Steel Products
DRI – What is it and is it a Game Changer for the Industry?
Written by Sandy Williams
March 13, 2013
Written by: Sandy Williams
This year Nucor plans to spend $280 million on its Louisiana DRI facility and approximately $260 million towards its natural gas related investments. Essar Steel Minnesota is in talks to build a joint venture DRI plant. Voestalpine and Northstar Bluescope Steel are both considering DRI facilities. Severstal just postponed a DRI project in Trinidad and Tobago.
Just what is DRI and why all the interest in it?
Direct Reduced Iron, or DRI, is created by heating iron ore with natural gas to produce pellets high in iron ore content (typically >90%) that can be fed into an electric arc furnace. The pellets can replace high grade scrap and pig iron used in an EAF (or a blast furnace). What fuels steel industry interest is the savings, both financial and environmental, that are realized by using cheap natural gas in lieu of coking coal or met coal. Bank of America Merrill Lynch projects 20M tons of new DRI capacity will be available by the end of the decade, lowering costs to make steel by at least $50 per ton.
Natural Gas and DRI production
High natural gas costs pre-empted early attempts in the 1970s and early 2000s to establish profitable DRI projects, but the recent availability of cheap, plentiful gas from shale depositories and fracking technology has assured success for today’s DRI production.
Nucor decided to assure its gas supply through agreements with Encana Oil & Gas to drill for onshore natural gas in Canada and the United States. The gas produced from the two investment programs is expected to provide all the needs of its two steel plants plus two DRI facilities or, alternatively, three DRI plants for the next 20 years.
Bank of America Merrill forecasts modest natural gas price rises over the next few years averaging $3.75/mmBTU in 2013 and $4.30/mmBTU in 2014E due to a switch from coal to gas. A lock in of natural gas, similar to Nucor’s, could result in a gas cost of $3/mmBTU for the next 20-40 years
DRI and EAF
Electric arc furnaces are beginning to replace traditional blast furnace operations currently at the rate of 60% EAF/40% BOF. Unlike a BOF, EAFs can be turned on and off at will allowing for flexible production applications. Starting in the 1960s and 70s electric arc furnaces focused on steel for low end products such as bars rods, and light section structural steel due to impurities in scrap that cannot be removed. Over time, 100 percent of the long products produced in the United States were by EAF’s.
The early EAF flat rolled mills focused on the low end of the market and then as they became more successful they began to start down the path of more critical applications normally reserved for fully integrated mills. The introduction of less expensive DRI, with its high iron content and none of the residual problems of scrap, is allowing EAF production to focus on light flat rolled products and move up the value chain.
With the potential growth to 20M tons of domestic DRI, SMU instructor John Eckstein predicts that EAF production will grow to more than 70 percent of the domestic market within the next 5 to 10 years. He cites the following reasons:
- Low cost raw material and low cost energy,
- Low residual products for more applications produced by EAF,
- New EAF facilities will be constructed versus blast furnace/BOF’s for cost reasons,
- EAF afford the ability to control production levels better than Blast Furnace/BOF operations,
- Cost to reline an existing blast Furnace may force some integrated mills to shut down aging facilities.
DRI and BOF
When asked about the potential of using DRI in a fully integrated steel mill, metallurgist John Eckstein told SMU, “DRI can be used in a BOF but you have to weigh the cost differences with the grades of scrap that would be used in the BOF. In most cases with a 25% scrap charge, the scrap will be cheaper than DRI. Remember the other 75% is low residual pig iron. Why add DRI with > 95% iron units to produce >95% pig iron? This does not make sense from an operation and/or a cost standpoint.”
DRI and Scrap
DRI, with its higher iron content, is used as a substitute for scrap and can account for at least 35 percent of the mix used to produce steel in an EAF. As demand for DRI increases, scrap prices will likely be pushed downward, providing additional savings for steelmaking. The chart below illustrates the potential cost savings using DRI as compared to pig iron and busheling.
In weak markets, says Nucor CEO John Ferriola, companies make a small but decent return on DRI products with some beneficial cost advantages. In strong markets, DRI has very large competitive advantages when scrap prices and pig iron prices go up. Since Nucor will have locked in the cost of natural gas and iron ore prices are generally less volatile (although this past year saw some dramatic peaks), DRI will provide a long-term supply of low cost, high quality scrap substitute products for their mills.
EAF and DRI Global Production
Global EAF production has risen from 27 percent in 1987 to 45 percent in 2011 (not including China). Global production of DRI, according to Midrex, is estimated to be around 87 million tons. The top five producers of DRI currently are India, Iran, Mexico, Saudi Arabia, and Russia—the common link being abundant natural gas supply. As DRI facilities are built in the U.S., imports of DRI will fall creating potential for U.S. DRI producers to enter the global market.
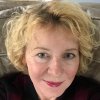
Sandy Williams
Read more from Sandy WilliamsLatest in Steel Products
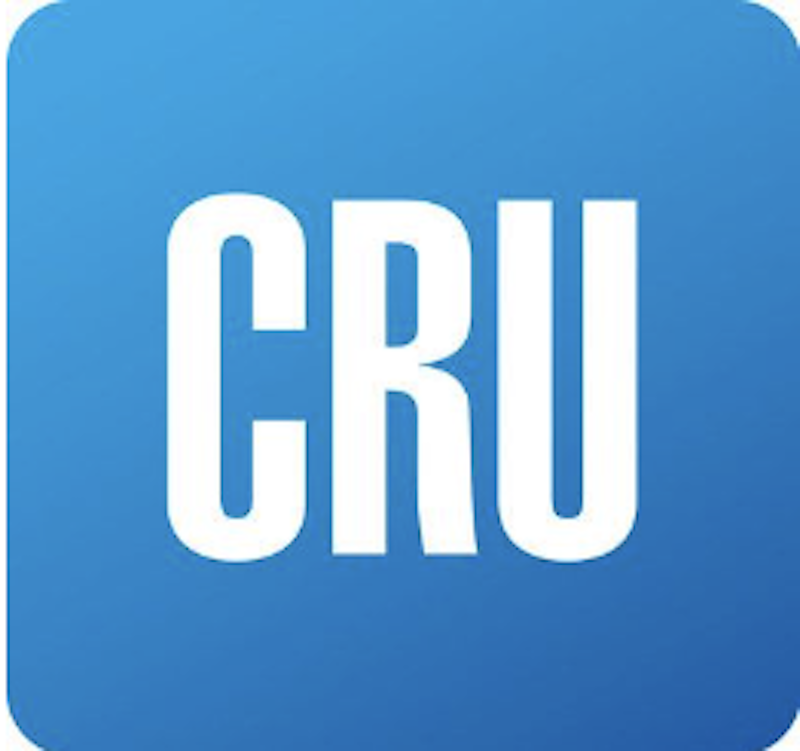
CRU tariff webinar replay now available
CRU’s latest webinar replay on how Trump’s tariffs affect the global steel market is now available on our website to all members. After logging in at steelmarketupdate.com, visit the community tab and look under the “previous webinars” section of the dropdown menu. You’ll find not only this special CRU webinar but also all past Community […]
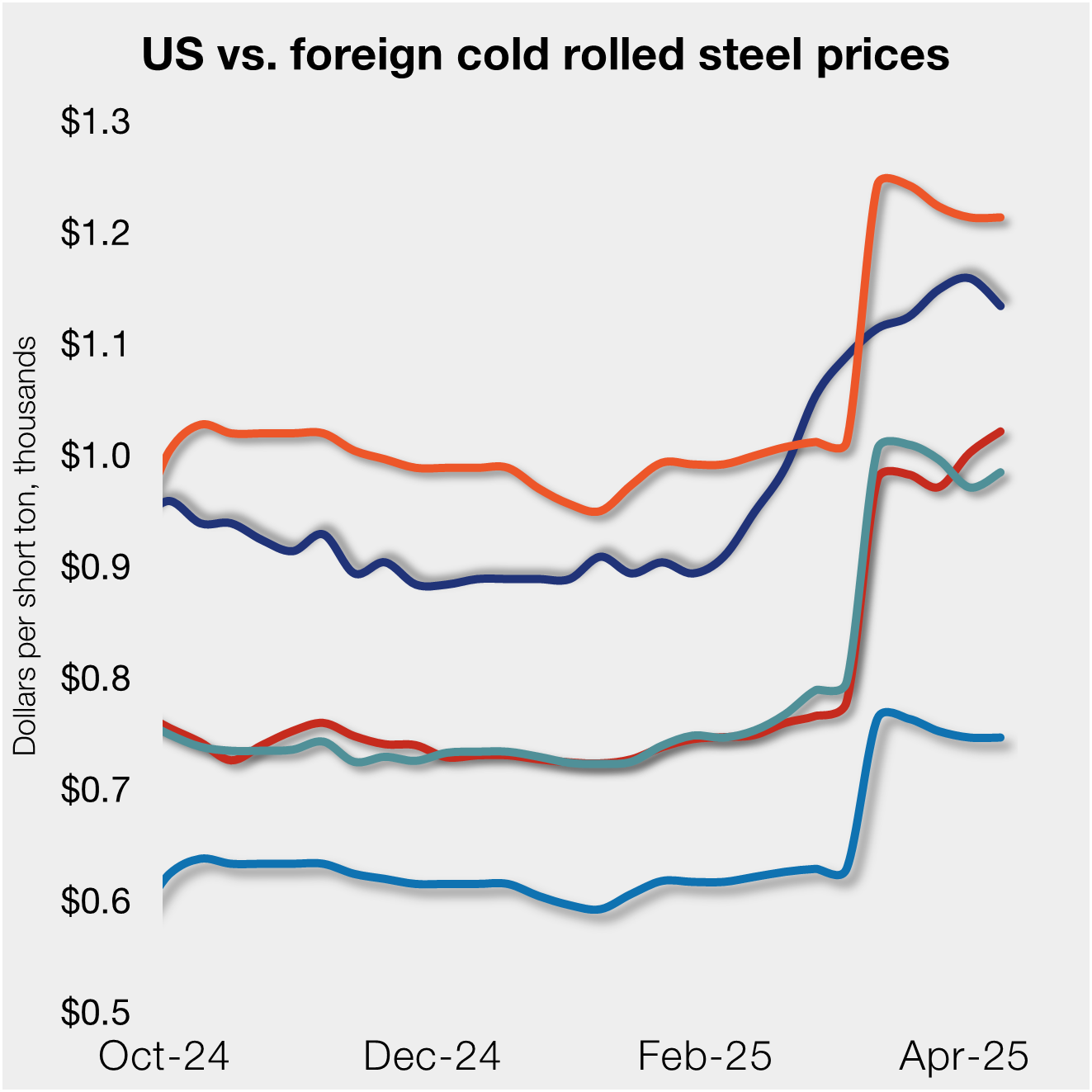
US, offshore CRC prices diverge
US cold-rolled (CR) coil prices declined this week, slipping for the first time since early February. Most offshore markets deviated, moving higher this week.
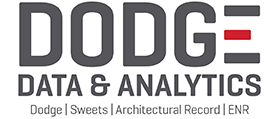
Construction growth slowed in March on tariff woes: Dodge
The decline comes after reaching a record high in January to kickstart the year.
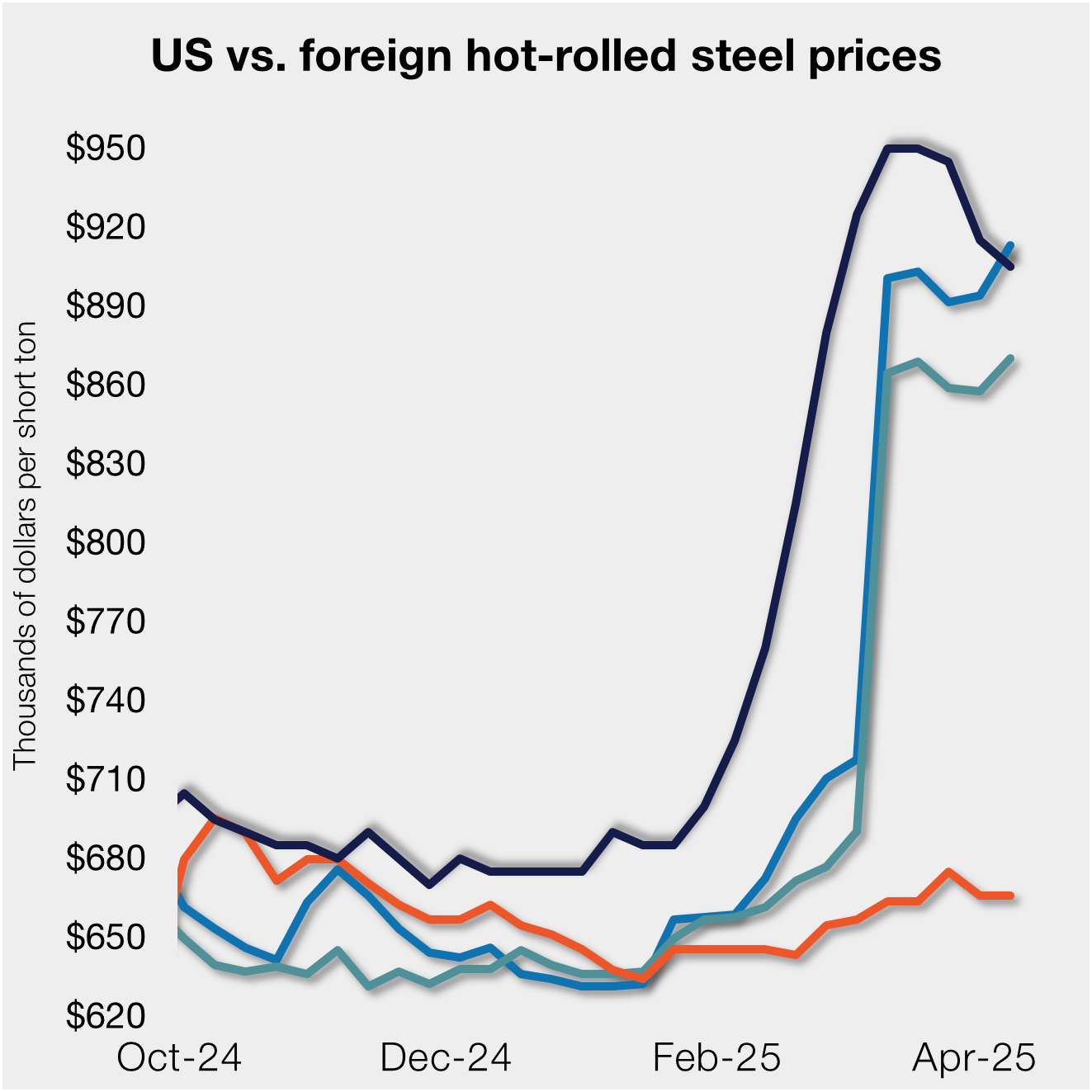
Return of S232 zapped gap between US and EU HR prices, Asian HR remains cheaper
Domestic hot-rolled (HR) coil prices declined this week for a third straight week. Most offshore markets bucked the trend and gained ground. Uncertainty in the US market around tariffs, especially after “Liberation Day,” caused US prices to slip as buyers moved to the sidelines. It’s unclear to date whether the 90-day pause on the more […]
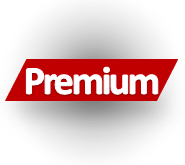
SMU Steel Demand Index momentum slows further
SMU’s Steel Demand Index growth eased again, according to early April indicators. The slowdown comes after the index reached a four-year high in late February.