Steel Mills
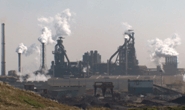
SMA Claims the High Ground in Environmental Debate
Written by Tim Triplett
February 18, 2020
While America’s integrated steel producers are investing millions in R&D to reduce harmful emissions from their steelmaking process, the nation’s minimill steel producers have already claimed the high ground for environmental stewardship.
Integrated mills and their blast furnaces heat iron ore and coking coal at high temperatures to produce high-quality virgin pig iron and steel. This centuries-old process releases high levels of carbon dioxide into the atmosphere, one of the primary greenhouses gases blamed for climate change. Minimills, which date back roughly 50 years, use electric arc furnaces to remelt ferrous scrap. They note with pride that not only does EAF steelmaking emit far less CO2, it also recycles and repurposes scrap metal from the consumer and industrial waste streams—a dual benefit to the environment.
The Steel Manufacturers Association in Washington is the trade group representing the EAF steelmakers. “SMA members are at the forefront of sustainable steelmaking. We have the lowest CO2 footprint in the world,” said SMA President Philip Bell.
Unlike the American Iron and Steel Institute, which promotes collaborative research to help its integrated-mill members share the cost of new technologies to reduce emissions, SMA does not see R&D as a big part of its mission, since EAF steelmaking is inherently “green,” relatively speaking. SMA members are actively engaged in R&D of their own to improve the process further.
Data collected by the U.S. EPA since 2010 tells the story, said Eric Stuart, SMA vice president of energy, environment and infrastructure policy. Based on the most recent data from 2018, a year in which U.S. minimills produced 58.3 million tons of steel, EAF steelmaking generated 12.9 million tons of CO2 emissions. In comparison, the blast furnace process used by the integrated mills emitted 49.4 million tons of CO2 in the production of 28.7 million tons of steel. “EAFs produce just one-third to one-quarter of the emissions of BOFs for the same ton of steel. Those numbers (see chart) make it stark and clear—we are the best form of production for making steel and minimizing CO2 emissions,” Stuart said.
As integrated producers are quick to point out, those figures do not include emissions generated in the production of the electricity needed to power the minimills’ electric arc furnaces.
That’s why much of the R&D done by minimills is focused on the use of renewable energy sources to power their EAFs. For example, EVRAZ North America is using solar energy to run its mill in Pueblo, Colo.; Nucor is using wind power at its new micromill in Sedalia, Mo.; and SSAB has set a goal to get to zero carbon steel production in the U.S. by 2026, and is working on hydrogen-based steel production in other parts of the world.
SMA has been a supporter of the Trump administration’s trade actions designed to reduce imports of foreign steel. While the main goal is to prevent China and other nations from dumping steel at predatory prices in the U.S., the environment benefits as well as more of the steel consumed in the U.S. is produced in the U.S. using the most environmentally friendly steelmaking process.
The United States has the largest concentration of EAF mills in the world. China, the world’s largest steel producer, is largely reliant on blast furnace technology. “When we import foreign goods, we are importing the emissions that come with them,” said Annie Stefanec, SMA manager of communications and public affairs. “Here in the U.S. we make a cleaner version of steel using the EAF process, which helps the environment not just in the U.S. but globally. Competition from bad actors takes a toll on the environment as well as the domestic steel industry.”
Various countries, including the EU and Canada, and even certain states within the U.S., are considering or have implemented carbon taxes and carbon trading schemes to incentive companies to use less fossil fuel and reduce GHG emissions. So far, the United States is not one of them. SMA is among the many opposed to taxing emissions.
“In the case of the U.S. steel industry, we don’t have to go down that road. Our industry is already more sustainable with emissions significantly lower than global steel producers,” Bell said.
Stuart added: “In 2009, the European Union started setting up a cap and trade program that chased one of every three tons of production out of the EU in the first five years. That was the wrong way to deal with the issue.”
President Trump is often criticized for withdrawing the U.S. from the Paris Climate Accord, but it made sense, Bell continued. “Why would we engage in legislation and regulation that makes our industry less competitive globally. Often underreported is that countries like China and India were not even subject to the standards in the accord, yet they are among the largest exporters of steel and the largest producers of CO2 emissions in the world. We’re already operating sustainably. We already have the cleanest steel in the world. Why do we need to have cap and trade or carbon taxes?”
The debate over climate change has been raging for decades. Why has this become such a hot topic lately? “Part of it is consumer-driven,” said Stefanec. “You are seeing a huge shift in our social landscape toward more environmental messaging. Given the option, people are choosing to buy products that are marketed as more sustainable and environmentally friendly.”
“It’s also shareholder-driven,” added Bell. “A lot of investors want to invest sustainably as part of their corporate social responsibility platforms.
“When you look at how our members use raw materials, water, energy and process technology that not only reduces CO2 emissions but increases recycled content, the U.S. steel industry is right in line with sustainable investment.”
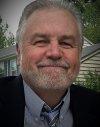
Tim Triplett
Read more from Tim TriplettLatest in Steel Mills
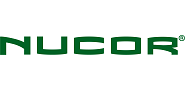
Nucor names Batterbee, Bledsoe to HR roles
Nucor Corp. has promoted Thomas J. Batterbee to the position EVP of human resources and talent and appointed Elizabeth Bledsoe to the newly created position of president of human resources and talent.
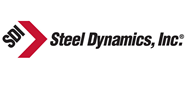
Millett sees tariffs, CORE case benefiting SDI
Steel Dynamics' top exec thinks Trump’s tariff policies, as well as the results from the recent CORE case, will prove advantageous to the Fort Wayne, Ind.-based steelmaker and aluminum company.
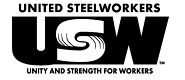
USW digs in on opposition to USS-Nippon deal
“We remain deeply concerned about the national and economic security implications of the subject transaction,” the union stated in the letter dated April 21.
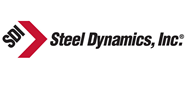
SDI’s Q1 earnings slump on-year, but up sequentially
SDI earnings slip in first quarter year over year, but are up sequentially.
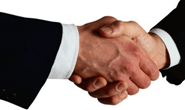
POSCO inks MoU with Hyundai on Louisiana EAF mill
POSCO has signed a Memorandum of Understanding (MoU) with Hyundai Motor Group that includes an equity investment in Hyundai’s previously announced EAF mill set to be built in Louisiana.