Environment and Energy
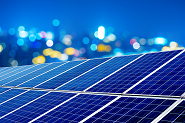
McKay: No Easy Road to a Green Industry
Written by David Schollaert
July 2, 2021
There are many roads to a Paris Accord-aligned carbon emissions target, but few steel-specific pathways, said BHP Billiton Chief Economist Huw McKay during CRU’s Steel Decarbonization Strategies 2021 Virtual Conference last week.
BHP’s top economist said steel emissions have roughly doubled over the past three decades due to rising demand and production despite major efficiency gains, as he offered sustainable decarbonization strategies for the steelmaking supply chain.
Presently, the average global emission is 1.7 tons of CO2 per ton of steel produced, down from 2.2 in 1990. The U.S., on average, has the lowest carbon intensity at 1.0 ton of CO2 per ton of steel, while India has the highest at 2.4 tons. China—the world’s largest producer of steel—has the second highest emissions at 1.8 tons of CO2 per ton of steel.
“Steel is a major emitter of greenhouse gas, but steel is also the backbone of the modern-built environment,” said McKay.
U.S. steelmakers, which favor electric arc furnace production, are the leaders in terms of low carbon intensity and greenhouse gas emissions due to their use of scrap, high-quality pellets and injection of natural gas. Key steelmaking regions in other parts of the world are at different starting points from a decarbonization perspective due to their dependence on blast furnaces and in some cases older assets. “They are all at vastly different commercial incentive stages, even before you begin to consider other factors such as policy support,” McKay said.
He noted that the steel industry has made significant strides over the last 30 years when it comes to carbon intensity. “Since 1990, global steel production has almost tripled, but emissions did not quite double. Production is up, and intensity has improved.”
Factors contributing to the improved carbon intensity include the closure of obsolete mills in the CIS, modernization of the Chinese steel industry, increased scrap utilization in the West, and more efficient blast furnaces in Japan and Korea. While steel demand over the next 30 years is expected to grow at nearly the same rate as global population growth, increased scrap availability, particularly in China, along with renewable energy, will reduce steelmaking’s carbon intensity, McKay said.
Use of scrap and renewable power are categorized as passive abatement levers. Steelmakers get little credit for abatement that comes from these measures. “Although the carbon intensity per steel unit could decrease notably due to the mobilization of these passive levers, if that was all that accrued the industry would fall far short of any decarbonization target,” cautioned McKay. “That underscores the magnitude of the challenge. There is no easy road to a green industry.”
As McKay highlighted three stages for global steel decarbonization, he shifted his attention away from U.S. steelmakers. Focusing on China, the EU, developed Asia Pacific, and India, he argued that steelmaking assets will have to navigate these stages—optimization, transition, and green end state—to become carbon neutral.
The optimization stage—where many steelmaking assets find themselves today—is where energy and raw material optimization is needed. Driven by technology improvement, carbon emission is reduced by 20% in this stage. The second stage, the transition stage, is driven by low carbon fuels, modified blast furnaces, and end of pipe CCUs (carbon capture, utilization and storage). The transition stage will likely carry a 50-60% carbon intensity reduction. The green end state, where 90% of CO2 reduction is achieved, will be driven by hydrogen-based DRI in electric arc furnaces.
“For the industry to produce steel at zero or near zero carbon emissions, hydrogen-based DRI EAF steelmaking is the key long-term pathway to carbon neutrality,” McKay said. “The real challenge with this technology, aside from uncompetitive costs, are the broad system-wide requirements needed to deliver the vast quantities of green-based hydrogen required.”
To put the size of the challenge in perspective, McKay noted that a single, 2 million tonne per year, green hydrogen-based DRI plant would require roughly 3 gigawatts of renewable power and electrolyzed capacity. That would require a 36.7 square mile solar array to power such a plant or the equivalent of two Manhattans. If power were to come from onshore wind, the land requirement increases by a factor of five. “All this for a single plant producing roughly one thousandth of global steel supply in 2050,” he said.
By David Schollaert, David@SteelMarketUpdate.com
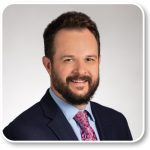
David Schollaert
Read more from David SchollaertLatest in Environment and Energy
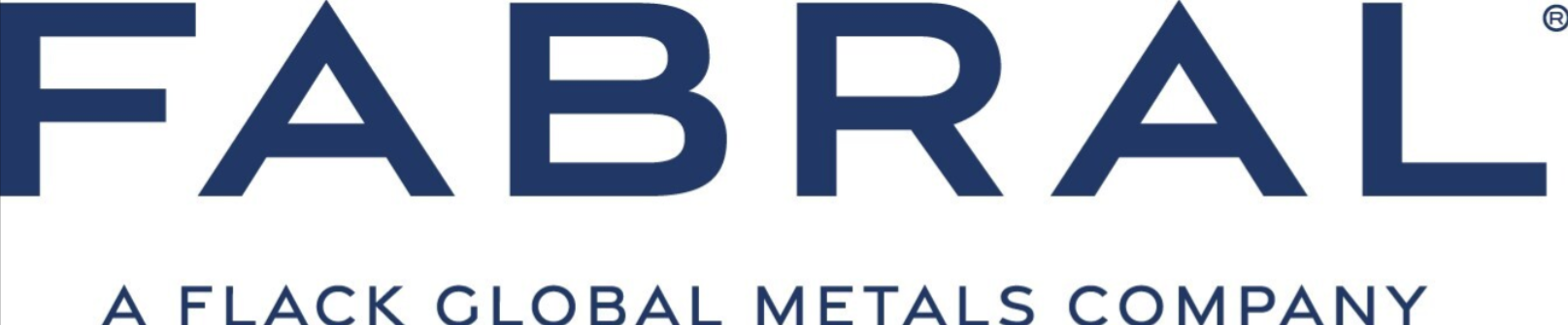
Flack’s Fabral launches solar division
The metal roofing manufacturer is launching Fabral Solar to integrate solar technology within commercial, residential, and agricultural structures.
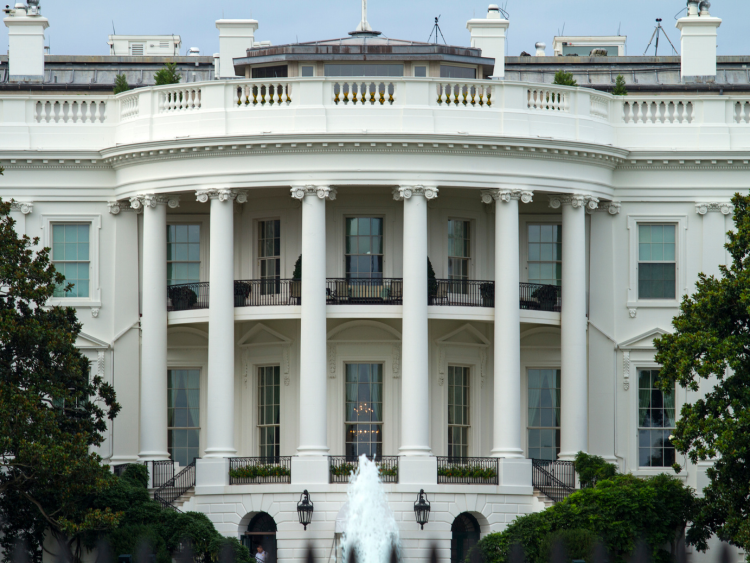
Trump intends to declare ‘national energy emergency,’ focus on fossil fuels
The incoming administration said it also wants to streamline permitting and roll back regulations.
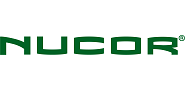
Nucor carbon targets certified by GSCC
Nucor’s “ambitious” carbon targets by the end of the decade and beyond have been certified by the Global Steel Climate Council (GSCC). The Charlotte, N.C.-based steelmaker used a base year of 2023 for its science-based emissions targets (SBET). It set an SBET of 0.975 metric tons (mt) of CO2 emissions per mt of hot-rolled steel […]
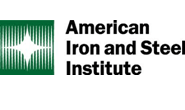
AISI cheers passage of water resources bill in Congress
The American Iron and Steel Institute (AISI) lauded the recent passage of a water resources bill in Congress.
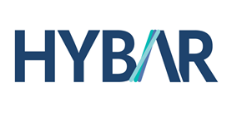
Solar power to supply Hybar’s Arkansas rebar mill
Green & Clean Power will supply electricity to Hybar’s mill that is due to begin operations next summer.