Final Thoughts
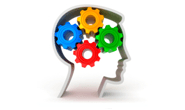
Final Thoughts
Written by Michael Cowden
September 24, 2021
A lot has been written about how a severe shortage of prime scrap could be the lasting result of the widespread shift to electric arc furnace (EAF) steelmaking.
I’d like to take a minute to point out that tri-state area around Pittsburgh, which Nucor is considering for its $2.7 billion, three-million-tpy EAF sheet mill mill, might be an exception to that rule. (We don’t know where U.S. Steel will build its $3 billion, three-million-tpy EAF sheet mill. But we do know that politicians in western Pa. are lobbying for it.)
A Global Scrap Shortage
Cleveland-Cliffs Inc. Chairman, President and CEO Lourenco Goncalves has said that prime scrap is a “precious metal” and that his company would be getting into scrap “very soon.” I don’t know who Cliffs might be eyeing – but we can think of an alphabet soup of scrap companies that could be potential acquisition targets.
And of course it’s not just U.S. Steel and Nucor that are building new EAF sheet mills. Steelmakers in Canada and in Europe have announced plans to switch from integrated steelmaking to the EAF route in order to meet climate goals. And that means it will be harder for U.S. mills to source scrap from north of the border as well as from overseas.
As CRU Senior Analyst Ryan McKinley has noted, EAF capacity growth globally is expected to dwarf that in North America. Approximately 17.6 million short tons of EAF capacity are being added here. That figure is approximately 110 million tons globally – something that is expected to tighten world scrap supplies and to make scrap procurement more difficult.
The Ohio Valley Exception
Why might the Ohio River Valley – so western Pa., northeast Ohio and the West Virginia panhandle – be an exception to the global rule? In a nutshell, the world is adding capacity. The tri-state area has been reducing it for decades.
Consider all the mills in the Ohio Valley alone that have closed in recent years. It’s a little like what we’ve observed about analysis surrounding new sheet capacity. A lot gets written about the capacity that’s coming online. But too often lost, or at least overlooked, in that discussion is that a lot of older capacity – both integrated and EAF – has been closed.
Below are just a few examples:
The former WCI Steel in Warren, Ohio, is permanently closed. The mill, previously owned by Russian steelmaker Severstal and by Ira Rennert’s RG Steel, had capacity of approximately 1.2 million tons per year. Its last blast furnace was torn down in 2017, according to the Warren Tribune Chronicle.
Cleveland-Cliffs’ mill in Weirton, W.Va., is now a finishing operation. That wasn’t always the case. The mill, previously owned by ArcelorMittal, saw its blast furnace idled in 2005, and its basic oxygen plant (BOP) was torn down in March 2019 by the Frontier Group of Companies, per the Steubenville Herald-Star.
It wasn’t just integrated mills that closed. LTV Corp.’s Aliquippa Works – along the Ohio River outside of Pittsburgh – added an electric furnace in the 1970s. That didn’t save it from the broader steel industry collapse the region saw a decade later. The mill – save for tinplate and light structural operations – had mostly closed by 1985, according to And the Wolf Finally Came, a history of the Pittsburgh-area steel industry.
And let’s keep in mind, folks, that just because a mill is an EAF does not mean that it’s new. The EAF currently operated by JSW Steel USA at its mill in Mingo Junction, Ohio, melted its first heat in 2004, per the Youngstown Business Journal, under Wheeling-Pittsburgh Steel Corp. – a prior owner (along with Esmark and Severstal).
I’ll let you run the numbers as to what that means for scrap supplies in the tri-state area. I’d just like to point out that Nucor and the David J. Joseph Co. (DJJ) know what they’re doing. And I’m guessing they’ve already scouted the Ohio Valley and liked what they saw.
You might object. You might note that blast furnaces, like the former WCI’s, don’t typically use much prime scrap. I’m not an expert on the subject. And I’m not going to say that Nucor can work miracles.
I’d just note that Nucor executives have said that the Charlotte, N.C.-based steelmaker could use more shredded scrap in its EAF sheet mills in the future thanks to newer technologies that can remove impurities such as copper – which can make steel brittle – from shred. I’d also point out that Nucor’s direct-reduced iron (DRI) plant in Convent, La., is situated along the Mississippi River and so is perfectly capable of sending material upriver to the Ohio Valley.
Speaking of the Ohio River, let’s remember that Nucor is not the first to suggest a new EAF sheet mill along its banks. Steel Dynamics Inc. (SDI) co-founder Keith Busse – also the company’s former president and CEO – used to talk about building “black beauty,” a proposed EAF sheet mill, along the Ohio. I never did figure out where exactly it might have been located. But maybe one of our readers knows?
Steel 101
If all this jargon is confusing you, I’d suggest you sign up for SMU’s next Steel 101: Introduction to Steel Making & Market Fundamentals Workshop, which will be held virtually on Oct. 5-6. In addition to the classroom portion with SMU’s expert instructors, participants will get a virtual guided tour of a steel mill. You can learn more about next month’s Steel 101 workshop by clicking here.
By Michael Cowden, Michael@SteelMarketUpdate.com

Michael Cowden
Read more from Michael CowdenLatest in Final Thoughts
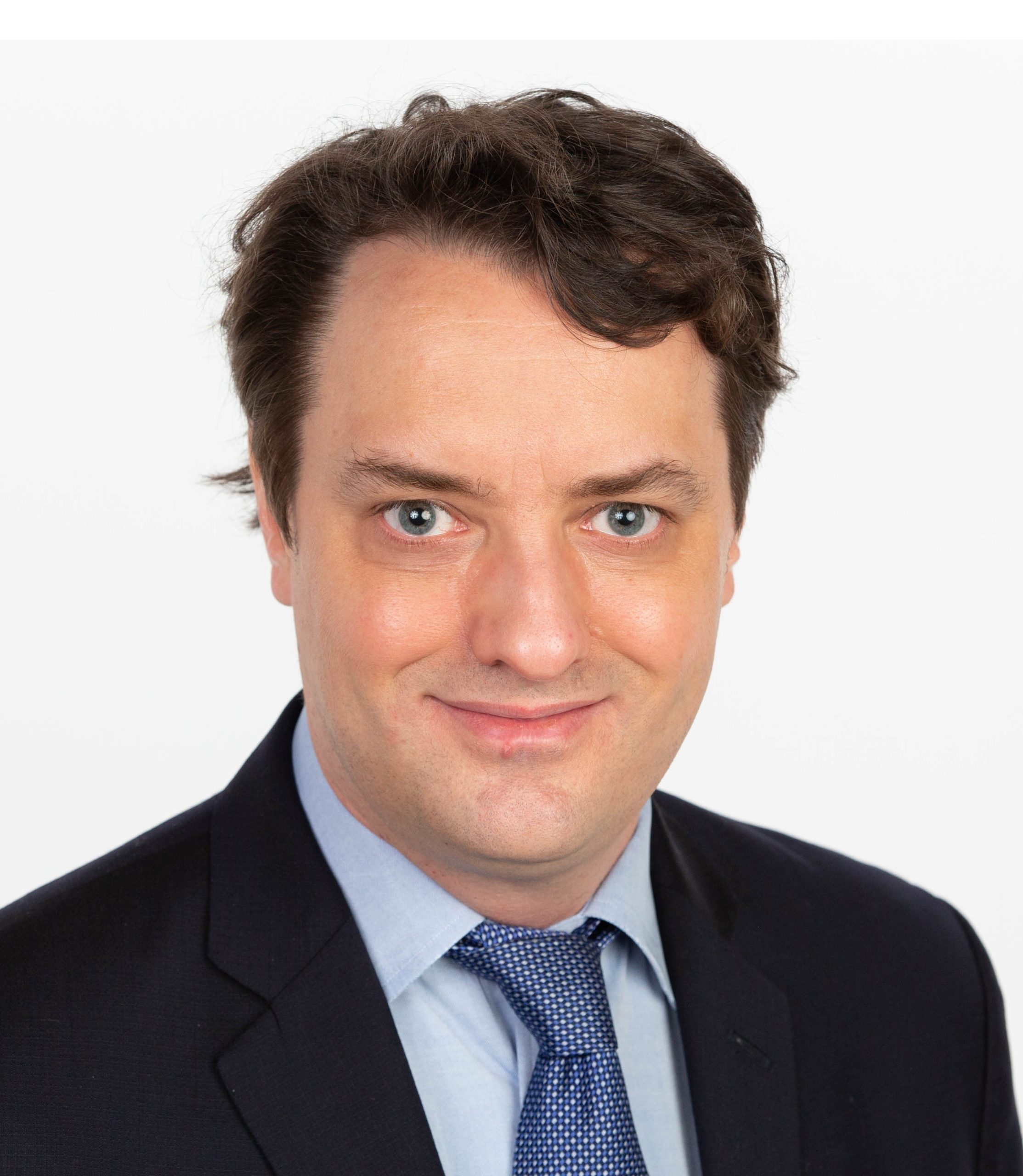
Final Thoughts
Despite some scary headlines lately (especially about Trump potentially firing Fed Chair Jerome Powell) this is not October 2008 (financial crisis) or March 2020 (onset of the pandemic). But it sure seems like we’ve taken a relatively strong economy and poured a thick sauce of uncertainty over it.
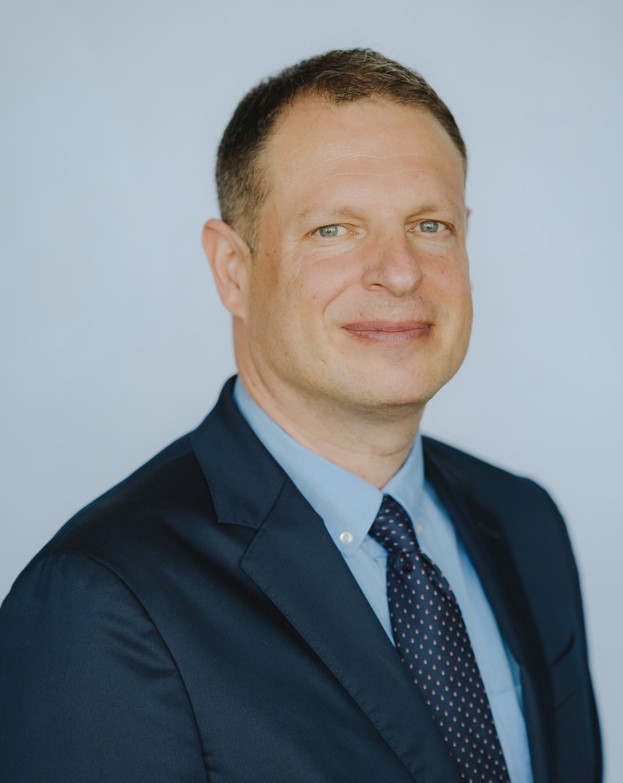
Final Thoughts
I put some of our survey data through ChatGpt, with interesting results.
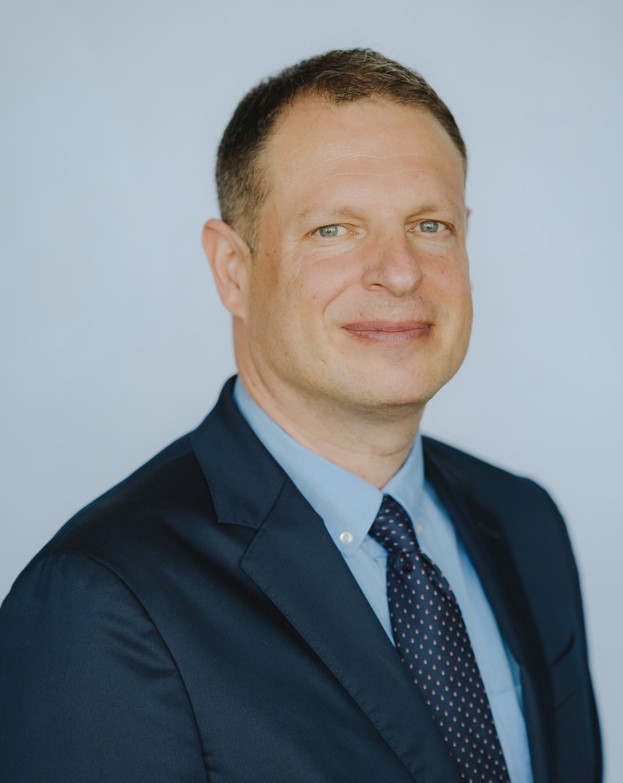
Final Thoughts
Nearly 50% of respondents to our latest survey thought hot-rolled coil prices have already peaked. And where will those prices be two months from now? Responses were decidedly split on that question.
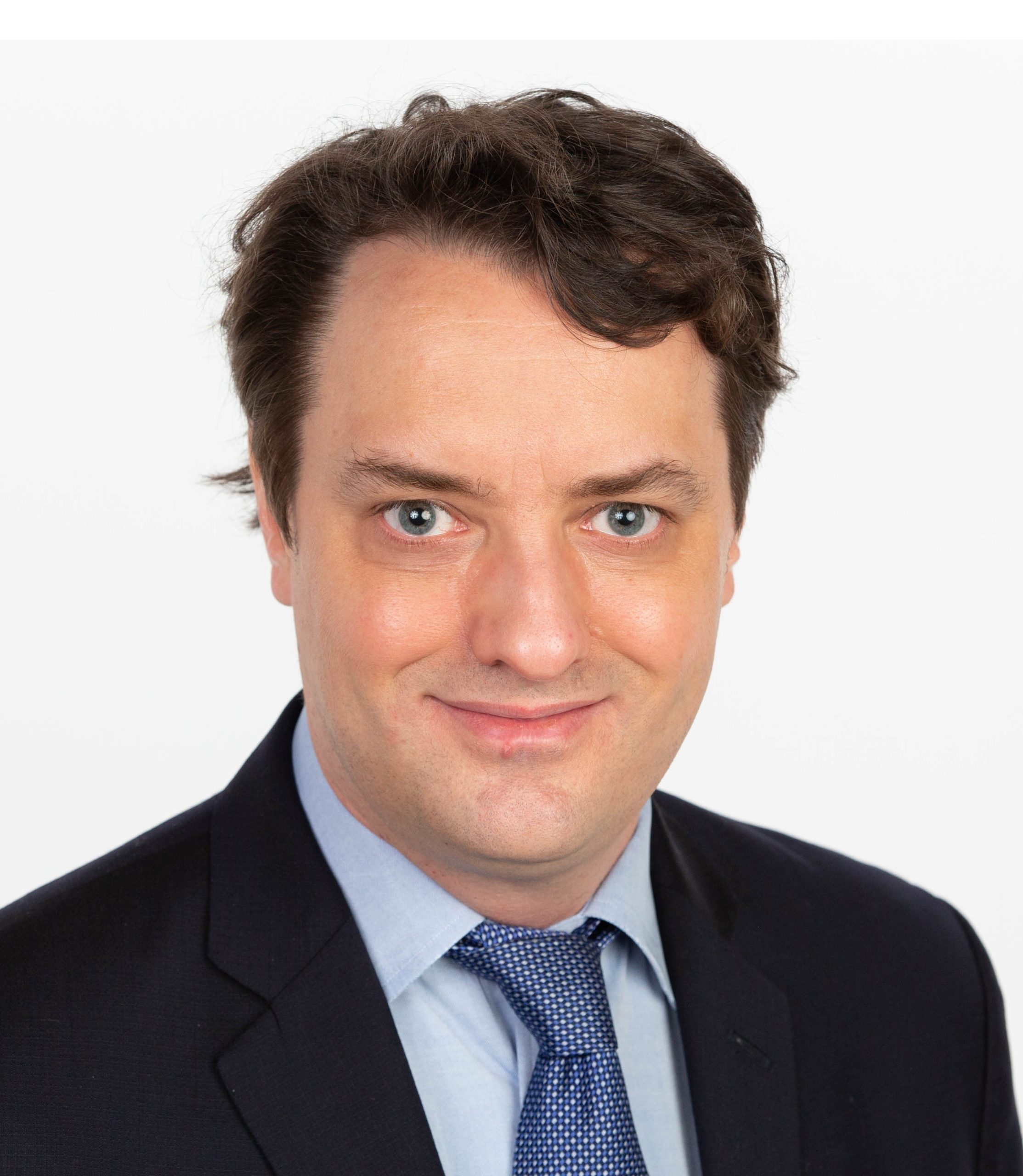
Final Thoughts
A modest week-to-week change in HR price understates a huge swing in expectations.
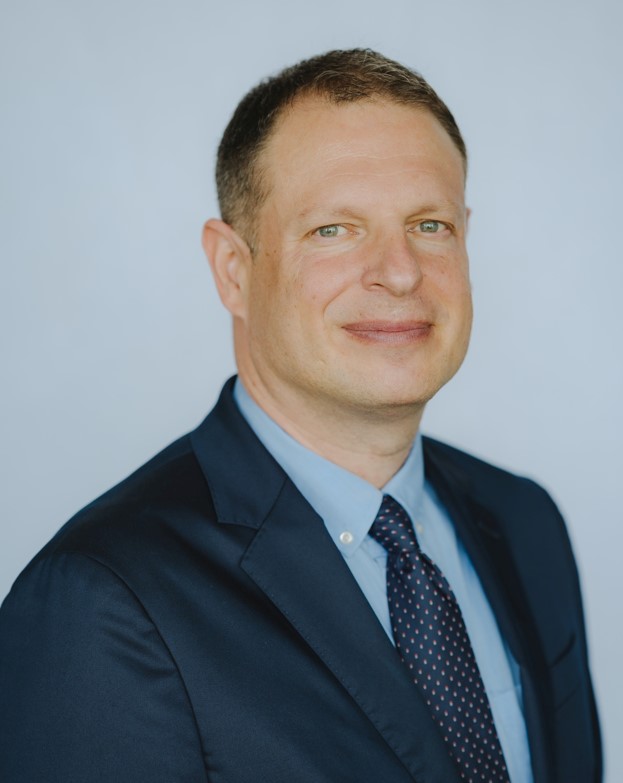
Final Thoughts
What happens when ChatGPT meets SMU's Market Chatter? No, this is not an idea for the latest Hollywood blockbuster. Then again, with what Hollywood is putting out these days, Chatter Meets Chat might just turn out to be a hit. Rather, it’s that old idea of putting theory into practice. Recently, I conducted an interview with Doug Schrock, managing principal of AI at public accounting and consulting firm Crowe. He gave some tips on how to implement AI into your business.