Steel Products
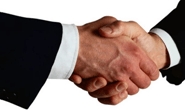
A Marriage Made of Steel: Big River Steel and U.S. Steel
Written by Sandy Williams
August 28, 2020
The future of U.S. Steel and Big River Steel as one entity continues to excite CEOs from both companies. Speaking during the SMU Virtual Steel Summit this past week, U.S. Steel CEO David Burritt could barely contain his enthusiasm regarding the opportunities the marriage of the two companies will provide the iconic steel producer.
Burritt called Big River Steel an “incredible asset” that U.S. Steel is thrilled to be “engaged to” even though the marriage probably won’t take place for more than three years.
The entrepreneurial mindset of Big River Steel, their technological capabilities and nimble operations will bring the “best of both worlds” to U.S. Steel and allow the company to be profitable even in the trough cycles, said Burritt. He added that U.S. Steel will be sure to take care with Big River’s culture. “We will not stifle them. We will let them run their business and they will run it better,” he said. “When we are ready to go, and we will go, we will amaze and delight everyone.”
David Stickler, CEO of Big River Steel, said the partnership with U.S. Steel will bring BRS deep product know-how, research capabilities and extensive customer contacts, especially in the automotive industry.
“Our cultures are different, I won’t deny that,” said Stickler. “U.S. Steel has 118 years of doing things a certain way, but hats off to them for embracing change.”
The two companies are already working on projects together. U.S. Steel had been paying a company to take their scrap sheet, slabs and pipes and cut them up for reuse in their BOF. Big River is now taking that scrap, processing it more efficiently and melting it in the EAF to produce high-quality steel that U.S. Steel can sell through its system.
Both companies have separate projects in the works that are nearing completion. Big River Steel is targeting Nov. 18 for completion of an expansion that will double its hot rolled coil capacity to just over 2.6 million tons. So far, the project is almost three months ahead of schedule and 6 percent under budget. Stickler says that commercial quality steel will be produced on the very first day and after a three-day cooling period will be in the market. Based on Big River’s experience in Phase 1 of the Osceola mill, operations should be at or above rated capacity by the fourth or fifth month of production.
Stickler was particularly proud of the design of BRS, with automation from scrap loading through to the galvanizing line, which produces 3,000 tons of steel annually per employee. Following completion of the expansion, that figure will move to over 5,000 tons annually per employee. Competitors, he said, are struggling to get over 900 tons per employee.
Another project in the works for Stickler is “off balance sheet from Big River Steel.” Plans are in the works to build a steel mill at Brownsville, Texas, and work has begun on obtaining environmental permits. With a finally completed power system at Brownsville, incentive packages in the works, a great scrap supply, access to a deep water shipping channel and expected financing from a German bank, the project is getting closer to fruition. Once completed and generating free cash flow, BRS will have an option to acquire it. Said Stickler of the project, “Can I say with 100 percent certainty that we will build it in Brownsville? No, but I can tell you we have 100 percent certainty that we want to.”
At U.S. Steel, the endless casting project at Mon Valley is on hold until it receives permitting. When completed the facility will be able to produce steel as thin as six strands of hair, said Burritt. The EAF at Fairfield is expected to be running by the end of the year and the team has been receiving advice and training from Big River Steel. A continuous galvanizing line at the Protec facility in Ohio will enable customers to utilize a fast stamping process with existing tools and dies and will be commissioned by the end of the fourth quarter.
Can EAFs produce the quality of exposed steel that the automotive market requires? Absolutely, said Stickler. Whenever an integrated steel maker says an EAF can’t do something, they are proven wrong, he said. Stickler added that auto companies are also increasingly looking at the sustainability footprint of their steel supply. Big River is among the top three lowest carbon emitters in the steel world.
“Automakers are loath to buy from those who mine iron ore and coal and produce steel in equipment that was installed 80 some years ago,” said Stickler. When asked by an auto company if Big River could produce the highest quality steels using 100 percent steel scrap, he replied, “Not sure about 100 percent, but with your help we could do 90 percent.”
Both Stickler and Burritt are confident in the futures of their companies and looking forward to one that includes the best of both their strengths.
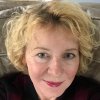
Sandy Williams
Read more from Sandy WilliamsLatest in Steel Products
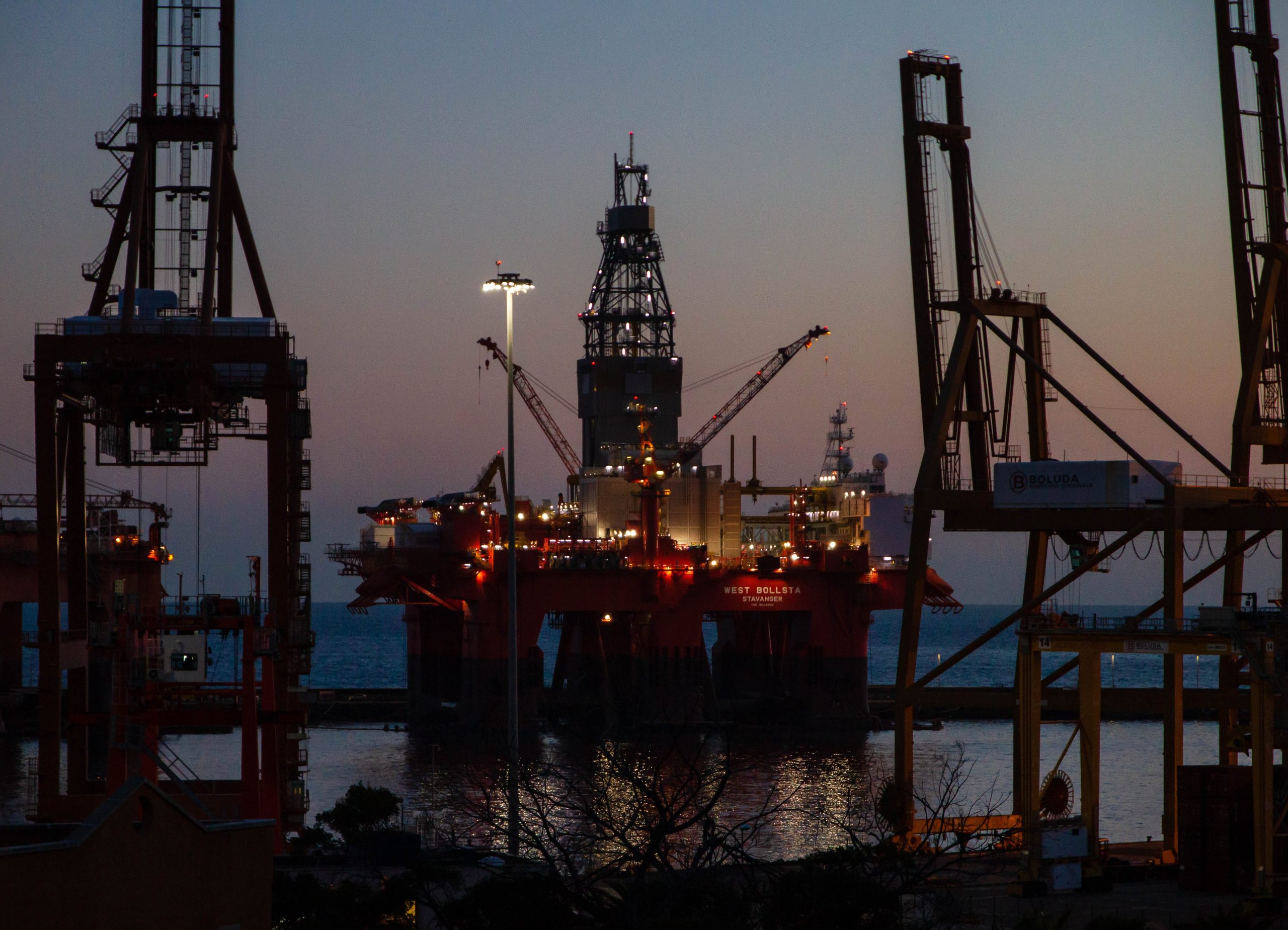
US rig count up, Canada declines
Oil and gas drilling activity was mixed this week, according to Baker Hughes. US rig counts expanded for a second straight week, while Canadian activity continued its seasonal slowdown of eight consecutive weeks.
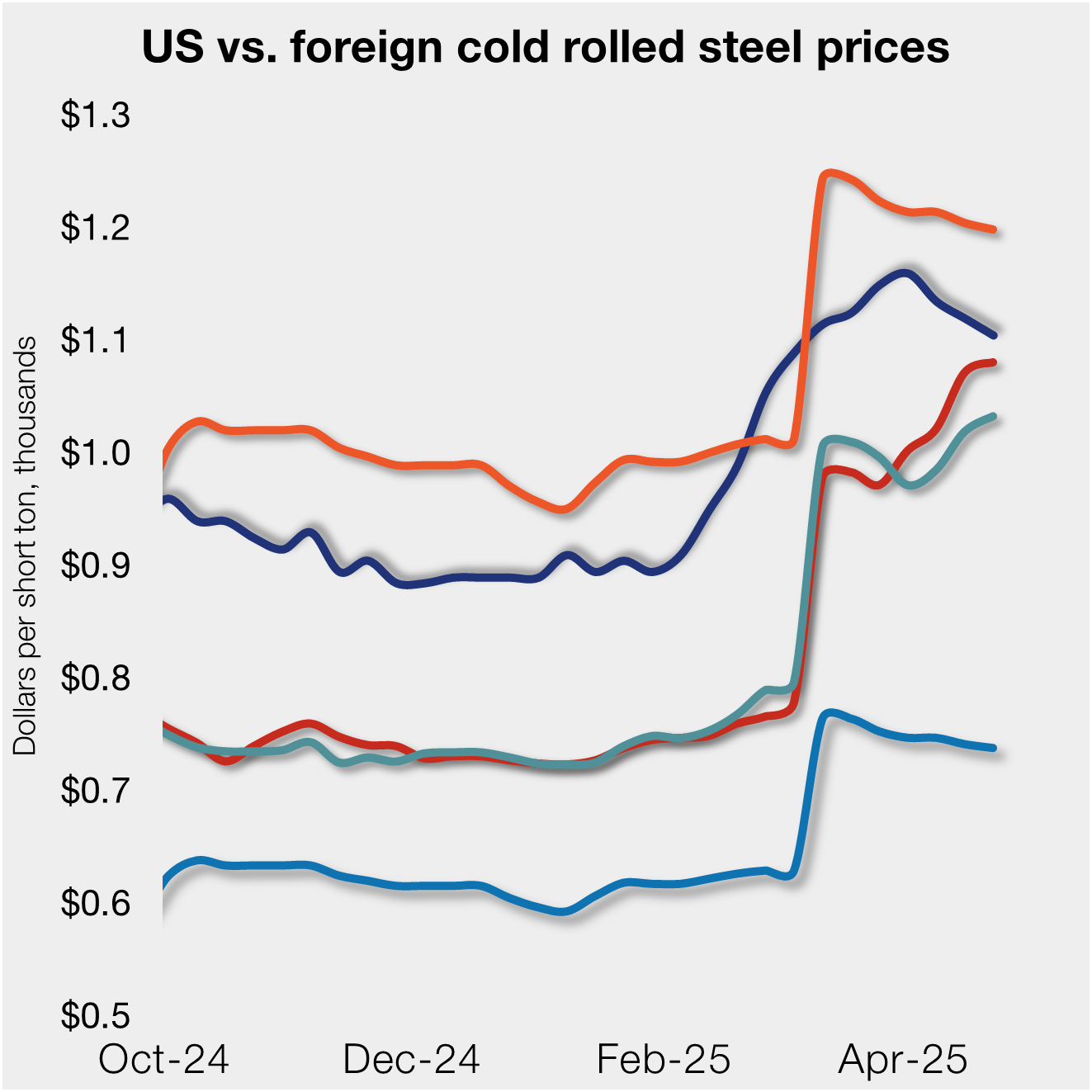
US, offshore CRC prices continue to diverge
US cold-rolled (CR) coil prices declined again this week, slipping for a third straight week. Most offshore markets did the opposite, moving higher this week.
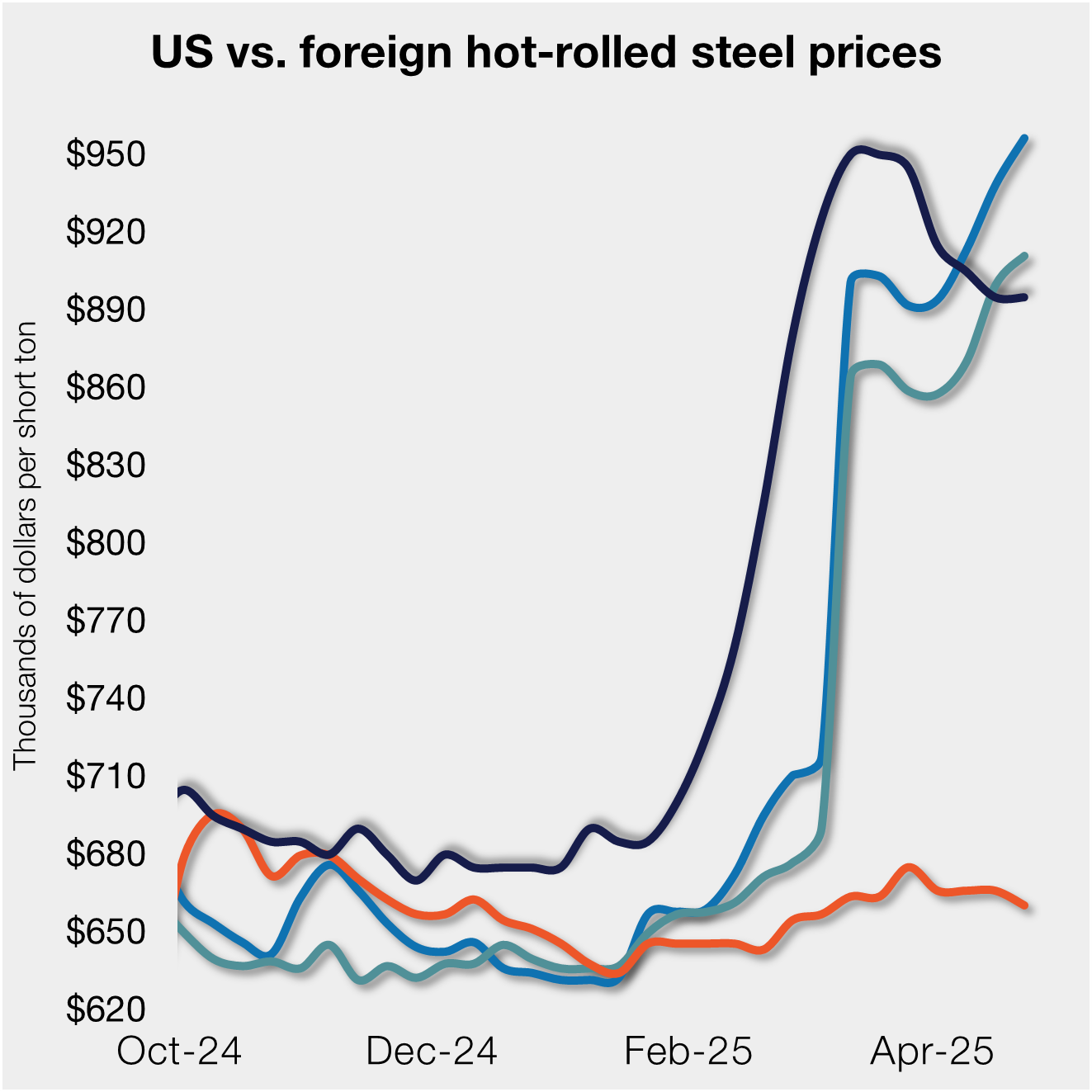
S232 lifts EU HR price over US, Asian HR still well behind
Domestic hot-rolled coil prices were flat this week after dropping for four straight weeks. Most offshore markets bucked the trend and gained ground.
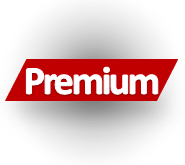
SMU Steel Demand Index dips into contraction
SMU’s Steel Demand Index has moved into contraction, according to late April indicators. The slowdown comes in response to growing tariff uncertainty after the index reached a four-year high in late February.
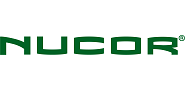
Nucor selects Fives Group for new galv line at CSI
Nucor Corp. has tapped Fives Group as its partner in designing and manufacturing the new continuous galvanizing line being added at its California Steel Industries (CSI) joint venture in Fontana, Calif.