International Steel Mills
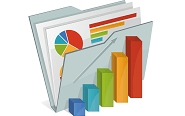
Green Steel Movement Faces Technical Hurdles
Written by Tim Triplett
January 2, 2020
Climate change is moving up the political agenda in countries around the world, putting increasing pressure on industries such as steel to reduce greenhouse gases. Globally, the steel industry is responsible for around 5 percent of total CO2 emissions. Steelmakers are responding with plans for mills that run on solar or wind energy and are spending millions on research into breakthrough technologies such as hydrogen-fueled furnaces and carbon capture and storage. It all sounds very promising, but a nightmare’s worth of R&D stands between the current steelmaking technology and the dream of true “fossil-free” steel, say the experts.
Mills all over the world are making headlines with their ambitious environmental initiatives. Nucor claims its micromill in Sedalia, Mo., will be the first U.S. steel plant to run on wind energy. EVRAZ North America’s mill in Pueblo, Colo., will be powered by an on-site, 240MW solar power plant. SSAB Americas claims it will be the first supplier of “fossil-free steel” in North America, operating its Montpelier, Iowa, minimill solely with renewable energy by 2026.
It’s important to note that the term “fossil-free steel” does not mean “CO2 free steel,” said CRU Senior Analyst Ryan Smith. Fossil-free means only that the sources of carbon involved in the production process are from renewable sources rather than nonrenewable fossil fuels.
SSAB’s minimill will remelt scrap in an electric arc furnace using electricity generated primarily by wind power, which addresses the electricity component of CO2 emissions. But it will still require the use of a graphite electrode to deliver the charge and the addition of metallics such as pig iron, DRI or HBI to dilute the residuals, among other carbon-based requirements. “Graphite electrodes are produced using needle coke, which is an oil derivative. There is no known commercially viable substitute to my knowledge, so this is one of the biggest hurdles to fossil-free steel,” Smith said. “At this stage, I can’t see how true ‘fossil-free’ can be achieved by 2026.”
CRU reports that most of the world’s steel is produced today using the more CO2 intensive Blast Furnace-Basic Oxygen Furnace (BF-BOF) method. Of the 1,786 Mt of crude steel produced in 2018, BF-BOF production accounted for approximately 72 percent, with an average CO2 intensity of 1.60 t CO2/t crude steel. Electric Arc Furnaces (EAFs) make up most of the remainder at around 27 percent, with a much lower Scope 1 CO2 intensity of 0.24 t CO2/t steel. While minimill EAFs continue to supplant the blast furnaces at the integrated mills, this is only a partial solution, as not enough scrap is generated globally to fulfill the demand for crude steel.
Much of the R&D into new steelmaking technologies is happening in Europe, where the EU’s Emissions Trading Scheme has increased the cost of emitting greenhouse gases and provided an economic incentive for companies to reduce emissions. HBIS in China also has recently announced it will be developing hydrogen-based steelmaking. Several major steel companies are experimenting with ways to replace carbon-based reductants, such as coke, with hydrogen in both the BF and DRI processes. However, despite its low CO2 emissions in the steelmaking process, most hydrogen today is produced from fossil fuels and, therefore, has its own CO2 footprint.
Carbon Capture and Storage (CCS) is another technology under consideration. CRU’s research into CCS in China showed that it could reduce CO2 emissions by up to 33 percent, but it would also increase steel production costs by an estimated $70 /t, making it cost prohibitive.
For countries to meet global emissions targets, there will need to be a significant change to the way steel is produced. Technical, economic and political hurdles are unlikely to allow a quick transition to new steelmaking methods, however. Yet, as CRU points out, the steel mills are feeling a growing sense of urgency to demonstrate their green credentials as the public and investors grow increasingly discontented with industries that pollute.
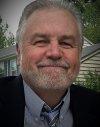
Tim Triplett
Read more from Tim TriplettLatest in International Steel Mills
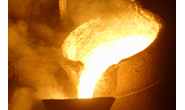
Global steel mill output steady through May
Global raw steel production rose 2% from April to May, slightly above average production levels seen in recent months, according to data recently released by the World Steel Association (worldsteel).
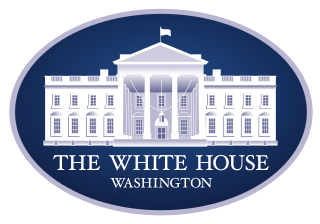
Trump says US government to control 51% share in USS
President Trump says the US government will hold a 51% stake in U.S. Steel after the Nippon deal.
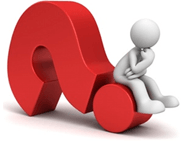
USS, Nippon Steel quiet as litigation deadline approaches
There has been little word from U.S. Steel, Nippon Steel, or the White House since President Trump endorsed the companies’ “partnership” on social media and celebrated it at the May 30 rally outside Pittsburgh.
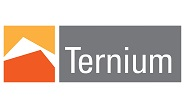
Ternium’s Vedoya named AIST’s Steelmaker of the Year
Maximo Vedoya was awarded in recognition of Ternium’s expansion project in Pesquería, Mexico, and Ternium’s efforts to decarbonize steelmaking.
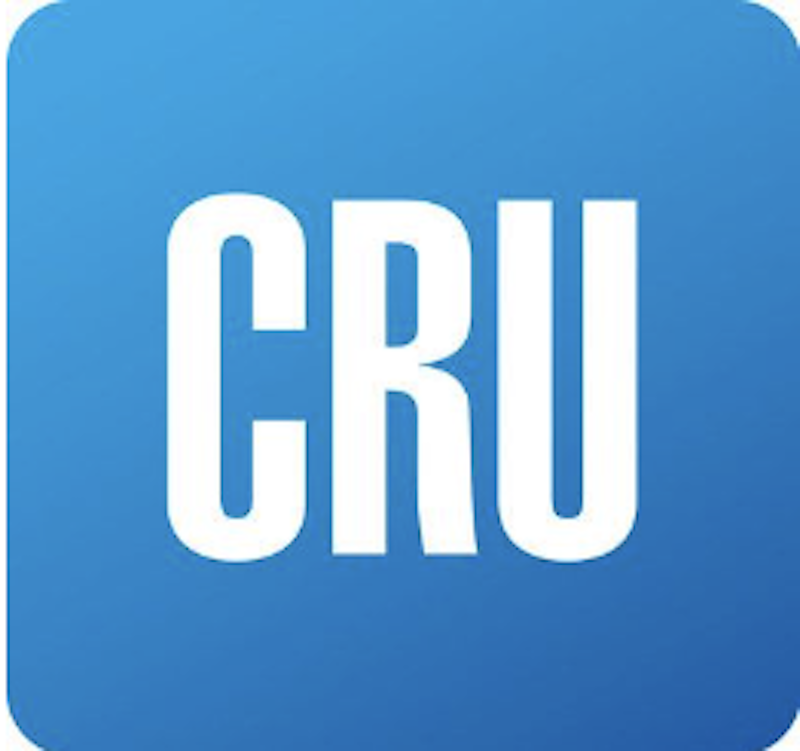
CRU: Baosteel hints at output cuts in China
Baosteel exec comments on market rumors of 50 million tons of output being cut this year, less than 0.5% of the 1 billion tons-plus China has produced annually in recent years.