Steel Markets
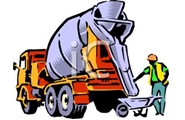
Tariffs Undermining Construction as Materials Prices Jump
Written by Sandy Williams
May 10, 2018
Construction costs are surging as tariffs drive prices up for a wide range of building materials, said a new analysis of Labor Department data by the Associated General Contractors of America. Firms are facing higher input prices that they are unable to pass along to customers.
“Contractors have started to boost the prices they charge, but they are falling further behind on the cost of materials they buy,” said the association’s chief economist, Ken Simonson. “This imbalance poses two risks—either contractors will suffer decreased profit margins or project owners with fixed budgets will cut back on the projects they undertake.”
The producer price index for construction inputs rose 1.0 percent in April and 6.4 percent in the last 12 months, for the steepest year-over-year increase since 2011, noted AGC. The index measuring what contractors charge for construction of nonresidential buildings, like schools, offices and warehouses, rose 1.1 percent from March and 4.2 percent year-over-year.
“The gap between the 6.4 percent rise in the cost of construction goods and the 4.2 percent increase in prices charged is ominous,” Simonson observed. “Unfortunately, the gap may widen further if tariffs or quotas push up costs further for the many steel, aluminum and wood products used in construction.”
The April producer price index jumped by 11.9 percent in the last 12 months for aluminum mill shapes, 11.0 percent for lumber and plywood, and 7.4 percent for steel mill products. Other construction inputs that rose in April include: diesel fuel, 41.6 percent; copper and brass mill shapes, 10.5 percent; gypsum products, 7.5 percent; ready-mix concrete, 6.9 percent; and truck transportation of freight, 6.0 percent.
As metal and lumber prices continue to surge, contractors will need to charge more, which may result in projects lost or delayed.
“The new tariffs have the potential to undermine many of the benefits of the president’s recently enacted tax and regulatory reforms,” said Stephen E. Sandherr, the association’s chief executive officer. “Instead of investing their tax savings in new personnel and equipment, many firms are being forced to use them to cover increasing steel and aluminum costs.”
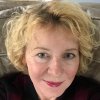
Sandy Williams
Read more from Sandy WilliamsLatest in Steel Markets
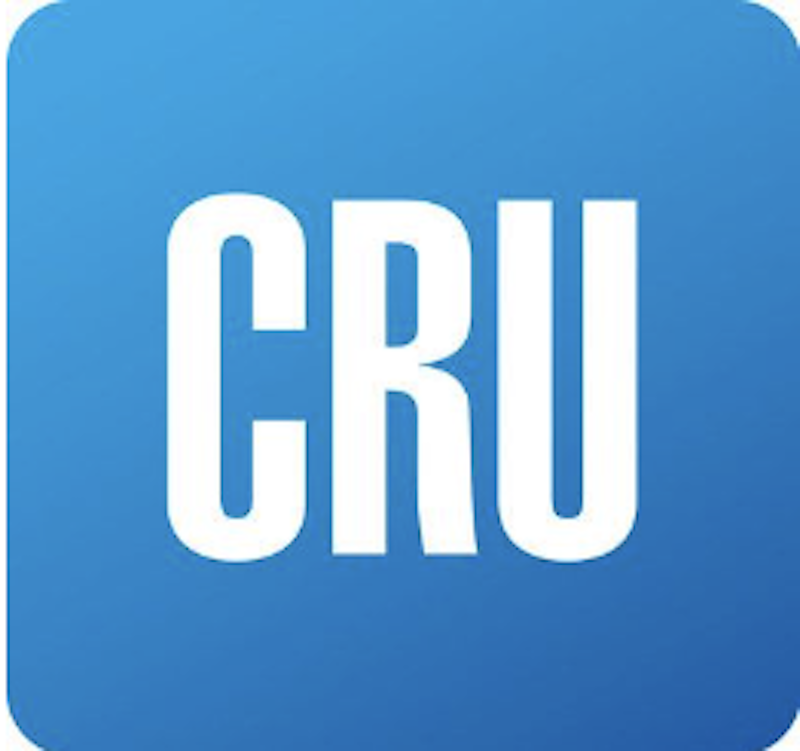
CRU: Sheet import demand softens as domestic price gains have slowed
US domestic sheet price gains have begun to slow as previously pulled-forward demand has led to a decline in orders.
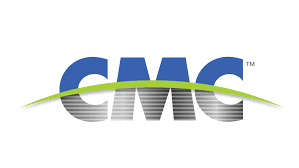
CMC looks beyond Arizona micro-mill woes to long-term viability of construction mart
Despite the economic and geopolitical upheaval of the last five years, CMC President and CEO Peter Matt points out that the construction market has been an essential element of the way forward.
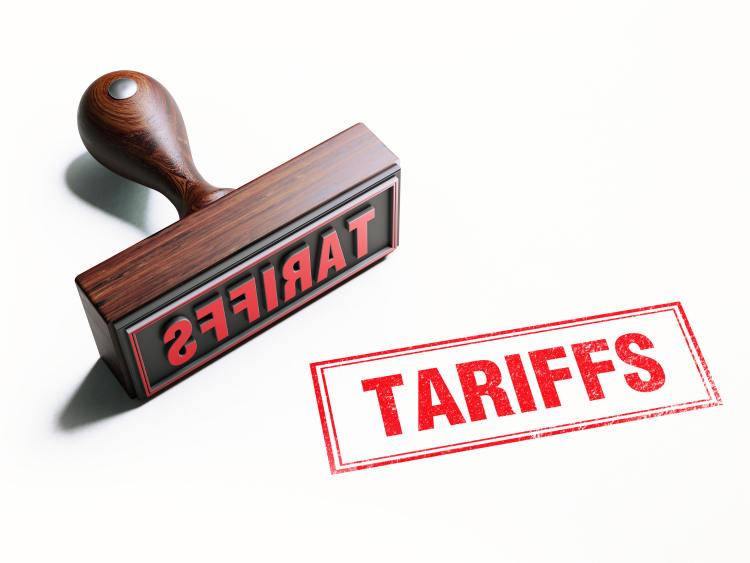
US importers face stricter rules under revamped S232 tariffs
“CBP expects full compliance from the trade community for accurate reporting and payment of the additional duties. CBP will take enforcement action on non-compliance," the agency said in a March 7 bulletin.
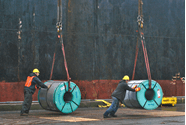
Steel exports rebound in January
US steel exports recovered to a five-month high in January after having fallen to a two-year low in December. This growth follows four consecutive months of declining exports.
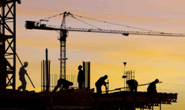
Construction spending drops marginally in January
Construction spending edged down slightly in January, slipping for the first time in four months. The US Census Bureau estimated spending at a seasonally adjusted annual rate of $2,196 billion in January, down 0.2% from December’s downward revised rate. The January figure is 3.3% higher than a year ago. January’s result, despite the slight erosion, […]