Steel Mills
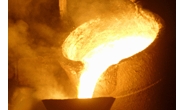
Blast Furnaces Still Strong at Integrated Mills
Written by Sandy Williams
August 14, 2019
Electric arc furnace minimills may have a cost advantage in steel production today, but there are still 19 traditional blast furnaces going strong in the United States.
Blast furnaces dominate about three-fourths of global steelmaking, but only three steel producers in the U.S. currently are using BF or basic oxygen furnace technology: U.S. Steel, ArcelorMittal and AK Steel. Combined, their 19 furnaces have an annual production capability of approximately 36 million tons. In total, U.S. steelmakers produce roughly 90 million tons annually.
U.S. Steel was the last to build a new BF in the United States. Commissioned in 2007 at U.S. Steel Gary Works, the No. 14 furnace replaced No.13 at a price tag of more than $300 million.
“The rebuild of No. 14, with a 20-year life expectancy, is a significant financial investment in Gary Works and a demonstration of our commitment to our customers, work force and community,” said then U.S. Steel spokesman John Armstrong. Standing 300 feet tall, the new furnace increased daily melted metal output from 2,155 tons to 9,200 tons.
The last integrated blast furnace mill to be built in the U.S. was completed by Bethlehem Steel in 1969. Bethlehem filed for bankruptcy in 2001 and the mill passed to International Steel Group. The mill was bought by ArcelorMittal in 2005. ArcelorMittal Burns Harbor, now operating furnaces C and D, recently celebrated Burns Harbor’s fiftieth anniversary.
Blast furnace steel is still prized for its quality and strength for use in automotive applications, although steel produced from EAF technology is quickly catching up.
“AK Steel operates both blast furnaces and electric arc furnaces and realizes the unique benefits of both manufacturing processes,” said AK Steel spokeswoman Lisa Jester. “As a producer of advanced high-strength and exposed steels for the automotive sector, some of which are only made in blast furnaces, AK Steel continually creates new innovative products while remaining cost competitive with other steel producers who supply automotive and other customers with demanding requirements.”
AK Steel operates two blast furnaces—one at Dearborn and one at Middletown, plus three EAFs—two at its stainless steel melting and casting facility at Mansfield Works and one at the electrical and stainless steel facility at Butler. U.S. Steel has 10 BFs in operation and is proceeding with construction of its first EAF, in Fairfield, Ala., which will have a 1.6 million ton annual capacity.
ArcelorMittal USA has seven operational blast furnaces, an EAF at its plate mill in Coatesville, Pa., and one at its rail production operation in Steelton, Pa.
Canada currently has three integrated mills—ArcelorMittal Dofasco with three BFs and Stelco and Algoma with one each. Mexican producer AHMSA operates two blast furnaces and ArcelorMittal Mexico one.
EAF Gains Market Share
EAF steel production was introduced to the U.S. in 1969 when Nucor opened its first minimill in South Carolina. Initially, EAFs primarily produced construction-grade long products such as rebar. In 1989, Nucor’s Indiana mill began producing sheet steel, and other mills soon followed.
Integrated steel producers have been losing market share to minimills since the late 1980s as the scrap-based EAF production process offers significantly lower raw material costs. The chart below from the American Iron and Steel Institute shows integrated and minimill market share equalizing in 2002 and EAFs capturing nearly 70 percent of the market by 2018.
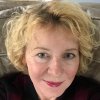
Sandy Williams
Read more from Sandy WilliamsLatest in Steel Mills
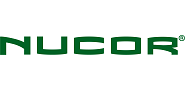
Nucor’s Topalian lauds Trump’s trade policies, downplays impact
Nucor’s top exec Leon Topalian said the benefit of the current administration’s aggressive trade policies “trumps” any risk of potentially higher raw materials prices.
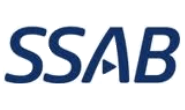
SSAB reports higher production, shipments
But profits slipped vs. last year.
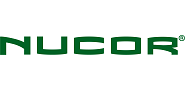
Nucor earnings slump in first quarter, but better times seen ahead
Nucor’s profits fell precipitously in the first quarter, but the company has a rosier outlook for the following quarter.
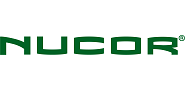
Nucor names Batterbee, Bledsoe to HR roles
Nucor Corp. has promoted Thomas J. Batterbee to the position EVP of human resources and talent and appointed Elizabeth Bledsoe to the newly created position of president of human resources and talent.
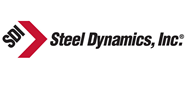
Millett sees tariffs, CORE case benefiting SDI
Steel Dynamics' top exec thinks Trump’s tariff policies, as well as the results from the recent CORE case, will prove advantageous to the Fort Wayne, Ind.-based steelmaker and aluminum company.