Steel Products Prices North America
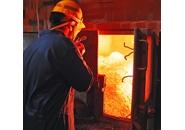
Potential Pig Iron Facility in Wyoming
Written by Sandy Williams
November 18, 2014
The Wyoming Business Council and JR Simplot Company are hoping to revive a shuttered iron ore mine and build a $500 million iron ore concentrator and pig iron production facility in central Wyoming.
The plant would produce cast pigs with a carbon content of 3.5 percent made from low grade taconite ore with an iron content of about 30 percent.
The mine in Atlantic City, Wyoming is owned by agribusiness company JR Simplot and estimated to have 150-200 million tons of reserves along with 20 years of tailings suitable for reprocessing. The reserves can support a minimum project life of 40-50 years at an annual capacity of around 1 million tons.
The site offers access to low-cost power and low cost natural gas as well as rail service to eastern steel producers, said Rex Lewis, co-chairman of the Wyoming Business Council Board of Directors.
“There’s also the attraction of having the state working for you rather than against you,” said Lewis.
Peter Wright, president of Dallas-based Steel Market Analysis and a Steel 101 instructor and writer for Steel Market Update, is working with the Wyoming Business Council to find a partner for JR Simplot. The company is experienced in mining potash for fertilizers and could supply prepared ore to a potential venture partner.
Wright says the project may interest private investors looking to enter the merchant pig iron market as well as steel mills looking to secure their own source of iron ore.
Projected customers would likely be mini-mills operating electric arc furnaces (EAF) making flat-rolled steel, although iron foundries, wire rod and special bar quality (SBQ) steelmakers are also potential customers or partners.
Wright says pig iron is superior to DRI and HBI in electric arc steelmaking due to a variety of reasons.
“The most important one,” said Wright, “is that pig iron has had all the nonmetallic silica and alumina removed. In DRI these can be as high as 6 percent but even if as low as 3 percent these impurities result in higher energy consumption in an EAF because they increase the slag volume. This also reduces furnace productivity.
“Oxygen content is a lesser factor. When DRI is added to an EAF it causes a reaction in the furnace which can cause slag run off and loss of yield. DRI does not travel well either. It is pyrophoric which means it can spontaneously combust and its density is lower than pig iron. Finally pig iron contains about 3.5% carbon which is a fuel and reduces energy consumption in the EAF.”
The project will benefit from the transition of from traditional blast furnaces to electric arc furnaces which require low residual iron units. EAF melting has increased from 23.9 percent in 1970 to 60.6 percent in 2013, said Wright.
Wright noted that Big River Steel, located in Arkansas, will be adding an EAF to the market and ArcelorMittal is considering an EAF for its Calvert mill. US Steel also plans to replace the Fairfield blast furnace with an EAF.
Recycled scrap is also used in electric arc furnaces but contains contaminants like copper, nickel, chromium, molybdenum and tin that limit the applications that sheet steel can be used for if they are present.
“Therefore it is necessary to dilute this scrap with pig iron or DRI,” said Wright. “Pig iron imports in 2013 were about 4.5 million tons. The Wyoming project is designed to replace a portion of those imports.”
The Wyoming Business Council is soliciting feasibility studies and looking for potential joint venture partners. An operating date has been tentatively set for 2019. The timetable, says Wright, includes finding a partner by third quarter 2015, two years for permitting, and 18 months of construction until the plant is operational.
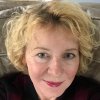
Sandy Williams
Read more from Sandy WilliamsLatest in Steel Products Prices North America
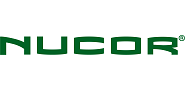
Nucor slows HRC price climb with $5/ton increase
After eight weeks of double-digit price increases on hot-rolled (HR) coil, Nucor slowed the price rise this week with an increase of $5 per short ton.
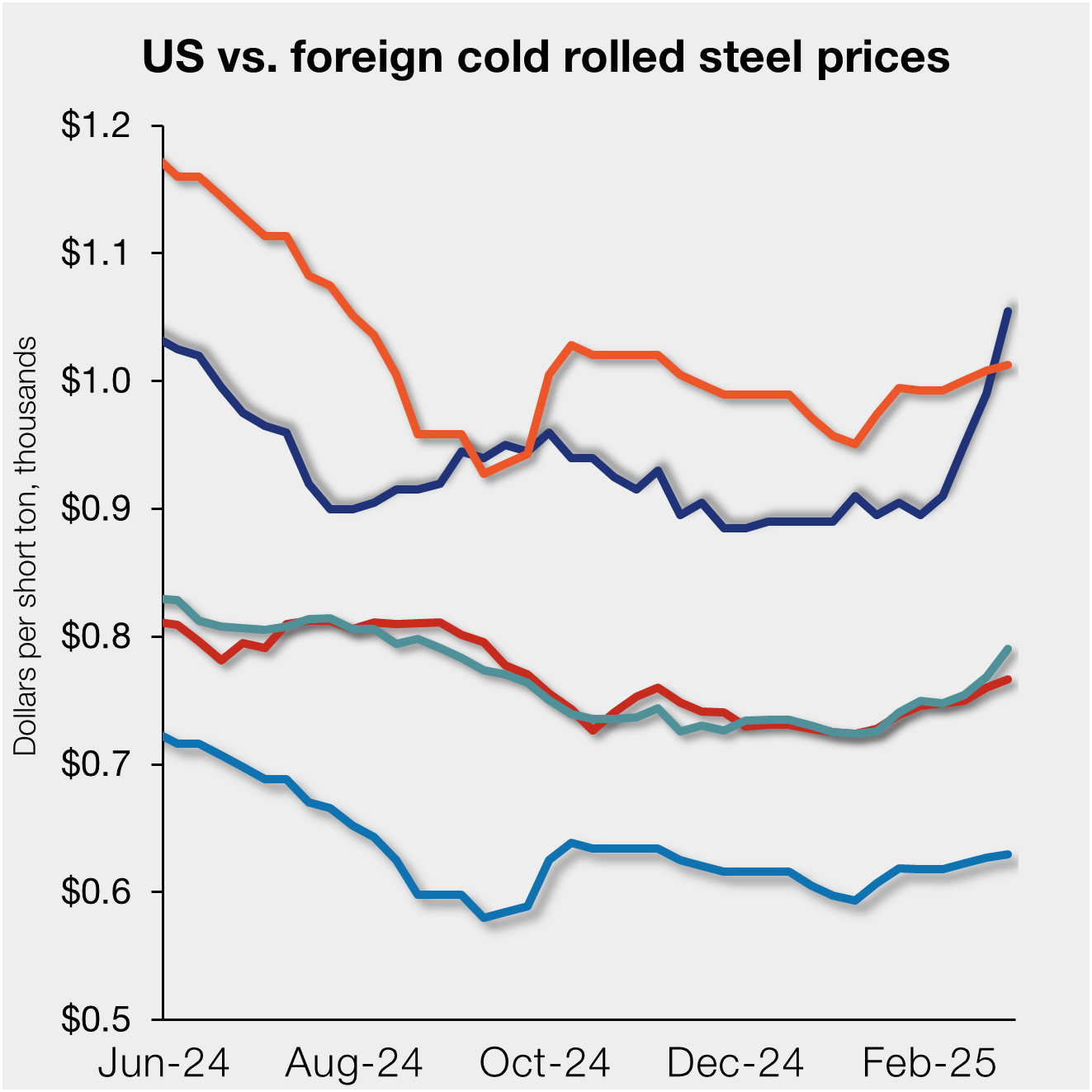
Domestic CRC prices surge ahead of imports
The price spread between stateside-produced CR and imports reached its widest margin in over a year.
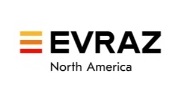
Evraz raises plate prices $160/ton
Evraz North America (NA) has followed Nucor and SSAB with a plate price increase of its own: up $160 per short ton (st). The increase was effective immediately for all new orders of carbon, high-strength low-alloy, and normalized and quenched-and-tempered plate products, as well as for hot-rolled coil, the steelmaker said in a letter to […]
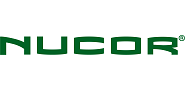
Nucor lifts HR coil to $820/ton
Nucor has increased its consumer spot price (CSP) for hot-rolled (HR) coil for a fourth consecutive week.
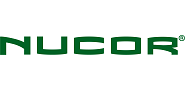
Nucor pushes HR spot price to $790/ton
Nucor increased its consumer spot price (CSP) for hot-rolled (HR) coil to $790 per short ton (st) on Monday, Feb. 10 – a $15/st bump vs. last week. The Charlotte, N.C.-based company has raised its weekly CSP by $40/st over the past three weeks after maintaining tags at $750/st since Nov. 12, according to SMU’s […]