SMU Community Chat
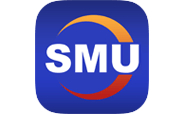
Construction: A Tale of Two Sectors
Written by Sandy Williams
April 1, 2021
Business conditions in the construction industry are split along the residential/nonresidential line, said Ken Simonson, chief economist at the Association of General Contractors of America, who spoke during Wednesday’s SMU Community Chat Webinar. Employment levels in the industry plunged last year at a similar rate between the two segments as the pandemic took hold in March and April. Since then the residential side of the market has recovered more strongly due to support from the Paycheck Protection Program and a surge in home building and home renovations.
Delving into the numbers, it is clear that residential construction fared much better than nonresidential. Residential construction employment rebounded with a 19% annual gain from April 2020 compared to an 8.2% increase for nonresidential. Essentially all of the jobs lost during the early stages of the pandemic in residential construction have been regained as opposed to only half of those in nonresidential construction, AGC reports.
Construction spending further highlights the disparity between the two sectors. Although up 6% overall from January 2020 to January 2021, private residential spending soared 21% while private nonresidential spending plummeted 10%.
Nonresidential segments that increased on an annual rate in January 2021 were mostly in the public category. Highway and street spending gained 6%, benefitting from milder weather. Education gained 7% mostly due to renovations to primary and secondary schools to accommodate safety protocols due to the pandemic. Health care saw an increase in special care units for COVID testing and long-term care.
Commercial construction dipped 8% although warehouse construction gained 2% as demand for last-mile/hour distribution facilities, cold storage, and fulfillment centers at or near airports increased. Retail is expected to remain depressed for quite a while, said Simonson.
Manufacturing passed its low point of a 15% decrease and is showing signs of picking up although remains frustrated by shortages, high raw material pricing and supply-chain delays. Simonson expects the sdministration’s push for wind energy will require new manufacturing facilities as will the transition to electric cars and the subsequent batteries and charging stations.
In the medium term, the economic recovery looks more certain, albeit with continued virus risks, said Simonson. Owners and investors will need to make up lost revenue and regain confidence in demand before committing to new projects. Construction in retail, offices, higher education, and lodging and travel related will remain below pre-pandemic levels, along with less expansion of sports, entertainment and cultural facilities.
Best prospects for public construction will be in K-12 schools. Investment in building projects requiring state and local funding will decrease, especially for higher education.
A concern for the long-run construction outlook (post-pandemic) is the decrease in population. The birth rate fell last year and the death rate accelerated. Population growth (births and migration) from July 2019 to July 2020 declined in 16 states and was less than half a percent in 17 others. California’s population declined for the first time in its history. The long-term impact will be reflected in future school construction, Simonson said.
The reveal of an infrastructure bill by the Biden administration was forefront during the Q&A. Simonson is confident that the House will pass a substantial package with a close vote, but expects getting the legislation through the Senate will be very difficult.
“Right now, my guess is that there will be a modest increase in highway and transit funding, the Senate would go along with that, but any other piece will be difficult to sell,” said Simonson. A long and intensive debate on the package and how to pay for it is expected.
Even if a package sailed through the House and Senate, it would not be until 2022 that the steel industry would see an impact. “It takes weeks, months or even years to get money distributed to agencies, projects designated, permitting completed, contracts awarded and for the contractor to assemble a team and order materials,” said Simonson.
Meanwhile pockets of strong demand in selective categories of manufacturing like Intel’s Phoenix expansion, medical device and pharmaceutical manufacturing, a mix of auto, electric and wind projects will stimulate demand for construction and steel, he added.
Contractor charges have not caught up to higher material prices and will not do so for a long time, said Simonson, noting he has seen periods of 28 months where input costs exceeded contractor bid prices.
Another area that consumes a large quantity of steel is HVAC, which is expected to remain strong. The pandemic created demand for improved airflow in new and existing construction. Anything with steel used in interiors or residential has a good outlook, said Simonson, but hold off on expectations for steel high-rise projects.
Regarding Section 232 tariffs, the AGC has joined a coalition that wants the tariffs “removed pronto,” Simonson said, adding, “we don’t see the administration ready to budge on that.” AGC is also trying to get relief from import tariffs on Canadian softwood lumber, another commodity that has soared for contractors. Simonson expects it will be a long time before relief is available on either front and may even go the other way towards more Made in America steel and lumber.
Simonson was asked if, in light of the current steel shortage, there will be enough U.S. melt and manufactured capacity to fulfill the demands of a new infrastructure bill. He said that is “far down my list of worries” and noted more capacity is coming online later this year. In 2008, as the economy recovered from the Great Recession, there was a rush in demand from all of the construction sectors, which resulted in significant delays for steel and the allocation for gypsum wallboard and many other issues, he said.
“This time the allocation and delay issues are much more related to the pandemic and the surge of demand overall. Hopefully, we will work that out before we get to the recovery in demand. But in two, three or four years from now we could see those capacity restraints become a real issue,” he said.
By Sandy Williams, Sandy@SteelMarketUpdate.com
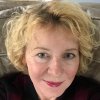
Sandy Williams
Read more from Sandy WilliamsLatest in SMU Community Chat
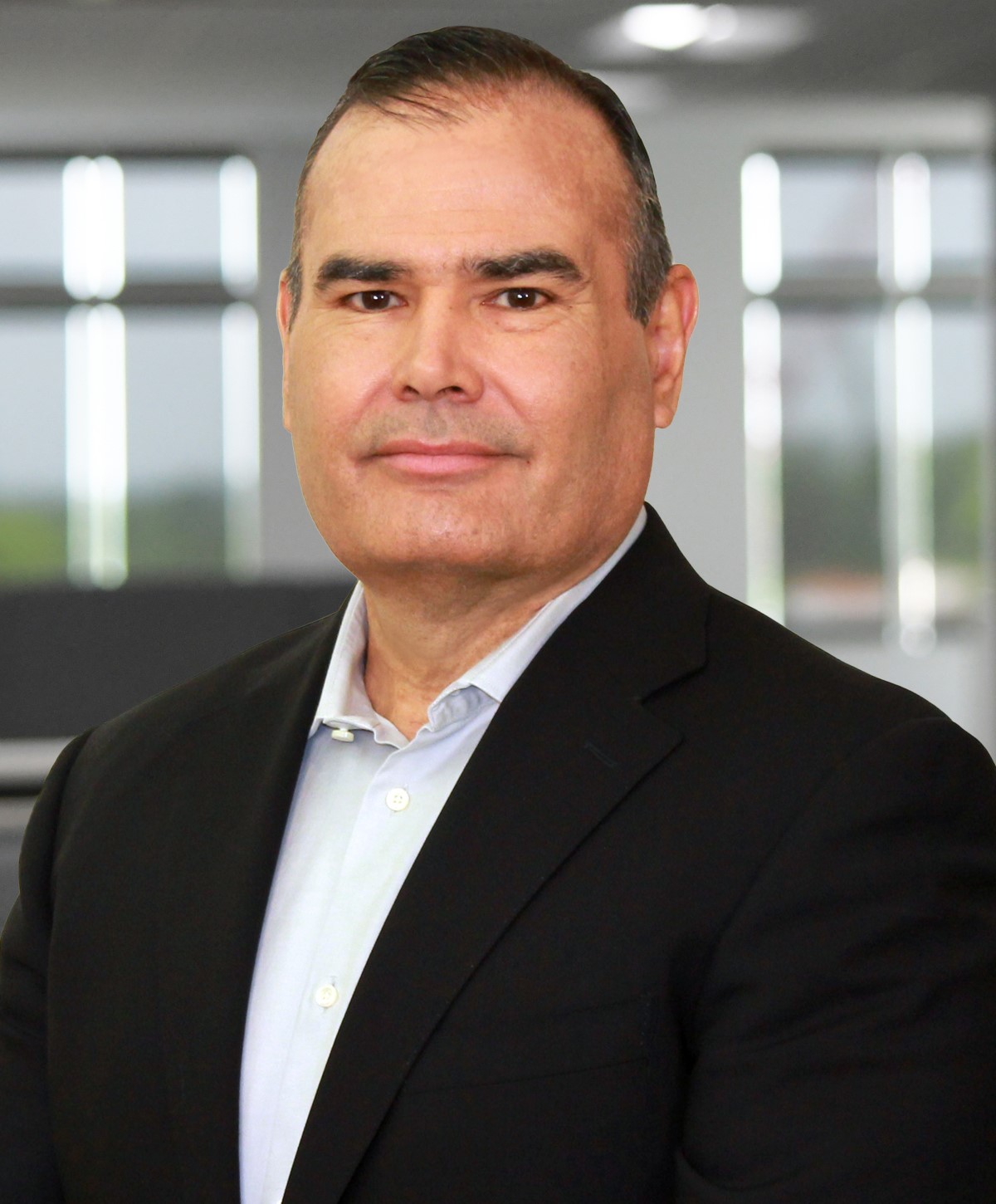
Join us for the April 9 Community Chat with Algoma Steel CEO Michael Garcia
During the chat, we’ll discuss trends in the North American sheet and plate markets, as well as the unique aspects of the Canadian market. We’ll talk all thing tariffs — and the timing couldn’t be better in the wake of Liberation Day on April 2.
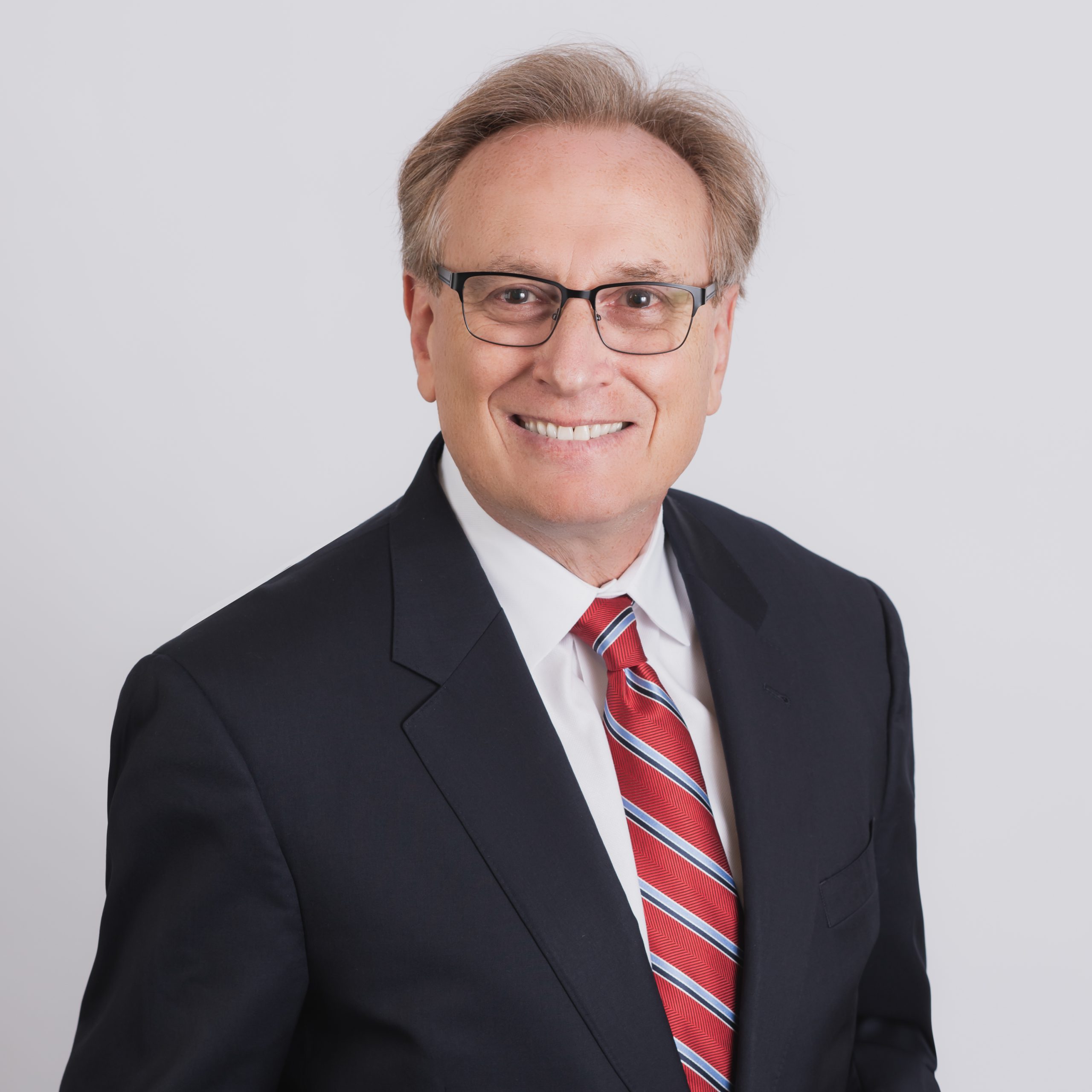
SMU Community Chat: Alan Price unpacks latest in rapidly shifting tariff terrain
International trade attorney Alan Price sat down with SMU to unpack the latest developments in Trump’s tariff merry-go-round.
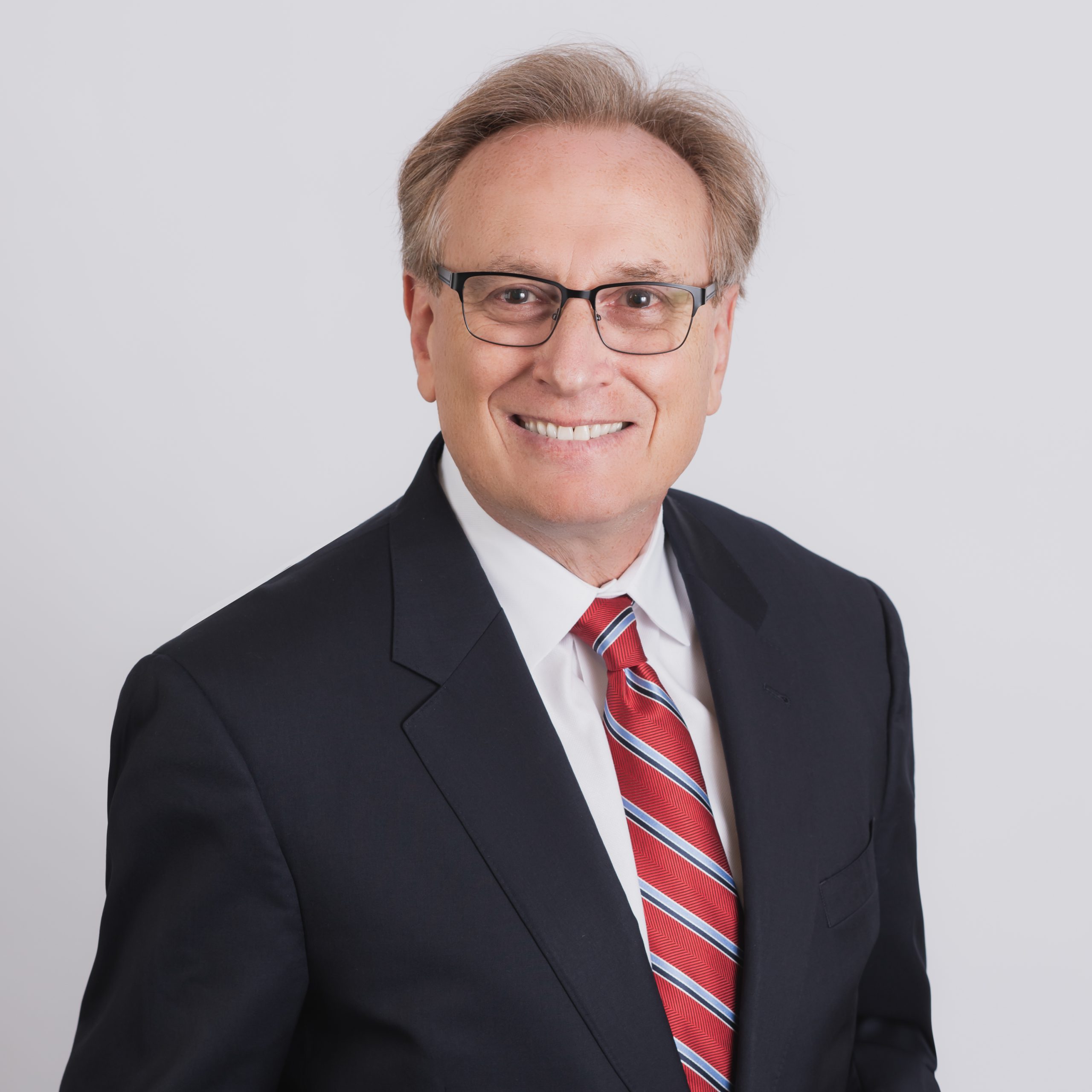
Join SMU for a Community Chat on March 13 With Wiley Trade Attorney Alan Price
Wonder what the fallout from all the Trump tariffs might be? A manufacturing renaissance? A post-WWII order in ashes? Or something a little more down the middle? Then register for our next Community Chat on Thursday, March 13 at 11 am ET. Yes, you read that correctly, SMU is shattering precedent by holding a Community Chat on a day that is not Wednesday. Our featured speaker will be Alan Price, a leading trade attorney at Wiley and someone whose columns you read regularly in SMU.
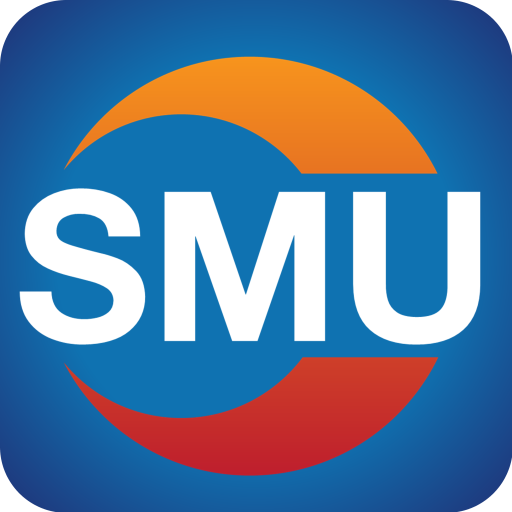
SMU Community Chat: CRU’s Josh Spoores looks out over the Trump 2.0 battlefield
SMU Community Chat with CRU's Josh Spoores.
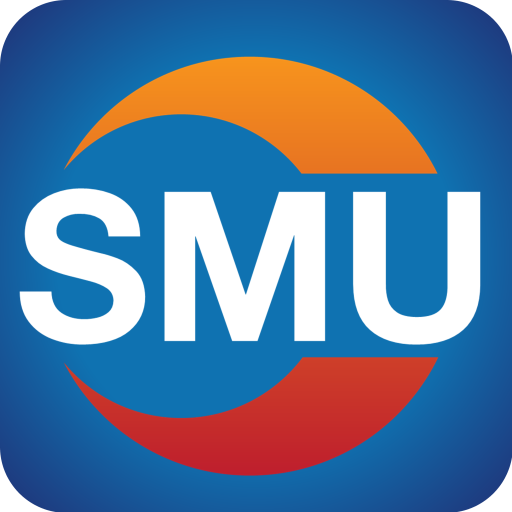
Join AWMI and SMU for a Community Chat webinar on steel AND aluminum
It’s been an eventful (and chaotic) start to the year for steel and aluminum as industry tries to navigate new Trump administration.