Steel Mills
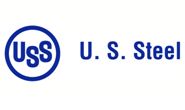
USS Slovakia Mill Must Adopt EAFs to Survive Decarbonizing World: Minister
Written by Michael Cowden
May 21, 2021
U.S. Steel’s mill in Košice, Slovakia, must swap out its blast furnaces for electric-arc furnaces (EAFs) to survive in a decarbonizing world, a government official said.
The problem: Doing so doesn’t come cheap. The change would cost approximately €1.5 billion ($1.8 billion), Slovakian Finance Minister Igor Matovič said per reports in local media.
“If we want to secure the future of the Košice plant, there is no other way than decarbonisation,” Matovič said following a trip to Pittsburgh earlier this month.
Accounts of Matovič’s visit to the steel city, where U.S. Steel is based, were reported on by the English-language Slovak Spectator as well as The News Agency of the Slovak Republic, also known as TASR.
U.S. Steel Košice has three blast furnaces – the No. 1, No. 2 and No. 3 – with combined annual capacity of five million tons per year. And all three furnaces are operating, according to data provided to SMU by U.S. Steel.
The steelmaking complex there – which makes a full suite of flat-rolled products, including electrical steels and spiral-welded pipe – employs nearly 11,000 people, according to its website.
Because U.S. Steel Košice is a “crucial” employer in eastern Slovakia, it should receive aid from the Slovakian government to pay for the shift from integrated to EAF steelmaking, Matovič said.
A U.S. Steel spokeswoman confirmed that company officials had met with Matovič and a Slovakian government delegation about reducing carbon missions. She declined to comment on “speculation” about Košice’s blast furnaces potentially being replaced with EAFs.
“U.S. Steel and government officials are exploring practical ways to decarbonize our operations in Slovakia,” she said. “We appreciate any opportunity to further explore partnering with the government to advance solutions that help us advance our 2050 net neutral carbon goal.”
U.S. Steel has said it wants to reduce greenhouse gas emissions across the company by 20% by 2030 and to be carbon neutral by 2050.
That goal was one of the reaon’s cited for shelving a more than $1-billion project to add “endless” casting and rolling equipment to U.S. Steel’s Mon Valley Works in western Pennsylvania.
“The project we had planned in 2019 would have decreased our carbon footprint, but we must now move farther and faster. Just as steel transformed the world, the world is now transforming steel,” the company said in an open letter.
Other integrated steelmakers in Europe – Swedish steelmaker SSAB, for example – already have plans to replace their blast furnaces with EAFs. The goal: to reduce carbon emissions by moving away from integrated steelmaking, and its reliance on the carbon-intensive coking process, and toward EAF steel production instead.
The backdrop for such decisions: The steel industry accounts for 8% of total global CO2 emissions. And most developed countries have announced or begun implementing plans to significantly reduce carbon emissions.
European mills are toward the middle of a “carbon curve” developed by SMU parent company CRU. They have made great strides in reducing carbon emissions in the context of a continental industry characterized mostly by integrated steelmakers. But a step-change is needed if they are to meet the EU’s increasingly stringent carbon standards.
By Michael Cowden, Michael@SteelMarketUpdate.com

Michael Cowden
Read more from Michael CowdenLatest in Steel Mills
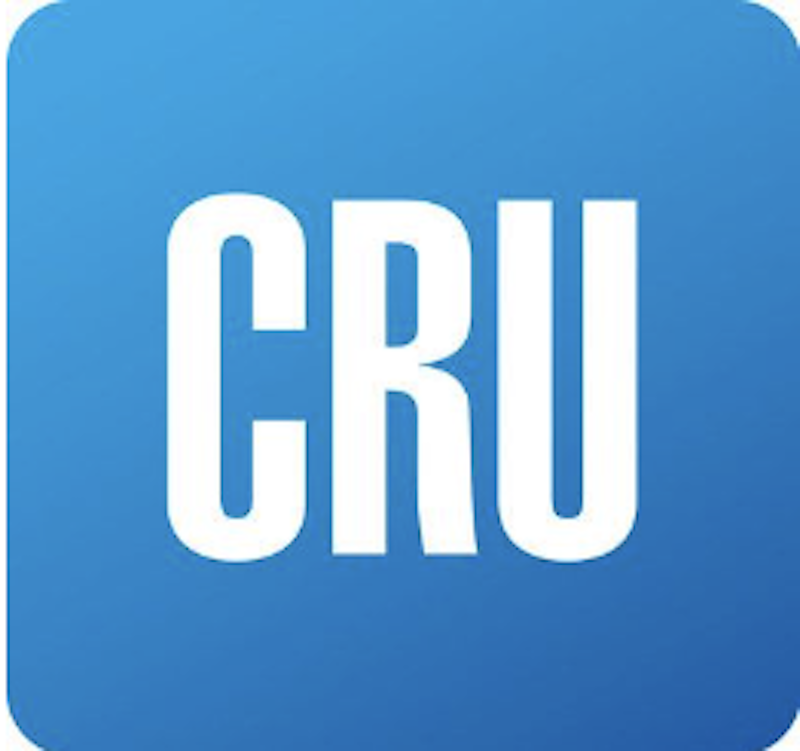
CRU: Tata Steel looks to shed 1,600 jobs in the Netherlands
The company said, “The challenging demand conditions in Europe driven by geopolitical developments, trade and supply chain disruptions and escalating energy costs have affected the operating costs and financial performance."

Reports: Federal funding for Cliffs’ project could be slashed
Elon Musk's DOGE is determining which Department of Energy grants to advance and which ones to terminate, according to several media outlets
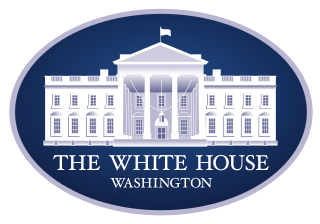
Trump still against selling USS to Japanese firm: Report
Despite ordering a new review of Nippon Steel’s bid for U.S. Steel, President Trump said he is still against selling USS to a Japanese company, according to media reports.
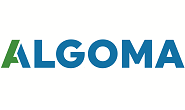
Algoma looks to sell more steel in Canada in wake of Trump’s tariffs
The Canadian steelmaker said its absorbing higher tariffs as it moves forward.
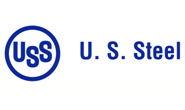
Ancora abandons plan to take over leadership of USS
Investment firm Ancora Holdings Group has halted its play for U.S. Steel's board, citing Nippon Steel’s proposed bid for USS “gaining momentum.”