Steel Products Prices North America
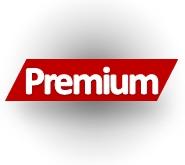
Raw Materials Prices: Iron Ore, Coking Coal, Pig Iron, Scrap, Zinc
Written by Brett Linton
May 4, 2020
Prices of steelmaking raw materials all declined in April, reflecting the initial impact of coronavirus shutdowns and the idling of steelmaking facilities all over the world. Generally speaking, rising supplies and lower demand are likely to keep downward pressure on iron ore, coking coal, pig iron, scrap and zinc in the months to come.
Table 1 summarizes the price changes through April 30 of the five materials considered in this analysis. It reports the month/month, three months/three months and year/year changes on a percentage basis.
Iron Ore
The Chinese import price of 62% Fe content iron ore fines moved up and down during the first quarter within a $13 range, declining to $83.50/dmt by the end of April from the quarter’s high of $96.70/dmt in late January. Figure 1, below, shows the price of 62% Fe delivered North China since January 2018.
Coking Coal
The price of premium low volatile coking coal FOB east coast of Australia declined sharply in the month of April by $43/dmt to $118.0/dmt. Coking coal prices are at their lowest levels in more than two years (Figure 2) below.
Pig Iron
Most of the pig iron imported to the U.S. currently comes from Russia, Ukraine and Brazil. This report summarizes prices out of Brazil and averages the FOB value from the north and south ports. The latest data, from April 1, shows an average pig iron price of $302.50 per metric ton, down from $325.00 at the beginning of March. Pig iron prices have declined erratically since hitting a peak of $400.00 per ton in June 2018, (Figure 3) below.
Scrap
Hot rolled steel prices fluctuate up and down with the price the mills must pay for their raw materials. Changes in the relationship between scrap and iron ore prices offer insights into the competitiveness of integrated mills, whose primary feedstock is iron ore, versus the minimills, whose primary feedstock is scrap. Prices for both prime/busheling and obsolete/shredded scrap have moved down in the first quarter. Figure 4, below, shows the relationship between shredded and busheling, both priced in dollars per gross ton in the Great Lakes region.
Figure 5, below, shows the recent spread between the price of iron ore, at $83.50 per dry metric ton, and shredded scrap at $225 per gross ton.
To compare the two, Steel Market Update divides the shredded scrap price by the iron ore price to calculate a ratio, (Figure 6) below. A high ratio favors the integrated/BF producers, a lower ratio favors the minimill/EAF producers. As the 2.7 ratio shows, the recent declines in the price of shredded scrap, which have outpaced the declines in iron ore, have added to the minimills’ competitive cost advantage.
Figure 7, below, shows how the price of hot rolled steel tracks with the price of shredded scrap. Shred traded down by approximately $55 in April, which allowed the mills to drop the price of hot rolled by about $40 in the same time period and remain competitive.
Zinc
Zinc, used to make galvanized and other products, declined in price for much of the first quarter (Figure 8), below. The LME cash price per pound of zinc as of April 30 was 0.8689, down about 25 cents a pound from a first-quarter peak of approximately $1.12 on Jan. 20. The price of zinc factors into the coating extras charged by the mills for galvanized products. Cheaper zinc has contributed to the declining prices of some finished steel products. Likewise, cheaper aluminum has benefited Galvalume prices.
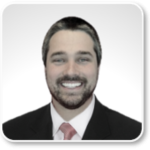
Brett Linton
Read more from Brett LintonLatest in Steel Products Prices North America
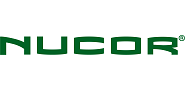
Nucor slows HRC price climb with $5/ton increase
After eight weeks of double-digit price increases on hot-rolled (HR) coil, Nucor slowed the price rise this week with an increase of $5 per short ton.
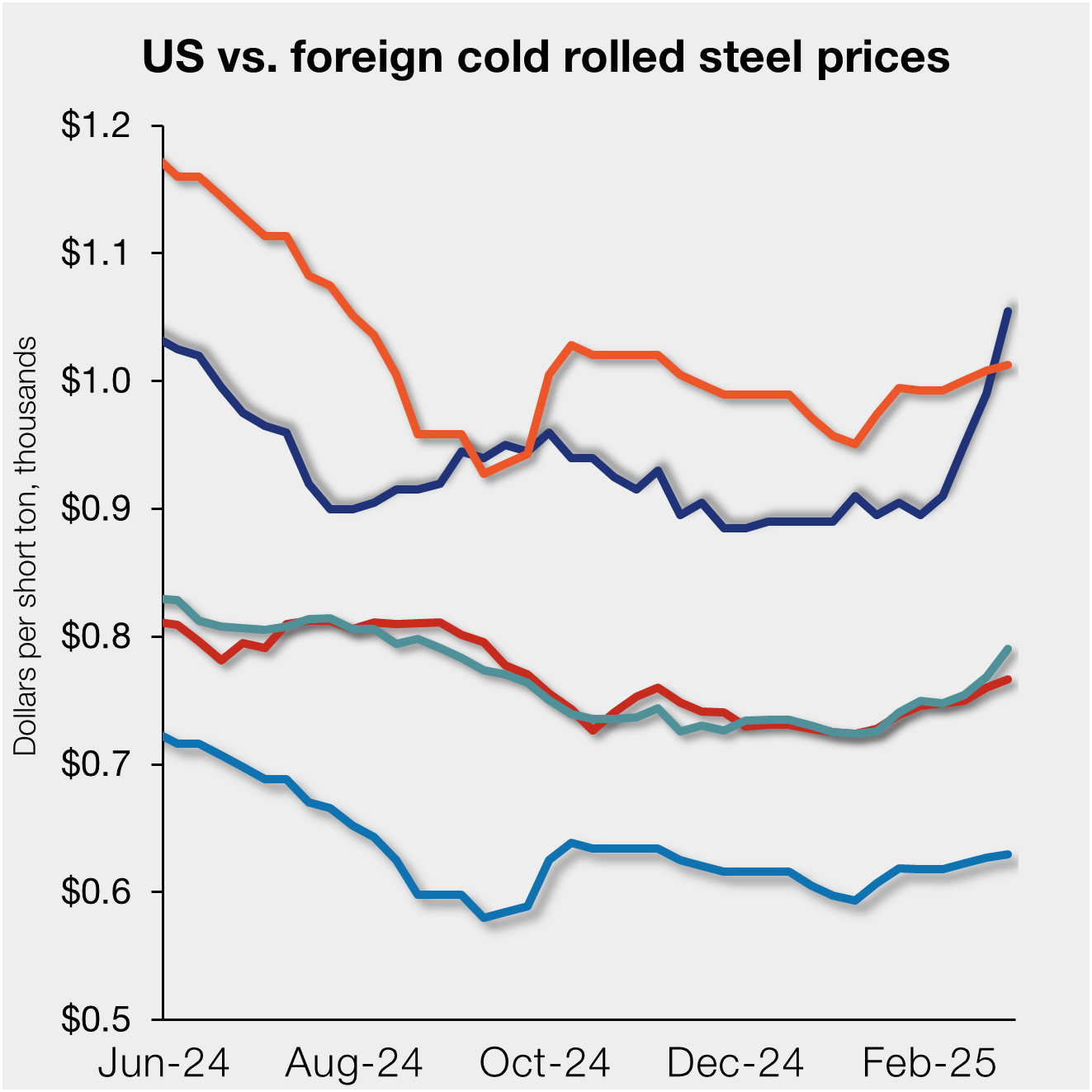
Domestic CRC prices surge ahead of imports
The price spread between stateside-produced CR and imports reached its widest margin in over a year.
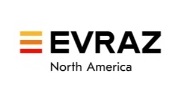
Evraz raises plate prices $160/ton
Evraz North America (NA) has followed Nucor and SSAB with a plate price increase of its own: up $160 per short ton (st). The increase was effective immediately for all new orders of carbon, high-strength low-alloy, and normalized and quenched-and-tempered plate products, as well as for hot-rolled coil, the steelmaker said in a letter to […]
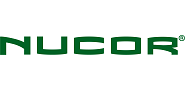
Nucor lifts HR coil to $820/ton
Nucor has increased its consumer spot price (CSP) for hot-rolled (HR) coil for a fourth consecutive week.
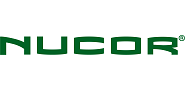
Nucor pushes HR spot price to $790/ton
Nucor increased its consumer spot price (CSP) for hot-rolled (HR) coil to $790 per short ton (st) on Monday, Feb. 10 – a $15/st bump vs. last week. The Charlotte, N.C.-based company has raised its weekly CSP by $40/st over the past three weeks after maintaining tags at $750/st since Nov. 12, according to SMU’s […]