Steel Mills
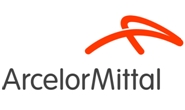
Pandemic Brings Loss, Structural Changes to ArcelorMittal
Written by Tim Triplett
July 30, 2020
Learning to do more with less during the COVID crisis is bringing structural changes to ArcelorMittal, said Aditya Mittal, president and CFO of the world’s largest integrated steel and mining company, during today’s second-quarter report to analysts and investors.
Without offering specifics about which assets will be affected in pursuit of cost savings, Mittal said the company is focused on retaining market share. He struck a positive tone, considering the company’s Q2 losses. “We see recovery momentum across all the regions in which we operate.”
ArcelorMittal reported a net loss of $559 million in the second quarter as steel shipments suffered a 23.7 percent decline due to the coronavirus pandemic. Sales for the quarter totaled about $11 billion, down from $14.8 billion in the first quarter and $19.3 billion in the same quarter last year.
“The first six months of the year, and particularly the second quarter, have been one of the most difficult periods in the history of the company, with demand for steel considerably disrupted by the COVID-19 pandemic,” said Lakshmi Mittal, ArcelorMittal Chairman and CEO. The company has implemented a range of measures to strengthen its balance sheet, he said, including reducing production by temporarily idling steelmaking and finishing assets, and cutting capex and fixed costs, as well as raising capital. “There are now signs of activity picking up, especially in regions where lockdowns have ended, but clearly it is prudent to remain cautious about the outlook. Against this context, we are examining what structural changes might be required to ensure the company is well configured to prosper in the coming years as demand recovers.”
ArcelorMittal’s global steel shipments in the first half of 2020 totaled 34.3 million metric tons, a decrease of 23 percent from first-half 2019. Shipments were 13.2 percent lower in the NAFTA region, 31 percent lower in Europe and 22 percent lower in Brazil due to the impact of the coronavirus. First-half sales decreased by 33 percent to $25.8 billion, compared with $38.5 billion in the same period last year.
Crude steel production in the NAFTA segment decreased by nearly 33 percent in Q2 to 3.7 million tons, down from 5.5 million tons in the first quarter. Escalation of the COVID-19 pandemic in late Q1 impacted ArcelorMittal’s key end markets in the U.S. and Canada, particularly the automotive and energy sectors. The company responded immediately by significantly reducing its capacity, which continued during Q2. As the quarter progressed, steel shipments started to recover as lockdown measures eased and automotive production and manufacturing activity restarted. NAFTA segment sales in Q2 decreased by about 36 percent to $2.8 billion due to a 31 percent decrease in steel shipments and a 6.3 percent decline in average steel selling prices, with flat steel prices down by 6.8 percent and long products prices up by 2.9 percent.
The easing of lockdown measures has seen activity levels improve. Nevertheless, demand remains significantly below normal and the pace and profile of recovery is uncertain, company executives said. ArcelorMittal continues to adapt production levels to market demand (one example is the recently announced layoff of 454 workers at ArcelorMittal Cleveland) and maintains the flexibility to quickly restart hot idled capacity, on a region by region basis, as demand improves.
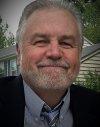
Tim Triplett
Read more from Tim TriplettLatest in Steel Mills
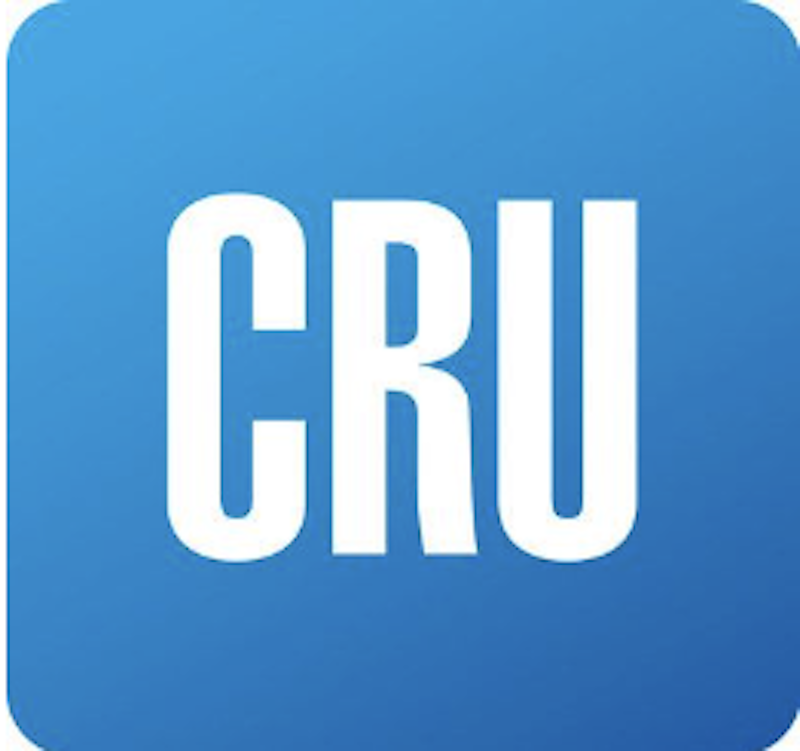
CRU: Tata Steel looks to shed 1,600 jobs in the Netherlands
The company said, “The challenging demand conditions in Europe driven by geopolitical developments, trade and supply chain disruptions and escalating energy costs have affected the operating costs and financial performance."

Reports: Federal funding for Cliffs’ project could be slashed
Elon Musk's DOGE is determining which Department of Energy grants to advance and which ones to terminate, according to several media outlets
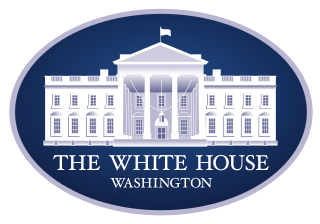
Trump still against selling USS to Japanese firm: Report
Despite ordering a new review of Nippon Steel’s bid for U.S. Steel, President Trump said he is still against selling USS to a Japanese company, according to media reports.
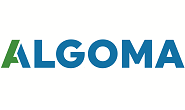
Algoma looks to sell more steel in Canada in wake of Trump’s tariffs
The Canadian steelmaker said its absorbing higher tariffs as it moves forward.
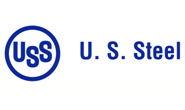
Ancora abandons plan to take over leadership of USS
Investment firm Ancora Holdings Group has halted its play for U.S. Steel's board, citing Nippon Steel’s proposed bid for USS “gaining momentum.”