’s seven operating furnaces, one of which is down for maintenance (Mon Valley Works No. 1, which began a 25-day outage on April 30), have a combined capacity of 27,400 tons of iron per day – or 10 million tons per year, per SMU figures.
Large swathes of capacity were idled in the second quarter of 2020 following the outbreak of the COVID-19 pandemic. That makes year-over-year comparisons less meaningful than they would be ordinarily. But the first quarter of 2020, initially a good quarter for steel, provides a reasonable comparison.
Cliffs is now operating at approximately the same blast furnace footprint that it had in the first quarter of last year. U.S. Steel is not.
The “A” blast furnace at U.S. Steel’s Granite City Works near St. Louis was temporarily idled at the end of the first quarter of last year and has not been restarted since. The “A” furnace has daily iron making capacity of 3,600 tons – or 1.31 million tons per year. And U.S. Steel said it would begin idling iron and steelmaking facilities at its Great Lakes Works near Detroit around April 2020. Great Lakes Works had previously operated three blast furnaces with combined annual capacity of 11,450 tons of iron per day – or 4.18 million tons per year.
In other words, U.S. Steel is contributing significantly less hot metal to the market now — to the tune of 5.49 million tons per year.
To put that in context, Big River Steel added 1.65 million tons per year of new capacity to the U.S. market when it doubled output at its flat-rolled steel mill in Osceola, Ark., late last year and early this year. Steel Dynamics Inc.‘s new flat-rolled mill in Sinton, Texas, is expected to come online in late summer with a capacity of 3 million tons per year. And Nucor’s expansion of its steel mill in Ghent, Ky., (Gallatin) is expected to add 1 million tons of new capacity to the market in 2022. In short, three major EAF expansions are necessary to offset capacity that U.S Steel alone has idled in recent years.
And that shortage is more pronounced if one looks further back in time to include the significant blast furnace capacity idled by Cliffs and the steelmakers it has acquired over approximately the last year. (Namely, ArcelorMittal USA and AK Steel.)
ARTICLE CONTINUES BELOW
{loadposition reserved_message}
The Amanda furnace at Cliffs’ Ashland Works in Kentucky and the No. 3 furnace at its Indiana Harbor steelmaking complex in northwest Indiana have been permanently idled. They have combined capacity of 8,500 tons of iron per day, or 3.10 million tons per year.
ArcelorMittal USA, the former owner of Indiana Harbor, announced in November 2019 that it would idle the No. 3 furnace, according to Inside Indiana Business. It has since been permanently idled.
And AK Steel, the former owner of Ashland Works, announced in October 2015 that it would temporarily idle the Amanda blast furnace. The company cited “challenging market conditions” at the time. That idling has since become permanent.
Steel prices in the meantime have continued to rise on strong demand, long lead times and limited domestic supplies. Buyer sources report that they’ve become resigned to higher prices and have instead shifted their focus to procuring enough steel to run their businesses amid continued strong demand.
SMU’s benchmark hot-rolled coil price stood at $1,570 per ton ($78.50 per cwt) when this article was filed, up 59.3% from $985 per ton at the beginning of the year and more than quadruple $390 per ton in late October 2015 – after the idling of Ashland Work’s blast furnace was announced. Lead times were at 10.81 weeks, up 37.3% from 7.87 weeks at the beginning of the year and up nearly fourfold from 2.82 weeks in late October 2015.
By Michael Cowden, Michael@SteelMarketUpdate.com

Michael Cowden
Read more from Michael CowdenLatest in Steel Mills
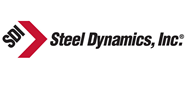
Millett sees tariffs, CORE case benefiting SDI
Steel Dynamics' top exec thinks Trump’s tariff policies, as well as the results from the recent CORE case, will prove advantageous to the Fort Wayne, Ind.-based steelmaker and aluminum company.
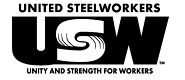
USW digs in on opposition to USS-Nippon deal
“We remain deeply concerned about the national and economic security implications of the subject transaction,” the union stated in the letter dated April 21.
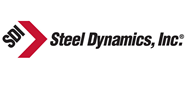
SDI’s Q1 earnings slump on-year, but up sequentially
SDI earnings slip in first quarter year over year, but are up sequentially.
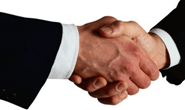
POSCO inks MoU with Hyundai on Louisiana EAF mill
POSCO has signed a Memorandum of Understanding (MoU) with Hyundai Motor Group that includes an equity investment in Hyundai’s previously announced EAF mill set to be built in Louisiana.
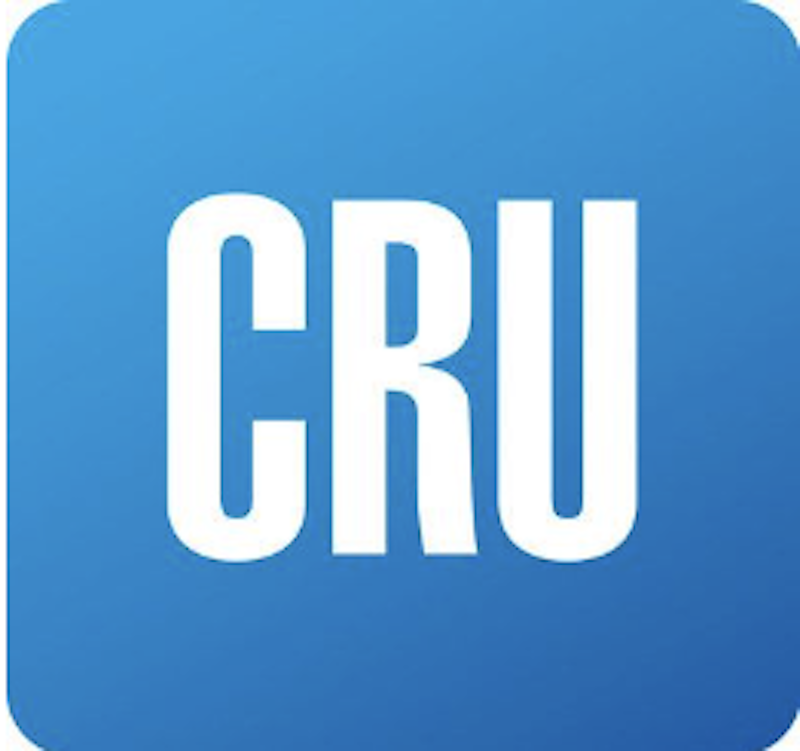
CRU: Tata Steel looks to shed 1,600 jobs in the Netherlands
The company said, “The challenging demand conditions in Europe driven by geopolitical developments, trade and supply chain disruptions and escalating energy costs have affected the operating costs and financial performance."