Steel Markets
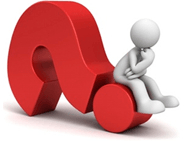
What Does the Trend Toward Electric Vehicles Mean for Steel?
Written by Tim Triplett
April 9, 2021
Given the heightened urgency to reduce carbon emissions and address climate change, nearly all the world’s automakers plan to replace at least some of the internal combustion cars and trucks in their lineups with fully electric vehicles (EVs). GM, notably, has pledged to introduce 30 new EVs by 2025 and to produce nothing but EVs by 2035. The Biden administration’s infrastructure spending plan unveiled April 1 includes $174 billion in incentives for electrification of the transportation sector, including funding for 500,000 vehicle charging stations. By some estimates, EV sales could approach 27 million worldwide by 2030 from less than 4 million today, an annual growth rate of more than 20%. So, what does that mean for steel?
Steel industry experts see the trend toward EVs as a positive one for steel consumption. “We are excited. We think there is a strong case to be made for steel in electric vehicles,” said John Catterall, vice president of the automotive program for the American Iron and Steel Institute.
AISI, the trade group representing integrated steel producers, is a supporter of the Steel E-Motive vehicle engineering program . Ride hailing, autonomous, electric vehicle fleets will eventually provide transportation to millions around the world. Steel E-Motive’s objective is to demonstrate that Advanced High-Strength Steel (AHSS) products and technologies can solve their unique architectural challenges, delivering better strength, safety, durability, affordability, total cost of ownership and environmental sustainability than competing materials. Final results of the study are due in December 2022.
Catterall pointed to several areas where steel offers distinct advantages in the design of electric cars and trucks. Electrical steel used in the motors is an obvious one. Another is the battery enclosure. The current trend is for vehicles to be equipped with a large, flat battery that occupies a big part of the underbody platform, sometimes called “the skateboard.” These batteries must be protected from any penetrating impact, which could cause a fire. Ultra-high-strength grades such as press-hardened and martensitic steels offer a cost-effective solution. “There is a need for a safety cage around the batteries, and high-strength steel is obviously very good for that,” he said.
(Image courtesy Steel E-Motive and WorldAutoSteel)
Automotive designers don’t necessarily bring the same urgency to removing weight from electric vehicles as they do with conventional cars and trucks. EVs don’t have internal combustion engines that produce harmful tailpipe emissions and they use the mass of the vehicle when braking to recharge the batteries. “Even though you may need more energy to launch a heavier vehicle, you recapture some of that energy when you apply the brakes. EVs are a little less sensitive to the overall mass,” Catterall said.
Removing the gas-powered engine and replacing it with electric motors and a battery pack is far from an even swap. Batteries are very heavy and require additional electronics and systems to keep them cool. “There is still quite a mass penalty, around 500-600 pounds, to do an electric vehicle. They are hoping to get to a point where it is not, but that’s where we are today,” he said.
Early on when the battery technology was not as good, a small, lightweight vehicle was necessary to achieve an acceptable minimum range. With today’s very efficient lithium ion batteries, electric-powered cars and even full-sized trucks can travel 300-500 miles per charge.
“There is still some pressure to keep the mass of the vehicle down for efficiency of range, but as far as paying a premium to get that mass down, that equation is changing,” Catterall said. Such math may favor steel over more costly but lighter materials such as aluminum and composites. “Putting a few extra battery cells on the vehicle may be as cost-effective as doing a light-weighting job,” he noted.
Aluminum has made inroads into the automotive materials mix in the past few decades in particular for hang-on closures such as vehicle doors, hoods and roof panels, something Catterall described as “parasitic mass” when it comes to the overall performance of the vehicle. He sees a potential opportunity for steel to win back some of those exposed automotive applications as the OEMs look for less expensive tradeoffs to help pay for the high-tech electronics and sensors in the next generation of electric and autonomous vehicles.
“Other than Ford’s F-150 trucks, we have not seen a big movement of alternative materials into the main body structures. The predominant material is still steel. Even the Tesla 3 Series has reintroduced steel back in, which is clearly a cost play,” he said.
Steelmakers continue to pour millions into R&D to create more formable, high-strength steels to protect their share of the lucrative automotive market from competing materials, such as magnesium and carbon-reinforced plastics, as well as aluminum. “We are giving the demanding automotive engineer more reasons to select steel,” Catterall said.
(Image courtesy Steel E-Motive and WorldAutoSteel)
One reason, now higher on the list, is “sustainability.” The steel industry points proudly to the environmental benefits of electric-arc furnaces, which recycle ferrous scrap. Integrated steel producers are also working to reduce the carbon emissions from their blast furnace process, which uses coking coal and iron ore. Their ultimate goal, to produce “clean steel” that is carbon neutral, is likely many years away. But they still claim the life-cycle high ground versus aluminum production that requires enormous amounts of electricity, which has a significant environmental impact of its own.
“We now have automotive engineers talking about sustainability as a criterion in the selection of materials. We didn’t hear that until recently,” Catterall said. “The automakers want to get to a zero-carbon footprint, and they are pushing that all the way back down the supply chain.”
As EVs displace the millions of conventional vehicles on the road today, will that be a net positive for steel demand? “We’re still studying that question, but fundamentally there should be a very similar use of steel in an electric vehicle versus a conventional vehicle,” Catterall said. “The auto manufacturers will try to use the most efficient mix of materials they can, so we don’t see anything that will change the equation significantly.”
Editor’s note: The aluminum industry paints a very different picture of the future for automotive materials. Steel Market Update will give the aluminum industry equal time to make its case in an upcoming issue.
By Tim Triplett, Tim@SteelMarketUpdate.com
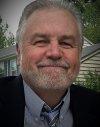
Tim Triplett
Read more from Tim TriplettLatest in Steel Markets
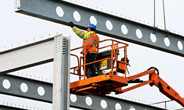
Steady architecture billings signal improving conditions
The November ABI decreased month over month but was still the third-highest reading of the past two years.
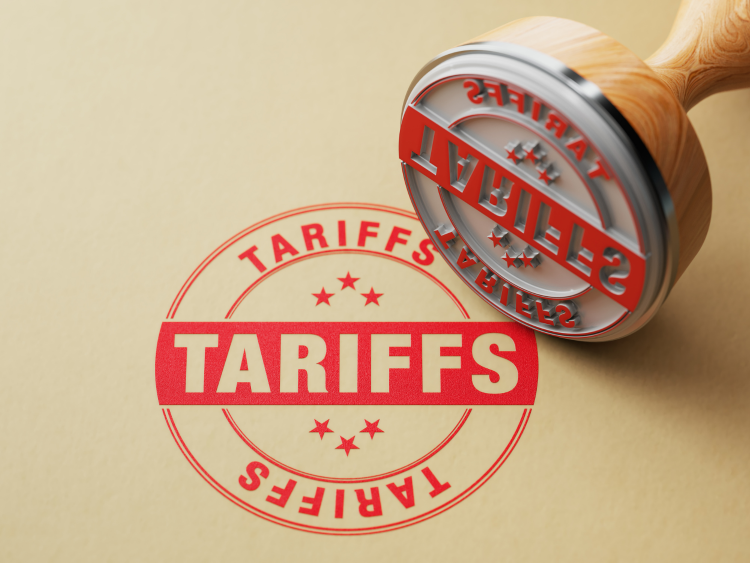
Fitch warns more tariffs will pressure global commodity markets
“New commodity-specific tariffs, mainly on steel and aluminum products, could widen price differentials and divert trade flows,” the credit agency forewarned.
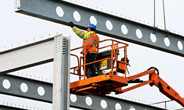
Slowing data center, warehouse planning drives decline in Dodge index
The Dodge Momentum Index (DMI) slid further in November as planning for data centers and warehouses continued to decline.
Latin America’s steel industry grapples with declining demand, rising imports
With climbing imports and falling consumption, the Latin American steel industry has had a challenging 2024, according to an Alacero report.
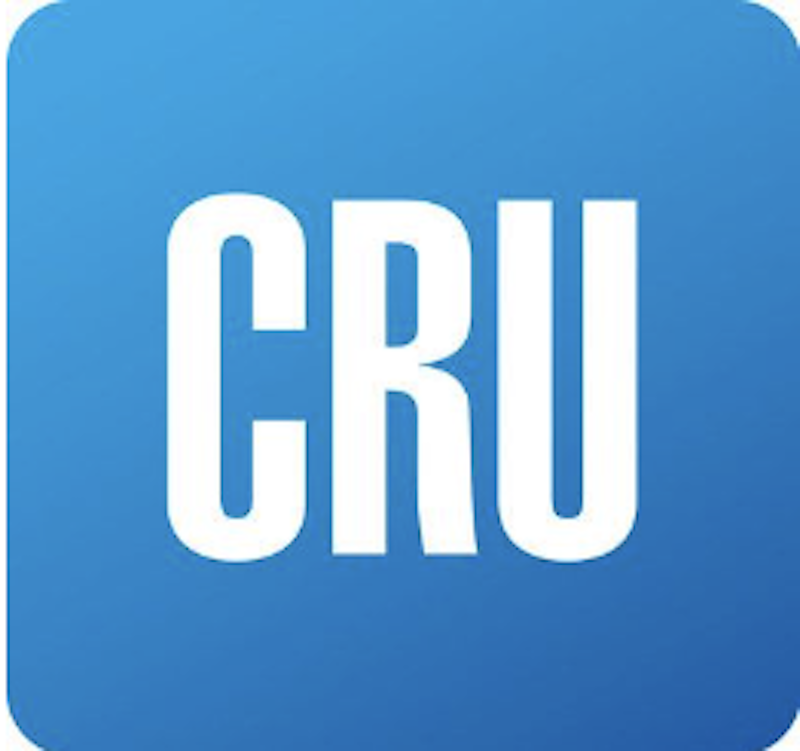
CRU: Trump tariffs could stimulate steel demand
Now that the dust has settled from the US election, as have the immediate reactions in the equity, bond, and commodity markets, this is a prime opportunity to look at how a second Trump presidency might affect the US steel market.