Steel Mills
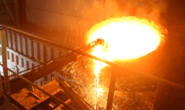
Worldsteel: "No Single Solution to Reducing CO2 Emissions"
Written by David Schollaert
July 28, 2020
Reducing harmful greenhouse gas emissions from the steelmaking process, which remains a very CO2- and energy-intensive activity, calls for a combination of approaches that may vary from nation to nation. “There is no single solution to drastically reducing CO2 emissions from our industry, and we believe that individual countries are best placed to assess and implement policy and technical strategies to suit their particular circumstances,” concluded the World Steel Association (worldsteel) in a new public policy paper.
In the report, worldsteel highlights that steelmakers can reduce GHG emissions by a) improving industry review standards, b) maximizing scrap use, and c) applying new technology to reduce fossil fuel dependency.
On average, every metric ton of steel produced led to 1.85 metric tons of CO2 released into the atmosphere in 2020. A total of 1.86 billion metric tons of steel were produced globally in 2020, resulting in total direct emissions of 2.6 billion metric tons, or 7-9% of all human-caused CO2 emissions, according to the association.
In 2019, worldsteel launched an industry-wide efficiency review process called Step Up. The process promotes leading practices that focus on the key efficiency levers of raw material quality, energy efficiency, process yield and process reliability. If such methodology is adopted, it could reduce direct and indirect emissions by up to 20% at an average ore-based steelmaking site, and by up to 50% at an average scrap-based facility, worldsteel said.
The industry can significantly reduce its carbon footprint by expanding electric arc furnace steelmaking. Future expansion of this scrap-based steel production will depend on the availability of high-grade scrap. Every metric ton of scrap used for steel production avoids the emission of 1.5 metric tons of CO2, and the consumption of 1.4 metric tons of iron ore, 740 kilograms of coal and 120 kilograms of limestone in blast furnace production. Growth of EAF steelmaking should be made easier as more steel from China begins to enter the scrap market in the next decade, worldsteel noted.
Investing in new ways to produce low-carbon steel from iron ore also will help reduce the industry’s carbon footprint. While a blast furnace is the primary way of reducing iron ore, it is nearing the efficiency limits of the reduction process. Therefore other options are necessary, such as: a) using carbon as a reductant while preventing the emission of fossil CO2, b) substituting hydrogen for carbon as a reductant, generating water rather than CO2, or c) using electrical energy through an electrolysis-based process.
There is no single solution to low-carbon steelmaking, the report concludes, and a broad portfolio of technological options, resource availability, and local policy support will be required. Pursuing these process changes will add 10-50% to today’s production costs, estimates the International Energy Agency (IEA), including increased operational costs, capital expenses, and capital losses arising from early retirement of long-lived steelmaking assets.
“What is absolutely clear is that governments and other stakeholders will need to work with the steel industry to overcome the technological and economic challenges and create the market conditions necessary for the steel industry to transition to low-carbon steelmaking effectively,” said worldsteel’s director general, Edwin Basson.
By David Schollaert, David@SteelMarketUpdate.com
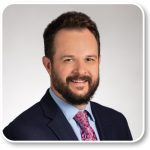
David Schollaert
Read more from David SchollaertLatest in Steel Mills
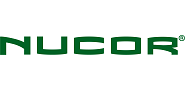
Nucor names Batterbee, Bledsoe to HR roles
Nucor Corp. has promoted Thomas J. Batterbee to the position EVP of human resources and talent and appointed Elizabeth Bledsoe to the newly created position of president of human resources and talent.
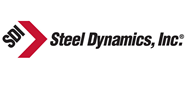
Millett sees tariffs, CORE case benefiting SDI
Steel Dynamics' top exec thinks Trump’s tariff policies, as well as the results from the recent CORE case, will prove advantageous to the Fort Wayne, Ind.-based steelmaker and aluminum company.
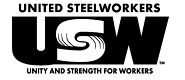
USW digs in on opposition to USS-Nippon deal
“We remain deeply concerned about the national and economic security implications of the subject transaction,” the union stated in the letter dated April 21.
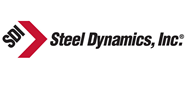
SDI’s Q1 earnings slump on-year, but up sequentially
SDI earnings slip in first quarter year over year, but are up sequentially.
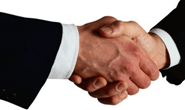
POSCO inks MoU with Hyundai on Louisiana EAF mill
POSCO has signed a Memorandum of Understanding (MoU) with Hyundai Motor Group that includes an equity investment in Hyundai’s previously announced EAF mill set to be built in Louisiana.