Steel Mills
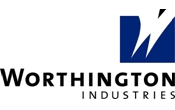
Tariffs Add "Noise" to Worthington's Earnings Report
Written by Sandy Williams
March 21, 2019
Worthington Industries President Andy Rose described the third quarter of fiscal year 2019 as a “noisy period” in terms of earnings.
“There continues to be a lot of noise in our third-quarter results,” said Rose. “The biggest challenge we have been facing is the steel tariffs, which have created artificial pricing mechanics that should have minimal long-term impact on our business but have created short-term margin pressure. Steel price fluctuations impacted all of our businesses in Q3.”
Higher raw material input costs for steel and helium in the past few quarters have impacted the cylinder segment, but Rose said recent prices increases are finally beginning to cover those costs.
“Recent declines in steel prices hindered margins and volumes in steel processing,” he added. “The good news is that demand remains good in almost all of our end markets. So, as mitigation efforts take effect to offset these cost pressures, we expect to see margins improve.”
Net sales for the quarter totaled $874.4 million, up 4 percent from Q3 2019. The increase was primarily driven by higher average direct selling prices in Steel Processing, partially offset by lower direct volume in Steel Processing and the impact of current year divestitures in Pressure Cylinders.
Net earnings for the quarter were $26.8 million, down from $34 million in Q2 and $1.27 million in Q3 2018.
Margins were impacted by a $13.0 million charge in Pressure Cylinders associated with the replacement of certain composite hydrogen fuel tanks produced primarily between 2012 and 2015. The hydrogen tanks were built to ISO standards but some of the ISO certification tests were not completed, resulting in a decision to replace tanks sold to a customer. The replacement program should be completed within six months.
“We continued to feel the impact of higher input costs and volatility in steel prices, but we also made good progress toward recovering margin as the quarter progressed,” said John McConnell, Chairman and CEO. “We believe that we are through the worst of the recent cost pressures, and I’m proud of the way our teams have executed.”
The drop in steel processing was largely due to automotive weakness from domestic auto producers, said Rose. December was also slow as customers waited for the January reset in pricing.
“Despite recent headwinds, the company is performing well, and we remain focused on driving improvements throughout our businesses,” McConnell said in outlook remarks. “Overall, our markets remain steady. We expect to see continued margin expansion in Pressure Cylinders, but also anticipate continued inventory holding losses in Steel Processing in the upcoming quarter.”
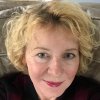
Sandy Williams
Read more from Sandy WilliamsLatest in Steel Mills
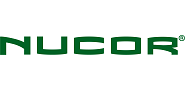
Nucor names Batterbee, Bledsoe to HR roles
Nucor Corp. has promoted Thomas J. Batterbee to the position EVP of human resources and talent and appointed Elizabeth Bledsoe to the newly created position of president of human resources and talent.
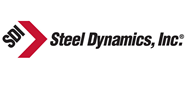
Millett sees tariffs, CORE case benefiting SDI
Steel Dynamics' top exec thinks Trump’s tariff policies, as well as the results from the recent CORE case, will prove advantageous to the Fort Wayne, Ind.-based steelmaker and aluminum company.
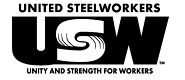
USW digs in on opposition to USS-Nippon deal
“We remain deeply concerned about the national and economic security implications of the subject transaction,” the union stated in the letter dated April 21.
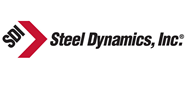
SDI’s Q1 earnings slump on-year, but up sequentially
SDI earnings slip in first quarter year over year, but are up sequentially.
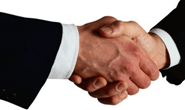
POSCO inks MoU with Hyundai on Louisiana EAF mill
POSCO has signed a Memorandum of Understanding (MoU) with Hyundai Motor Group that includes an equity investment in Hyundai’s previously announced EAF mill set to be built in Louisiana.