Economy
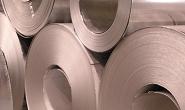
GOES Barriers to Entry Breached
Written by Tim Triplett
December 21, 2017
Following is an edited excerpt of a new monthly publication, “The GOES Chronicle,” from Steel-Insights. For further details, contact Becky E. Hites at becky.hites@steel-insights.com.
Production of Grain Oriented Electrical Steel (GOES) has undergone a tectonic shift in the past decade. The market historically has been supplied through a controlled group of companies protected from outside producers by substantial barriers to entry, including technical know-how, licensing by product developers and high capital costs. That has all changed in the past decade, which has seen a 77 percent increase in GOES production and an 84 percent increase in GOES capacity, as new production practices have made the process more forgiving and less cost-prohibitive. Products that in the past required decades to perfect are now being produced to acceptable market quality by mills less than a decade old. The competition makes the profitability of even the highest quality GOES products less guaranteed, even in the face of consistently growing demand.
The new production process also has changed how products are marketed with many suppliers consolidating thickness categories and magnetic property ranges into more “standardized” offerings with a targeted magnetic loss per thickness category. Consequently, in some instances, “higher grade” (high permeability-HB) products are being sold in the standard grade (regular grain oriented or RGO) categories, as some producers have streamlined production into a single process to reduce cost.
The market has also experienced a dramatic change on the demand side as global economic growth and the emergence of the “developing worlds” has resulted in greater electricity usage requiring increased production and distribution of power to the market. Growing global electricity demand and massive developing world infrastructure investment has resulted in steadily expanding consumption of electrical steels. In the decade from 1980 to 1990, the GOES industry recorded six down years; in the decade from 1990 to 2000, the industry recorded three down years. From 2000 to 2016, the industry has experienced only one down year and that was in 2009 following the global financial meltdown.
In tandem with this shift to continuous market expansion, and in part driven by increasing transformer efficiency standards in the USA and Europe, there’s been an increase in use of higher performance (HB) electrical steel products, which now account for about 60 percent of the market. From 2010 to 2015, the percentage of HB consumption increased gradually from 41 percent to 48 percent of the total. In 2016, HB consumption surged as the Chinese became more aggressive exporters of the products and the premium between RGO and HB for the 0.23 mm thickness remained at historically low levels. (Note: The HB percentage has dropped slightly in 2017 due to two new RGO entrants to the marketplace.) Supply of HB requires investment in modern equipment supported by dedicated research and development efforts. New market entrants (in China and South Korea) have invested heavily to produce the increasingly demanding HB products that have historically been the domain of product developers in the USA and Japan.
With the evolution in mills’ ability to control the production process, there has also been a shift in demand for product thicknesses. For RGO products, the market in the past few years has shifted from 50 percent 0.27 mm to almost 70 percent, as many producers have consolidated their offerings of 0.30 mm into a single “thicker” category. There has also been an increase in RGO 0.23 mm products to 20 percent of the mix from less than 10 percent and will likely continue to expand to 30 percent. For HB products, the market has historically been 50 to 55 percent 0.23 mm, which has expanded to about 70 to 75 percent, and we believe will continue to expand to 75 to 80 percent.
With the exit of Allegheny Technologies from the electrical steel market in 2016, the only remaining USA producer for these products is AK Steel. Big River Steel, the newest USA EAF steel producer located in Osceola, Ark., designed its mill with a proposed phase II production expansion that would include both non-oriented steel (NOES) and GOES products. While this capital investment has yet to receive board approval, it’s likely to get a green light given the late John Correnti’s vision for the mill, which included electrical steels, and current CEO David Stickler’s commitment to deliver on that vision, in this analyst’s view. We could see electrical steel production from Big River before the end of the decade.
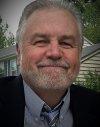
Tim Triplett
Read more from Tim TriplettLatest in Economy
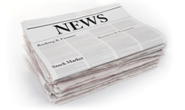
Steel groups welcome passage of budget bill
Steel trade groups praised the passage of the Big Beautiful Bill (BBB) in Congress on Thursday.
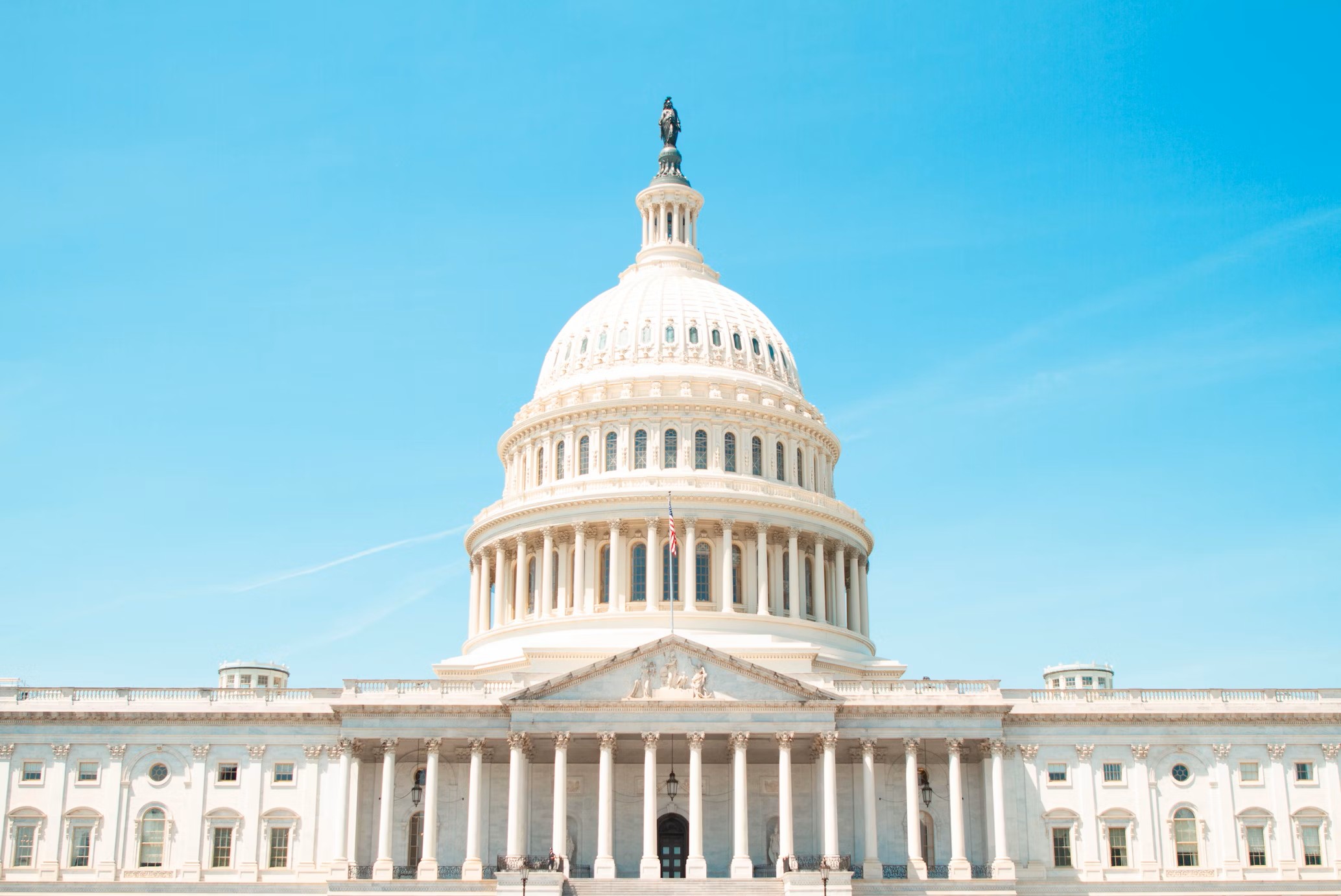
Industry groups praise Senate for passing tax and budget bill
The Steel Manufacturers Association and the American Iron and Steel Institute applauded the tax provisions included in the Senate's tax and budget reconciliation bill.
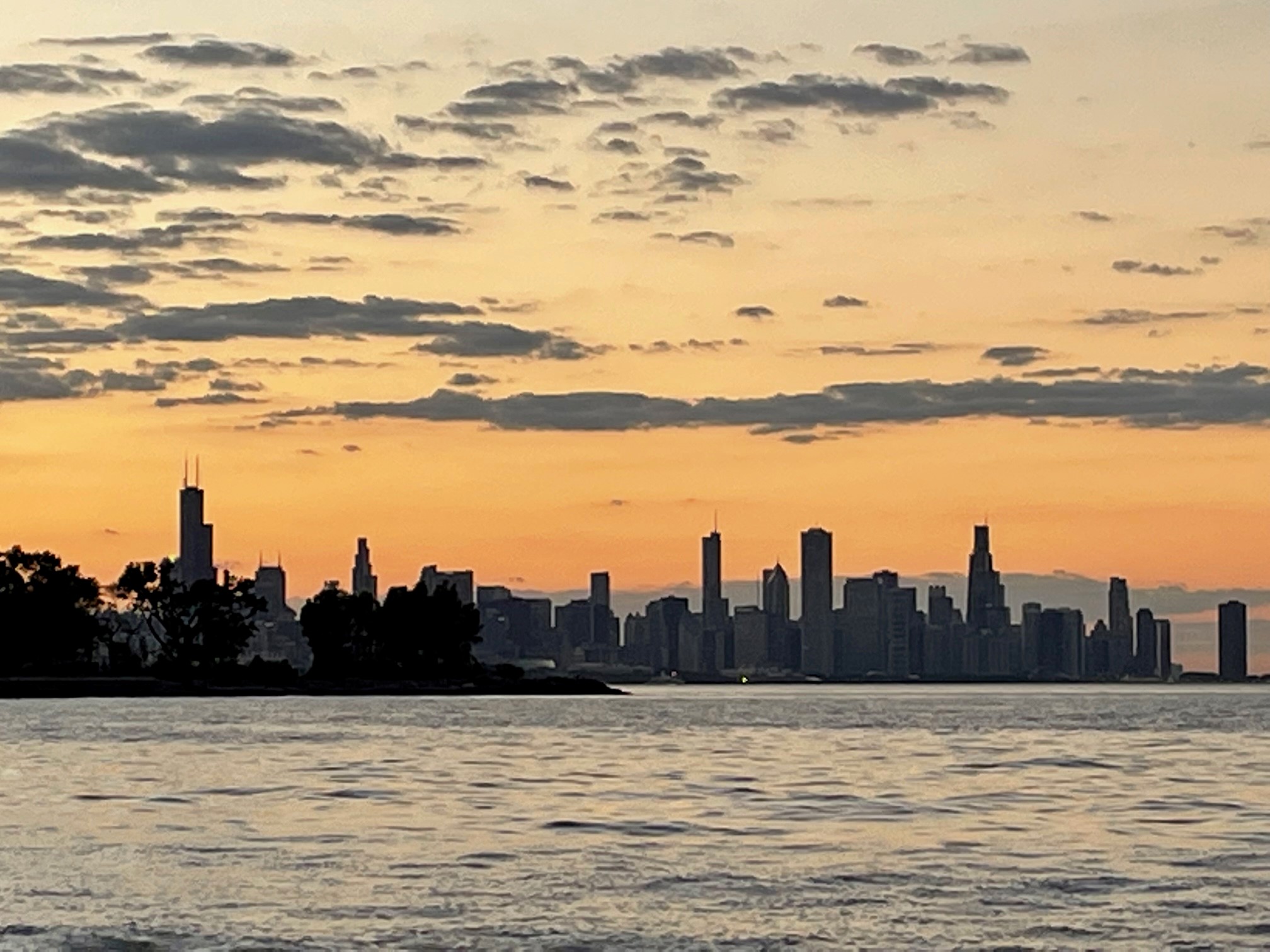
Chicago PMI dips 0.1 points in June
The Chicago Purchasing Managers Index (PMI) slipped 0.1 points to 40.4 points, in June.
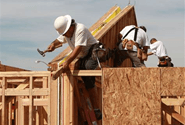
Multi-family pullback drives housing starts to 5-year low in May
US housing starts tumbled in May to a five-year low, according to figures recently released by the US Census Bureau.
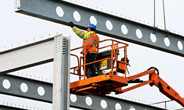
Architecture firms still struggling, ABI data shows
Architecture firms reported a modest improvement in billings through May, yet business conditions remained soft, according to the latest Architecture Billings Index (ABI) release from the American Institute of Architects (AIA) and Deltek.