Steel Mills
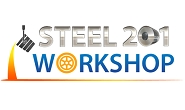
First Steel 201 Workshop Spotlights AK Steel's R&D
Written by Tim Triplett
September 12, 2018
AK Steel co-hosted Steel Market Update’s first Steel 201: Introduction to Advanced High Strength & Other New Steels workshop this week at the $36 million AK Research and Innovation Center opened last year in Middletown, Ohio. The beautiful 135,000-square-foot facility made AK Steel’s commitment to R&D readily apparent to the 40+ students and staff assembled there for the workshop.
AK General Manager of Products J.B. Chronister described the company’s philosophy as its staff of research scientists challenge the laws of physics to create new advanced high-strength steels. “It’s OK to fail, but fail fast, then move on,” he said. It’s not enough to simply develop new products; they must be both profitable for the company and cost-effective for the customer. New steels must also be economical versus competitive materials, most notably aluminum, whose own research establishment is hard at work developing products to win market share from steel in various automotive applications.
In the 1960s, steelmakers offered just seven different steels to the marketplace. Today, thanks to the R&D of AK and other steel companies, there are more than 200 different types of steel. AK has helped to lead the way in the development of next-generation AHSS and specialty steels, working with automakers to design lighter, more fuel-efficient vehicles.
As AK Research and Innovation Engineer Jeremy Hansman explained, development of higher-strength steels has focused on a number of different processes and materials. They range from bake hardened to dual phase to TRIP (transformation induced plasticity) to TWIP (twinning induced plasticity), to martensitics and more. The science is complex, but the challenge is simple to understand. Each new alloy represents a tradeoff between hardness and elasticity. With a harder, stronger steel, parts can be made thinner and lighter. But the steel cannot be so hard that parts are no longer formable. As Dean Linders of Red Bud Industries explained during his processing presentation to the gathering, some new-generation steels are so hard they are extremely challenging to level, slit or cut to length—processes that are essential to the supply chain.
AK is also the leading supplier of grain-oriented and non-grain-oriented electrical steels in the U.S. which help the nation’s electrical grid become more energy efficient and improve the performance of electric motors for hybrid and electric vehicles.
AK’s new stainless and aluminized steels offer superior corrosion resistance for a variety of applications, such as vehicle exhaust systems. As Paul Shefcyk, manager of applications engineering, pointed out during the tour of the facility, Midas Muffler had to reinvent itself as a full-service auto repair business because mufflers today, made of rust-resistant stainless and aluminized steels, often outlast the rest of the vehicle.
The AK executives emphasized their interest in collaborating with customers on new product development, which presents a chicken-or-the-egg sort of dilemma. What comes first? Should the mill develop a new steel and then find customers who can benefit from its new properties or should the customer approach the mill with a problem and then have researchers try to solve it? At AK, it’s a bit of both. “With a culture focused on both innovation and collaboration, new products and processes can be developed more efficiently and launched faster,” the company says.
As part of the Steel 201 workshop, the group toured both the Research and Innovation Center and AK Steel Middletown Works, which is a fully integrated steel mill.
Steel Market Update thanks the AK Steel management and their entire team for allowing us to use their facility, work with their industry experts, tour their mill and impart knowledge that will be beneficial to those who attended our workshop in the months and years ahead.
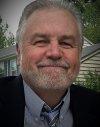
Tim Triplett
Read more from Tim TriplettLatest in Steel Mills
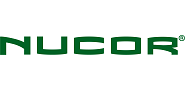
Nucor names Batterbee, Bledsoe to HR roles
Nucor Corp. has promoted Thomas J. Batterbee to the position EVP of human resources and talent and appointed Elizabeth Bledsoe to the newly created position of president of human resources and talent.
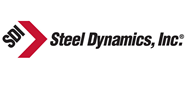
Millett sees tariffs, CORE case benefiting SDI
Steel Dynamics' top exec thinks Trump’s tariff policies, as well as the results from the recent CORE case, will prove advantageous to the Fort Wayne, Ind.-based steelmaker and aluminum company.
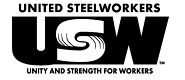
USW digs in on opposition to USS-Nippon deal
“We remain deeply concerned about the national and economic security implications of the subject transaction,” the union stated in the letter dated April 21.
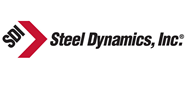
SDI’s Q1 earnings slump on-year, but up sequentially
SDI earnings slip in first quarter year over year, but are up sequentially.
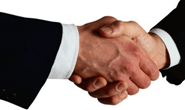
POSCO inks MoU with Hyundai on Louisiana EAF mill
POSCO has signed a Memorandum of Understanding (MoU) with Hyundai Motor Group that includes an equity investment in Hyundai’s previously announced EAF mill set to be built in Louisiana.