Toll Processors
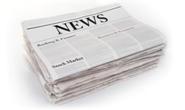
Toll Processor Sees Fabrication in its Future
Written by Tim Triplett
November 26, 2017
It’s not that unusual anymore to find a service center that has taken its value-added offerings as far as first-stage parts manufacturing. Less common is a toll processor that offers fabrication.
Mississippi Steel Processing (MSP) is located on the campus of Steel Dynamics’ mill in Columbus, Miss. For the past two years, it has shared the facility with sister company Layhill Precision Fabrication. “The fabricating operation was really born out of necessity,” explained President Chip Gerber.
Gerber originally relocated to Mississippi for Heidtman Steel, to spearhead construction of a processing center adjacent to the new Severstal mill. When Heidtman opted to pull out of the project, Gerber partnered with Rich Merlo of Chicago-based JDM Steel to build the facility anyway. The 130,000-square-foot processing center began operations in 2011. It was originally designed to process heavy-gauge coils up to 90,000 pounds, housing a 1/4- by 72-inch slitting line and a 5/8- by 84-inch cut-to-length line.
The alliance with Severstal, primarily toll processing steel for makers of oil country tubular goods, proved fruitful, and the mill soon began to pressure MSP to expand. So, the partners added another 120,000 square feet and installed a second 5/8-inch slitter, a 3/8-inch slitter and a 3/16-inch cut-to-length machine, for a total of five lines. “At that time, we were processing 40,000 tons a month, filling 100 trucks and 10 railcars a week. We were a very busy operation, heavily concentrated in the OCTG market,” Gerber recalled.
Then, in the spring of 2014, the price of oil began a slide that took it from over $110 per barrel to under $50 in a matter of six months. By mid-2015, the price had reached as low as $30. The oil boom in the shale fields of the U.S. stalled abruptly. “When the OCTG market collapsed, we lost a substantial portion of our business in heavy-gauge slitting,” Gerber said.
As if that weren’t bad enough, Russia-based Severstal announced its plans to sell the mill and exit the U.S. market. “It was a trying time for us. We had a market that collapsed and a mill that was looking to be sold. We had some challenges in front of us,” Gerber said.
In September 2014, Steel Dynamics bought the fully modern minimill from Severstal for $1.6 billion. MSP found itself allied with a new neighbor, one focused more on light-gauge materials including prepaint and coated steels. “It was clear we were going to have to reinvent ourselves,” Gerber said. “We had a big overcapacity problem. Since we couldn’t make the building any smaller, we needed to find another way to utilize the space. So, we asked ourselves, what else can we do for our customers?”
Their answer was to use some excess capacity for first-stage parts manufacturing and fabrication, a move that has been tried by many forward-thinking service centers, but is unusual for a toll processor. The partners formed Layhill Precision Fabrication as a separate company, which began operations in 2015. “It’s a one-stop shop. An OEM can go to the mill, buy the steel, have it toll processed right next door by MSP, then have parts burned and formed by Layhill, all in one location,” Gerber said.
The fabrication operation is equipped with three plasma tables and two press brakes to cut and bend shapes into finished parts. On its shopping list are new laser cutters. It also offers welding services.
Layhill shares in the logistical advantages MSP derives from being located on the same campus as SDI Columbus. There is no freight cost to move material from the mill to the processing center next door, and certainly not across the bay from MSP to Layhill. The fabrication operation makes parts from prime material, as well as secondary and excess steel that may be left over from toll processing operations. It can often source steel very economically from service centers that are doing business with MSP. And MSP can refer business to Layhill from OEM customers looking to outsource early-stage manufacturing steps, Gerber said.
Layhill Precision Fabrication is still a small part of the partners’ business, but it’s a fast-growing part, Gerber said. Today, Layhill plasma cuts and forms about 6,000 parts per month with 15 employees. MSP levels, slits and blanks about 25,000 tons per month with 60 employees. About 70 percent of MSP’s business comes from service centers, 20 percent from tube makers and 10 percent from OEMs that source steel from SDI. “We are a virtual warehouse for service centers that have customers in our region,” he noted.
Before Layhill was formed, MSP’s OEM customers would often ship their material to another fabricator to be bent and formed into parts. Now, they can have the whole process taken care of in one location, Gerber said. “We are a bit of a hybrid. Layhill is a standalone manufacturing company, but it also toll processes parts for MSP’s toll processing customers. That aspect is unique.”
Even with Layhill’s contribution, MSP’s recovery is still ongoing. In January, MSP plans to begin production on a new light-gauge slitting line designed to handle painted coils and other surface-critical products. “That will help us get more in line with what SDI is producing now and plans to produce in the future,” Gerber said.
But the toll processor stills sees fabrication in his future. “I definitely see the manufacturing side growing. More and more people are outsourcing parts.”
Written by Tim Triplett, Tim@SteelMarketUpdate.com
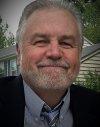
Tim Triplett
Read more from Tim TriplettLatest in Toll Processors
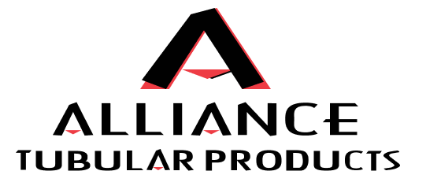
Alliance Steel expands into tubular market
Flat-rolled steel service center Alliance Steel has expanded into the tubular market with the launch of Alliance Tubular Products. The new Alliance division manufactures square and rectangular electric resistance welded (ERW) products and steel HSS tubing. Production has already started and will continue to ramp up next year, the company said in a statement. Alliance […]
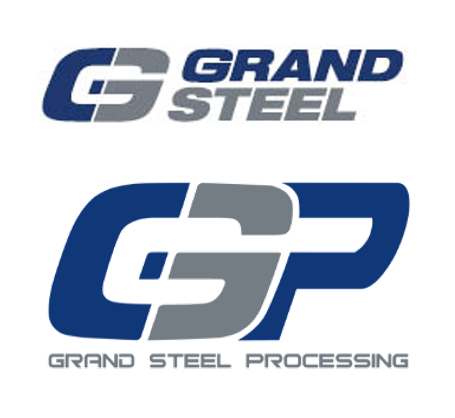
Grand Steel buys Chattanooga toll processing facility
Grand Steel has acquired a new toll processing facility in Chattanooga, Tenn., marking the third location for the flat-rolled steel service center.
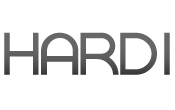
Get your muck boots out: Galv buyers see ‘swampy’ steel market continuing
Swampy. Sticky. Mushy. Murky. These were all words galvanized buyers used this week to describe the current state of the US steel market.
Metalformers expect steady conditions in coming months
Metalformers expect economic activity to stabilize over the next three months, according to the recently released July Business Conditions Report from the Precision Metalforming Association (PMA).
Metalformers’ business outlook worsens
Most metalformers expect economic activity to be level to down over the next three months, according to the May Business Conditions Report from the Precision Metalforming Association (PMA).