Steel Mills
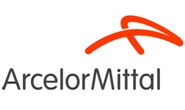
ArcelorMittal Reports Billion Dollar Loss in Q1
Written by Sandy Williams
May 7, 2020
International steelmaker ArcelorMittal was hit particularly hard by the pandemic, dealing with closures and economic recessions across the globe. The company reported a loss of $1.1 billion for the first quarter of 2020 and expects the remainder of the year to be challenging.
“There are still too many uncertainties to accurately predict what the rest of the year holds,” said Chairman and CEO Lakshmi Mittal. “However, it seems likely that over the course of this month countries will start to announce details of their ‘exit’ strategies. Whilst these are likely to be an easing, not an immediate ending of lockdown, construction and manufacturing are expected to be among the first sectors to be permitted to re-start operations, and indeed we are seeing signs of customers re-starting production. Rigorous planning to ensure we can meet customer demand whilst protecting the health and safety of our people has been undertaken, leaning on the experience of our plants which have already been on this journey.”
The company moved quickly to cut costs, temporarily idling furnaces, cutting production and workforce to match demand, and reducing operating and capital costs. Steel shipments of 19.5 metric tons were 1.2 percent lower than Q4 2019 primarily due to lower shipments in Brazil and ACIS. Shipments from the NAFTA segment were up 10.1 percent and were mostly stable in Europe. Sales fell 22 percent year-over-year to $14.84 billion due to impacts on shipments related to the coronavirus.
Shipments are expected to be in the range of 13.5 million to 14.5 million metric tons during the third quarter, a decline of 25 to 30 percent from the first quarter.
“At this point in time, all the fixed cost savings that we have outlined are temporary in nature,” said President and CFO Aditya Mittal during the earnings call. “Clearly, it’s very hard to predict the future. We all have limited visibility. To the extent that demand levels don’t come back to pre-crisis levels, then we would review how to make some of these temporary fixed cost savings more permanent in nature and look for structural cost measures.”
The NAFTA segment saw crude steel production increase 4.6 percent to 5.5 million metric tons from the fourth to the first quarter, driven by a 12.2 percent increase in flat steel shipments mostly in the early part of the quarter. Shipments declined in March with demand falling as a result of the pandemic.
NAFTA sales rose 7.1 percent from Q4 to $4.3 billion due to increased steel shipments, offset by declines in flat and long steel prices. The company temporarily idled the #3 blast furnace at Dofasco, #5 in Cleveland, and #4 at Indiana Harbor, reducing production and workforce to align with deteriorating demand resulting from the COVID-19 crisis.
Non-essential capex projects in the segment have been suspended other than the Mexico hot strip mill, which is close to completion. The Dofasco hot strip mill modernization is expected to be completed in 2021 and installation of two walking beam furnaces at Burns Harbor later in 2020.
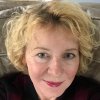
Sandy Williams
Read more from Sandy WilliamsLatest in Steel Mills
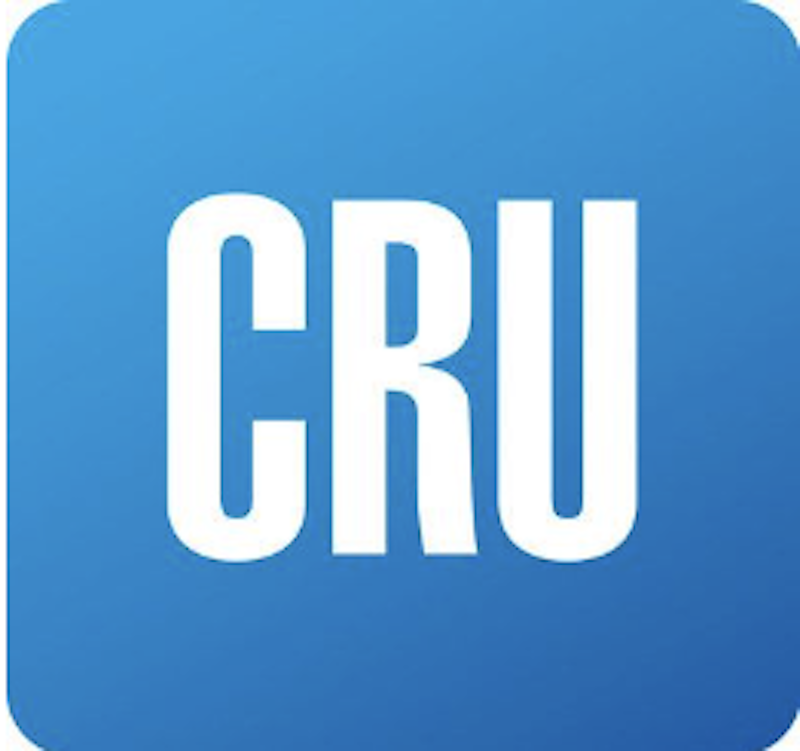
CRU: Tata Steel looks to shed 1,600 jobs in the Netherlands
The company said, “The challenging demand conditions in Europe driven by geopolitical developments, trade and supply chain disruptions and escalating energy costs have affected the operating costs and financial performance."

Reports: Federal funding for Cliffs’ project could be slashed
Elon Musk's DOGE is determining which Department of Energy grants to advance and which ones to terminate, according to several media outlets
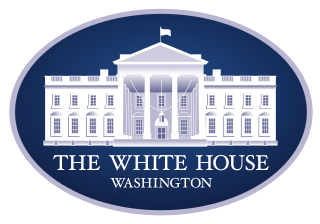
Trump still against selling USS to Japanese firm: Report
Despite ordering a new review of Nippon Steel’s bid for U.S. Steel, President Trump said he is still against selling USS to a Japanese company, according to media reports.
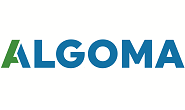
Algoma looks to sell more steel in Canada in wake of Trump’s tariffs
The Canadian steelmaker said its absorbing higher tariffs as it moves forward.
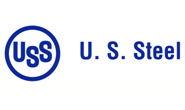
Ancora abandons plan to take over leadership of USS
Investment firm Ancora Holdings Group has halted its play for U.S. Steel's board, citing Nippon Steel’s proposed bid for USS “gaining momentum.”