SMU Community Chat
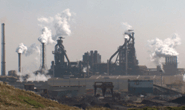
U.S. EAFs Have Head Start in Race to Go Green: CRU's Smith
Written by Michael Cowden
March 17, 2021
U.S. electric-arc furnace mills have a leg up on the world when it comes to meeting new carbon emissions standards–for now, said CRU Senior Analyst Ryan Smith.
That’s according to a “carbon curve” Smith presented that is part of CRU Group’s Emissions Analysis Tool.
The carbon curve is similar to the cost curve many steel industry participants may be familiar with, but it measures mills in terms of CO2 emissions per tonne of steel made rather than in terms of costs per tonne of steel produced.
That curve is relevant now because the world is taking a hard look at decarbonizing a steel industry that accounts for 8% of total global CO2 emissions. Most developed countries already have announced or begun implementing plans to significantly reduce emissions, Smith said
In the U.S., the Biden administration has rejoined the Paris Agreement amid “whispers” of policies aimed at putting a price on carbon in the U.S., something that has long been standard practice in Europe, he noted.
“There is real and growing pressure on steel producers globally to reduce their emissions,” Smith said.
In other words, being environmentally friendly is no longer just a catchphrase for marketing departments. “In some companies, there is executive pay linked to emissions targets in their value chain,” he said.
Smith made the comments during a Steel Market Update Community Chat webinar on Wednesday, March 17. SMU is a part of the CRU Group. This article comes from that webinar as well as a prior conversation between Smith and SMU.
You can click here to listen to a recording of the webinar.
The U.S. Scene Is Green
U.S. mills, especially domestic EAF producers, have among the lowest carbon emissions in the world thanks to abundant and cheap natural gas as well as plentiful scrap supplies. And so the first quartile of the carbon curve, meaning the mills emitting the least CO2, is populated largely by U.S. EAF steelmakers, Smith said.
There is no getting around the fact that integrated steelmaking emits more carbon. “Things like on-site sintering, on-site pelletizing … coking and iron making account for a majority of the emissions within the industry,” Smith said.
So why doesn’t the global steelmaking industry switch en masse to EAF steelmaking to reduce pollution?
“There is just not enough scrap supply in the world to meet the level of steel demand globally,” Smith said. Namely, there is a scrap gap of approximately one billion metric tonnes that needs to be met by ore-based metallics such as traditional hot metal or alternatives such as DRI.
That’s not to say the U.S. blast furnaces are at the high end of the curve. Cleveland-Cliffs’ Middletown Works in Ohio, for example, is almost in the first quartile in terms of carbon emissions, meaning that its carbon output is very low compared to most mills abroad.
That’s thanks in part to cheap natural gas in the U.S., which domestic blast furnaces operators use as fuel in their furnaces instead of the carbon-intensive pulverized coal that is injected into blast furnaces in Asia and Europe, Smith said.
U.S. integrated mills also charge their furnaces almost entirely with pellets as opposed to the sinter feed and lump ore more commonly used abroad. The latter have higher amounts of alumina and silica, which increases emissions, he said.
And deep underground mines abroad, while they might contain richer deposits of iron ore than places like Minnesota’s Iron Range, are not necessarily less carbon intensive. The reason: Deep mines tend to release more methane than surface mining, which results in a worse outcome for the climate, Smith said.
China is Not Green, But It Will Be
The high end of the curve, representing steel mills and mines that emit the most CO2, is comprised in large part of mills in India, which rely heavily on a coal-fired power grid. That’s not to say that India doesn’t care about the environment. But rather the world’s second most populous country has prioritized growth as it develops, putting environmental concerns on the backburner, a pattern typical of developing countries, Smith said.
Producers in China also generally emit far more than mills in the United States and Europe. That’s partly due to the fact that China is the largest steel producer in the world. It’s also because China, like much of the rest of the world, doesn’t have the luxury of ample ferrous scrap and cheap natural gas enjoyed by U.S. mills, he said.
But the United States’ scrap benefit might not endure in the decades ahead, which are expected to see China gain a deeper well of domestic scrap. “In the next few years, the U.S. will maintain its (advantageous) CO2 position. But longer term, as scrap–particularly in China–becomes more available, (lower CO2) should be something the U.S. steel industry looks at,” Smith said.
Europe and the Case for Hydrogen Steelmaking
European mills are toward the middle of the carbon curve. They have made great strides in reducing carbon emissions from a continental industry characterized mostly by integrated steelmakers. But a step-change is needed if they are to meet the EU’s increasingly stringent carbon standards, he said.
That explains why some European mills are investing heavily in technologies such as hydrogen-based steelmaking. Such processes would see direct-reduced iron (DRI) produced in a reduction unit powered by renewables and then melted in an EAF, also powered by renewables. That would dramatically reduce carbon emissions compared to traditional integrated steelmaking, which necessitates heavy use of carbon-emitting coking coal.
The problem: The capital investments required to make such a switch dwarf the costs of even expensive projects such as a blast furnace reline. And steel made from carbon-free technologies costs over $200 per tonne more to produce compared to material made via traditional means. That’s in large part because producing hydrogen requires “immense” amounts of electricity even compared to EAF steelmaking.
“Decarbonizing is going to increase costs. That’s going to lead to higher steel prices.” And that’s true whether one is talking hydrogen-based steelmaking or carbon capture and sequestration, Smith said.
Carbon Border Taxes
Government subsidization or intervention in power markets could offset those costs as could a carbon border tax. But a lot hinges on exactly how a carbon border tax might work in practice. If carbon border policies are applied only to steel and not to downstream products, it could incentivize manufacturers to move elsewhere, where steel costs are lower, Smith said.
Another reason for caution: It’s not clear that all alternative iron-making technologies currently being explored will pan out. Such processes tend to proliferate when steel and ore prices are high. But enthusiasm and available capital tends to wane when tags fall, he said.
In the current market environment, one characterized by record high prices, increased costs might be manageable. And money might be available to research new technologies. The problems will come when the steel market inevitably resets to more normal conditions, which are often cash-flow neutral for steelmakers, Smith said.
As for cross-border trade, it’s too early to say how a carbon border tariff might impact flows. It’s possible that a specific nation would be assessed a certain carbon tariff and that an individual steelmaker could apply for a lower rates. That might be the case in the U.S., for example, were an EAF steelmaker might be able to ask for a lower carbon tariff than an integrated mill, he said.
That process could be broadly similar to how antidumping cases work in the U.S., where a country-wide rate is determined but where individual mills might receive higher or lower margins depending on their particular circumstances.
While the details of a carbon border tariff aren’t yet certain, this is: What’s needed to facilitate a wholesale shift to carbon-neutral steelmaking is a much higher price for carbon than prevailing market prices. “Carbon prices need to be hundreds of dollars more than where they are currently,” Smith said.
Carbon prices in Europe are approximately $40 per tonne, higher than usual but still “nowhere near high enough to incentivize a wholesale shift to low CO2 steel production,” he said.
By Michael Cowden, Michael@SteelMarketUpdate.com

Michael Cowden
Read more from Michael CowdenLatest in SMU Community Chat
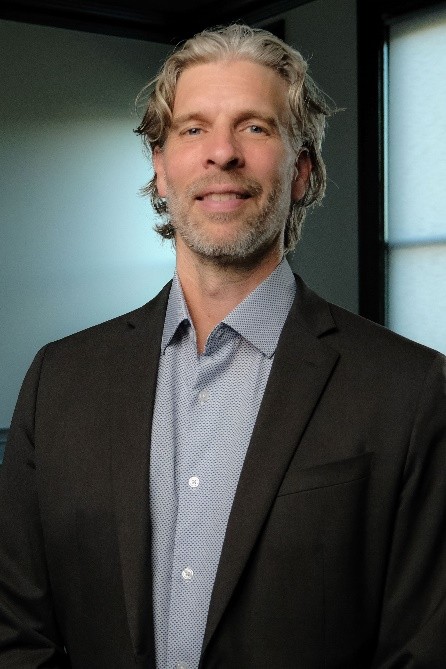
Join SMU on April 30 for a Community Chat with Bilstein Cold Rolled Steel CEO Brent Wilson
Bilstein Cold Rolled Steel LLC CEO Brent Wilson will be the featured speaker on the next SMU Community Chat webinar on Wednesday, April 30, at 11 am ET. You can register here. Reminder: The live webinar is free to attend. A recording will be available only to SMU subscribers. About Bilstein and Wilson Bilstein Cold […]
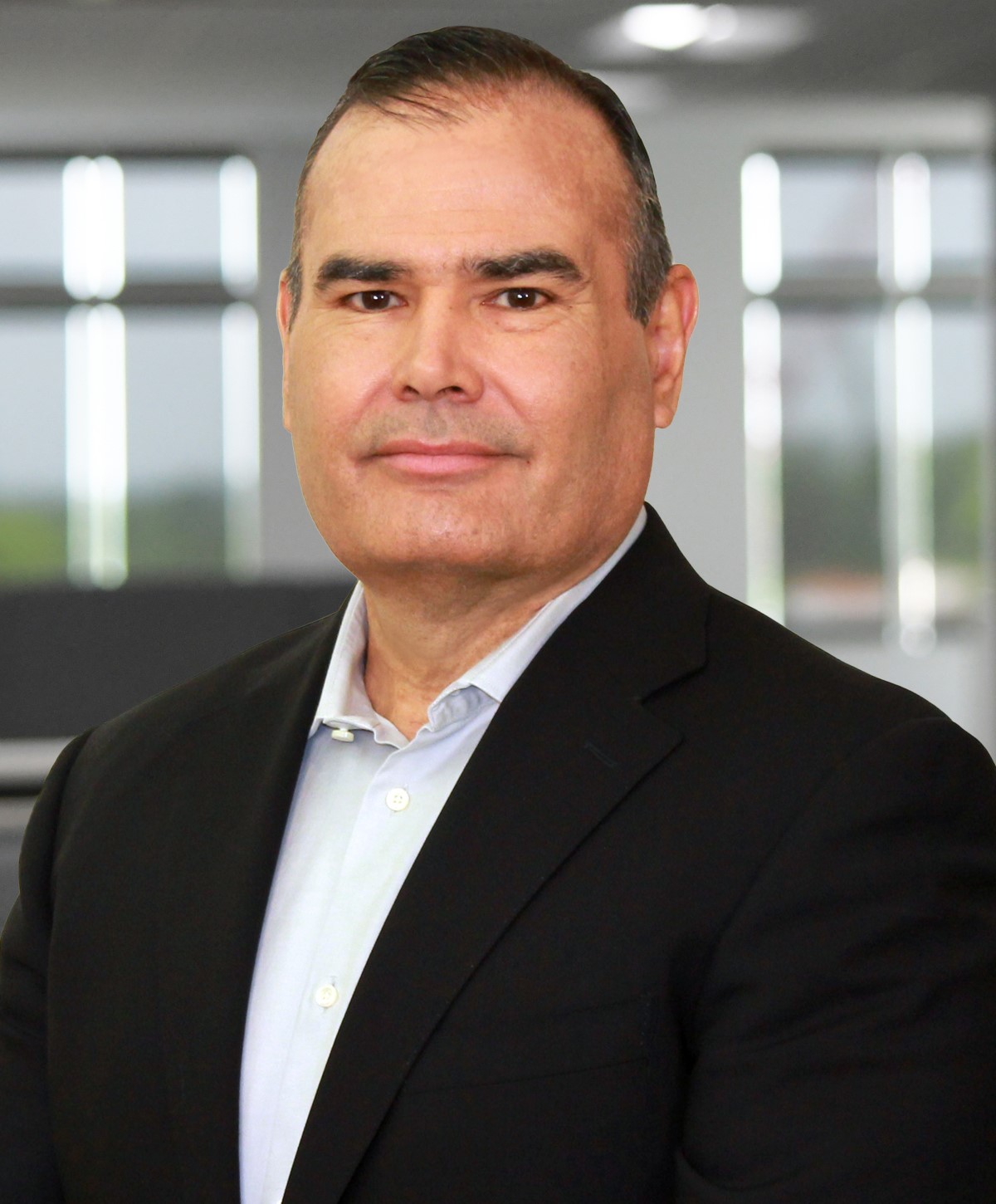
Join us for the April 9 Community Chat with Algoma Steel CEO Michael Garcia
During the chat, we’ll discuss trends in the North American sheet and plate markets, as well as the unique aspects of the Canadian market. We’ll talk all thing tariffs — and the timing couldn’t be better in the wake of Liberation Day on April 2.
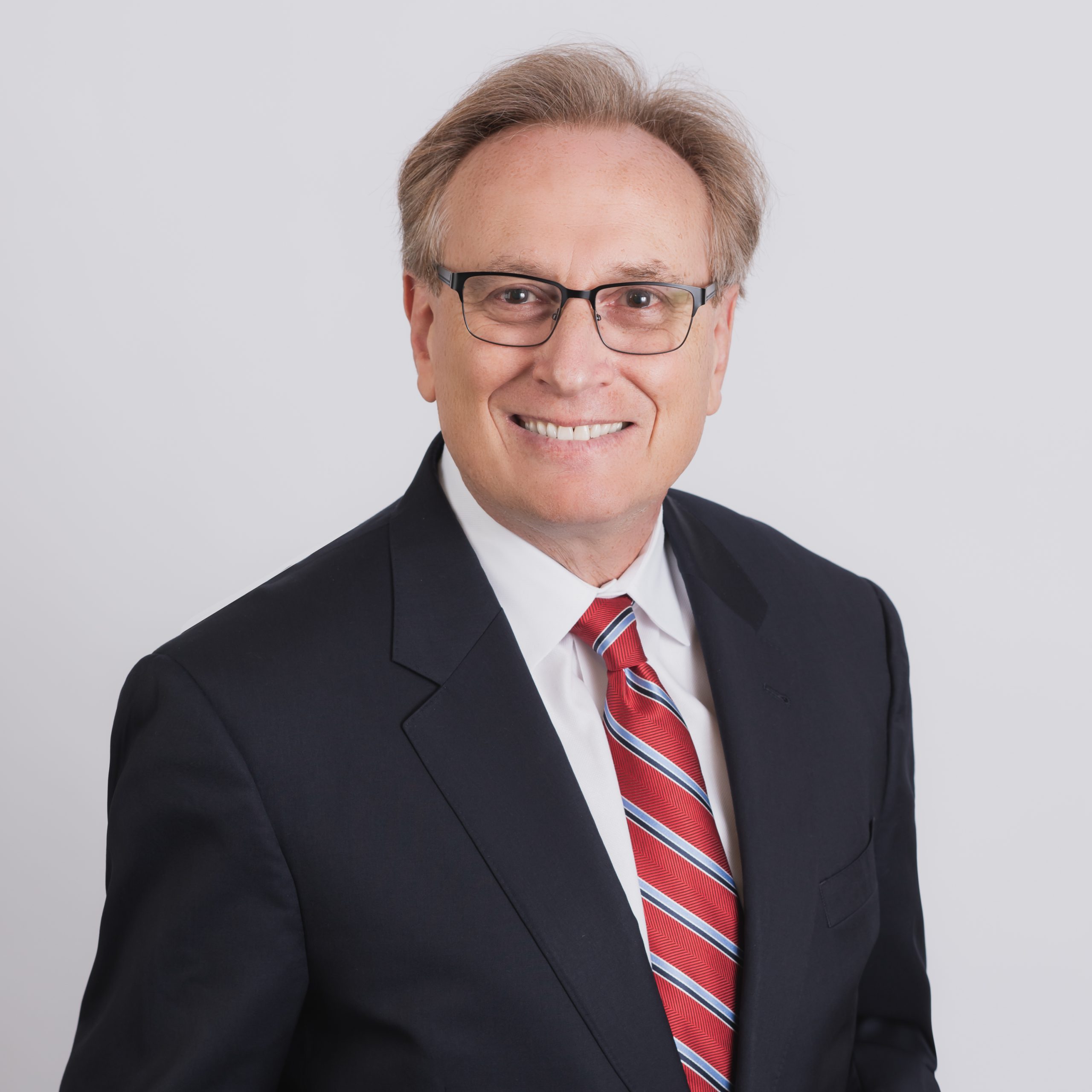
SMU Community Chat: Alan Price unpacks latest in rapidly shifting tariff terrain
International trade attorney Alan Price sat down with SMU to unpack the latest developments in Trump’s tariff merry-go-round.
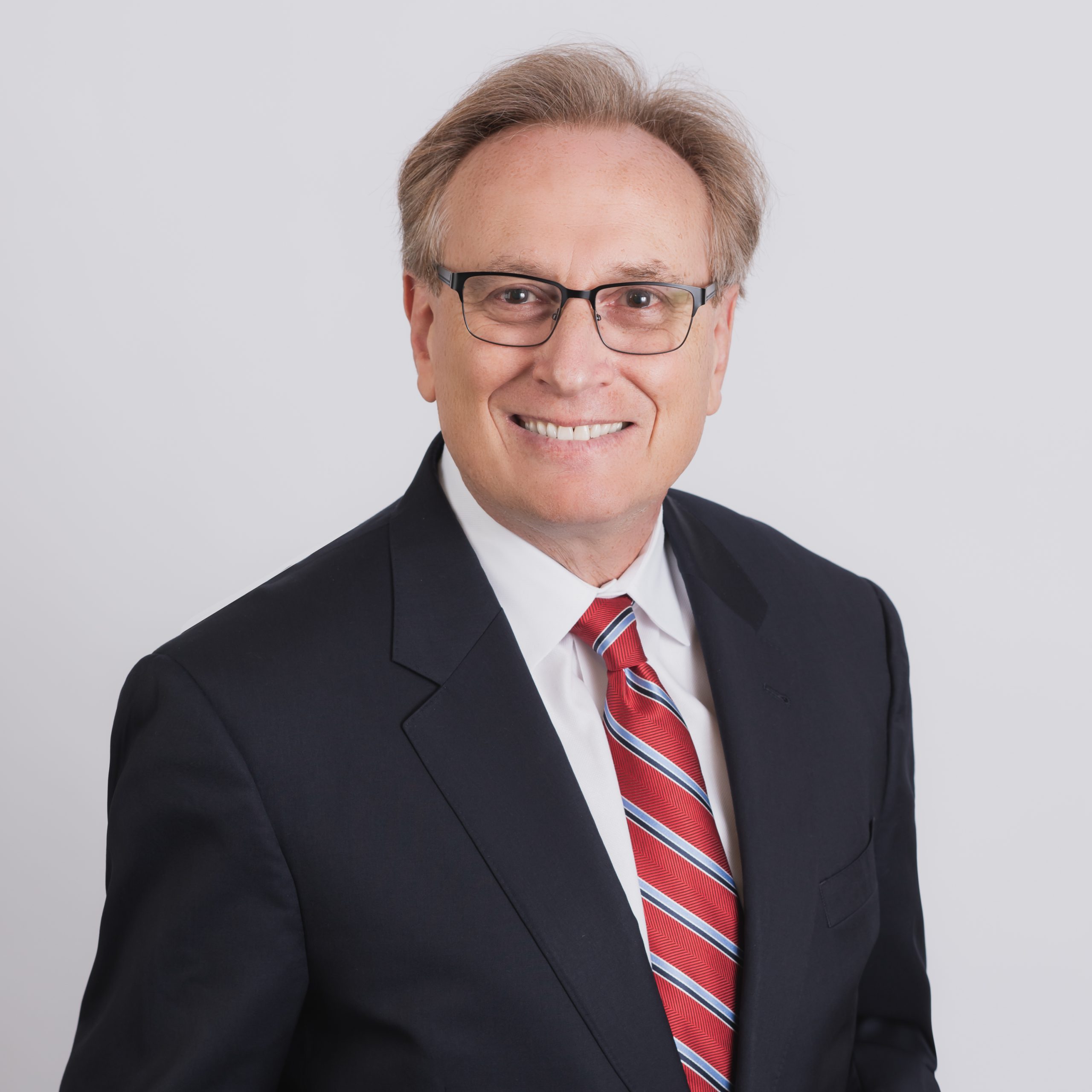
Join SMU for a Community Chat on March 13 With Wiley Trade Attorney Alan Price
Wonder what the fallout from all the Trump tariffs might be? A manufacturing renaissance? A post-WWII order in ashes? Or something a little more down the middle? Then register for our next Community Chat on Thursday, March 13 at 11 am ET. Yes, you read that correctly, SMU is shattering precedent by holding a Community Chat on a day that is not Wednesday. Our featured speaker will be Alan Price, a leading trade attorney at Wiley and someone whose columns you read regularly in SMU.
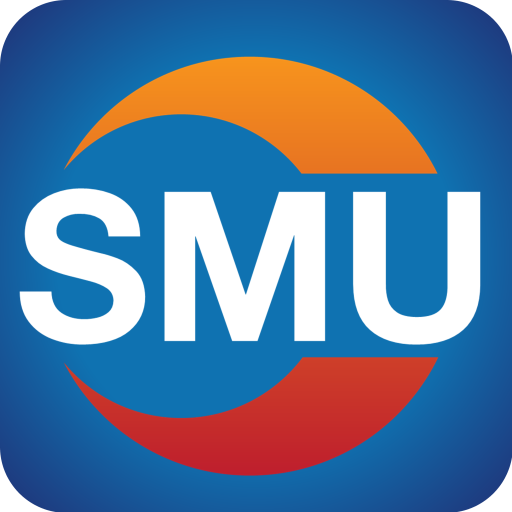
SMU Community Chat: CRU’s Josh Spoores looks out over the Trump 2.0 battlefield
SMU Community Chat with CRU's Josh Spoores.