Steel Products
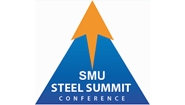
Rail Exec to Detail the “Puts and Takes of Tariffs” at SMU Steel Summit
Written by Tim Triplett
May 20, 2019
Rail transport is a critical link in getting steel to market. With domestic mills cranking out steel at more than 80 percent of their capacity, are the railroads struggling to keep up?
“People assume our business should be booming, but it’s not as straightforward as one would think,” said JR (Jim) Schaaf, Group Vice President for Metals & Construction with Norfolk Southern, which operates the largest steel-handling railroad in North America. Schaaf will offer his company’s view of the market and how tariffs have affected the rail transport of commodities as a speaker on the transportation panel at the Steel Market Update Steel Summit Aug. 26-28 in Atlanta. “Some would assume the tariffs have made things better from a rail transportation perspective. It has had some puts and takes with respect to the benefits of Section 232,” he said.
The Norfolk Southern Railway Company subsidiary operates approximately 19,500 route miles in 22 states and the District of Columbia and serves every major container port in the eastern United States. The company’s new three-year strategic plans is based on an operating model known as precision scheduled railroading, and is built on five principles: serving customers, managing assets, controlling costs, working safely, and developing people. The new strategic plan already is delivering results. The company achieved its all-time best first-quarter performance in 2019 across a range of financial measures, including net income, earnings per share and operating ratio. It also accomplished significant improvements in network fluidity and velocity, increasing average train speed 14 percent and reducing the time that rail cars dwell in terminals by 23 percent.
The changes at Norfolk Southern have enabled the rail line to keep up with the pace of steel production, Schaaf said. “A year or so ago we had some capacity issues, which were more self-inflicted. Since then we have changed our operating practices—more scheduled railroading—which has freed up a lot of capacity just by being more focused on on-time delivery. We have increased the frequency of pickup and delivery with our customers. We continue to focus more on velocity and getting more out of the rail fleets that we have,” he said.
The tariffs on steel imports, notably semi-finished steels, have placed an unusual burden on the supply chain, Schaaf noted. For example, one Norfolk Southern customer, a re-roller with a foreign parent whose tariff exclusion request was denied, must source slabs from other domestic mills to maintain production. “Certain mills have the capacity to supply slabs to other companies, but they can’t tell you from month to month where that capacity will come from,” he explained. “They have to fill their orders first and then offer whatever they have left on the open market. From one month to the next you never know what tonnage is coming from what mill. So, it forces you to deploy more equipment, it elongates transit times, it puts a stress on the logistics chain that was not previously there.”
Norfolk Southern sees both challenge and opportunity in the planned capacity additions announced by several mills. If they all follow through, some 15-20 million tons of new steelmaking capacity will be added to the market in the next five years. That’s a lot of raw materials, steel and scrap to hit the rails. Much of this growth will take place at smaller minimills in remote locations across the country.
“We will clearly have to ramp up to make sure there is equipment available,” Schaaf said. “Long term, I think it will be good for the industry, but there will have to be a lot of communication to make sure we have ample time to plan. If managed correctly, it can be absorbed.”
For more information on SMU’s Steel Summit and to register, click here.
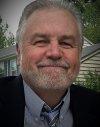
Tim Triplett
Read more from Tim TriplettLatest in Steel Products
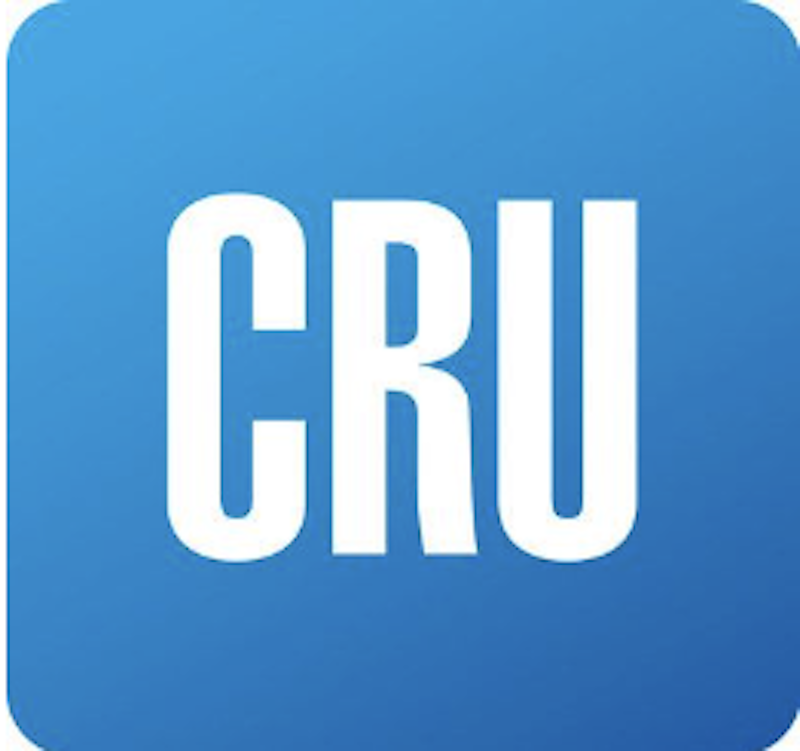
CRU tariff webinar replay now available
CRU’s latest webinar replay on how Trump’s tariffs affect the global steel market is now available on our website to all members. After logging in at steelmarketupdate.com, visit the community tab and look under the “previous webinars” section of the dropdown menu. You’ll find not only this special CRU webinar but also all past Community […]
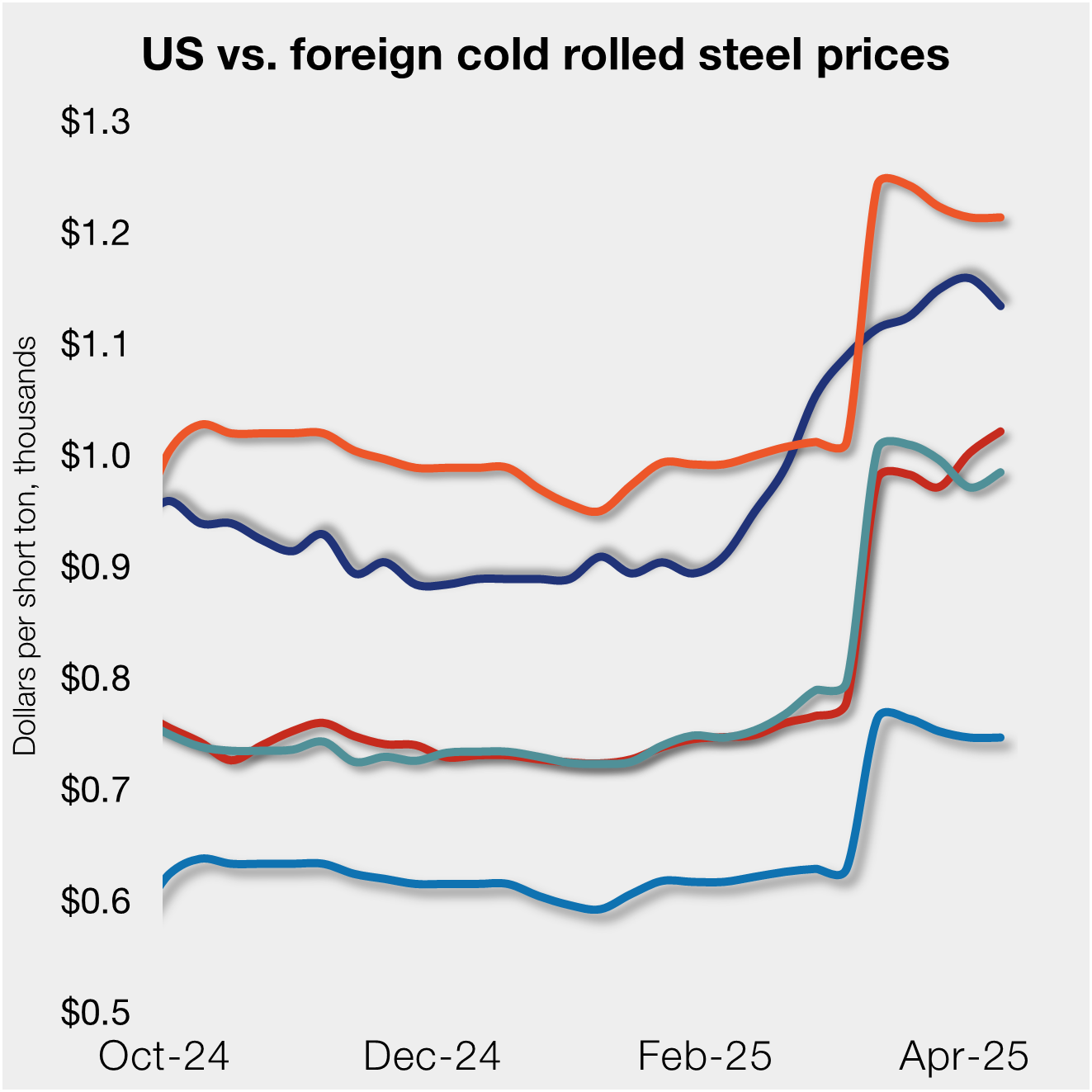
US, offshore CRC prices diverge
US cold-rolled (CR) coil prices declined this week, slipping for the first time since early February. Most offshore markets deviated, moving higher this week.
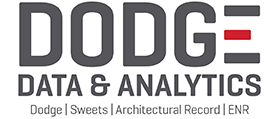
Construction growth slowed in March on tariff woes: Dodge
The decline comes after reaching a record high in January to kickstart the year.
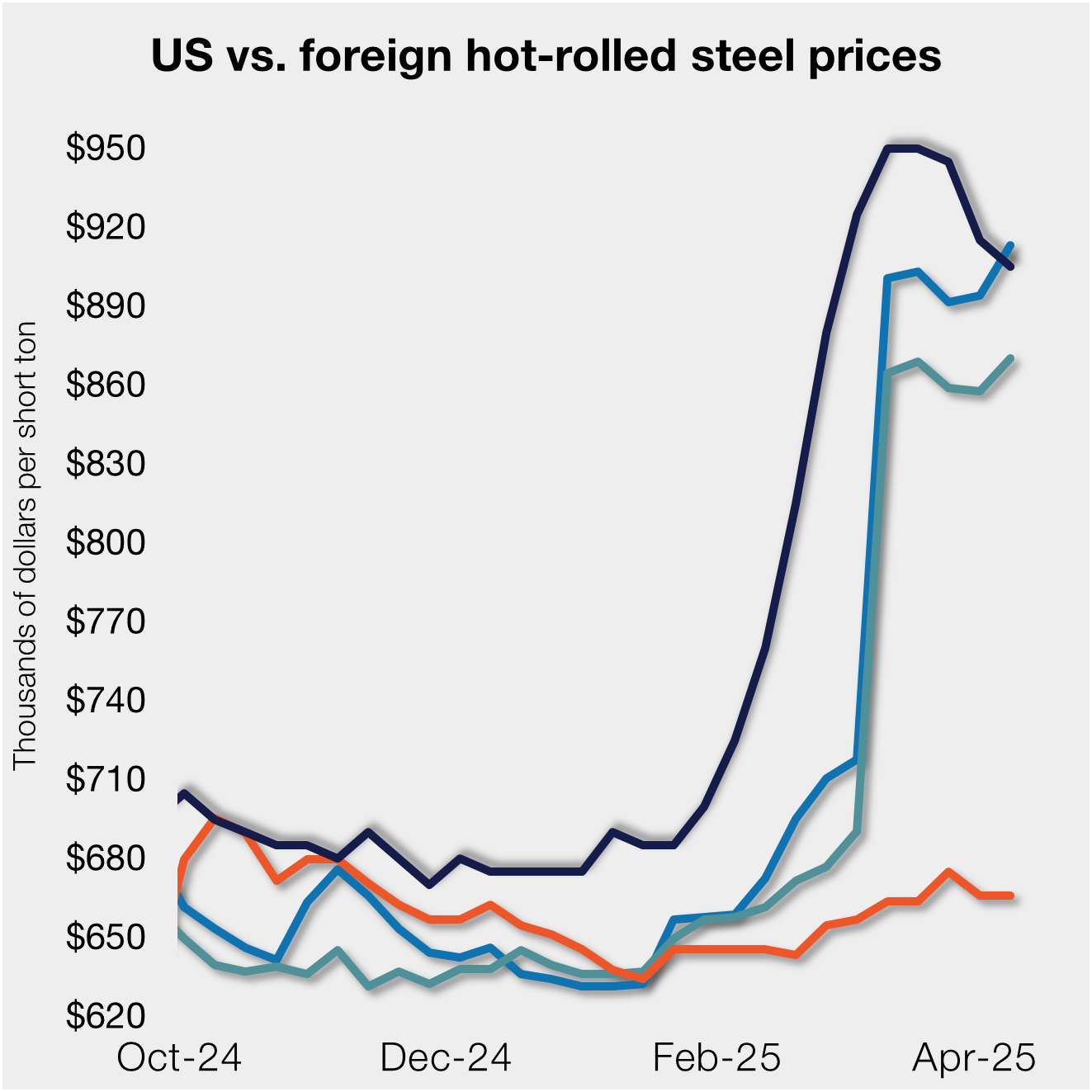
Return of S232 zapped gap between US and EU HR prices, Asian HR remains cheaper
Domestic hot-rolled (HR) coil prices declined this week for a third straight week. Most offshore markets bucked the trend and gained ground. Uncertainty in the US market around tariffs, especially after “Liberation Day,” caused US prices to slip as buyers moved to the sidelines. It’s unclear to date whether the 90-day pause on the more […]
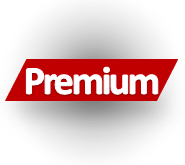
SMU Steel Demand Index momentum slows further
SMU’s Steel Demand Index growth eased again, according to early April indicators. The slowdown comes after the index reached a four-year high in late February.