Steel Mills
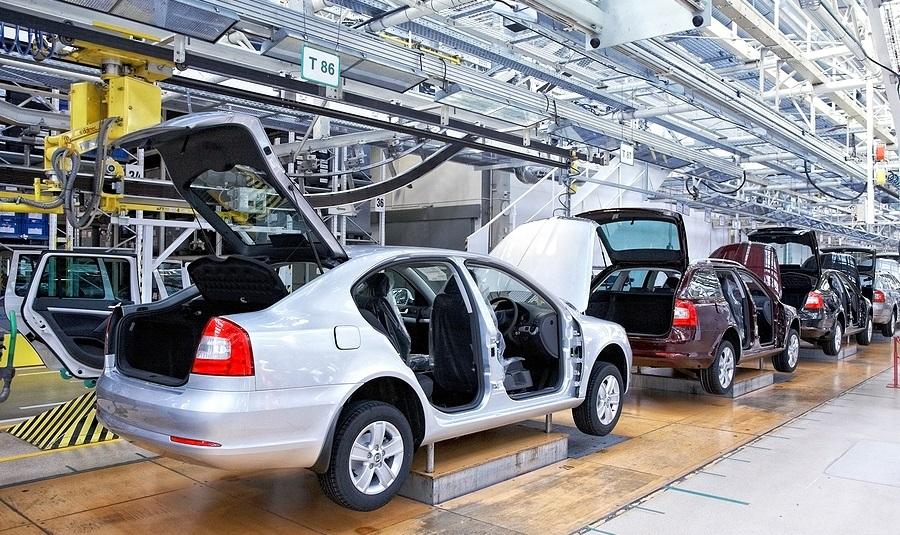
Steel Makes a Comeback in Audi A8
Written by Sandy Williams
May 14, 2017
The following article was provided and first published by ArcelorMittal USA news:
After experimenting with aluminum in its luxury models, Audi’s next A8 will switch back to steel. Scheduled for release in 2018, the body structure of the new A8 will be made up of more than 40 percent steel, following the trend of automakers opting to use advanced high-strength steels in new vehicles. That’s a marked turnaround from the all-aluminum body-in-white which Audi developed for the A8 in 1994.
Since, steel has evolved dramatically. In fact, steel’s strength has multiplied by almost 10 times over the past 20 years, from 270 to 2000MPa tensile strength. More than 80 new steel products are under development at ArcelorMittal, with an automotive steel grade portfolio of almost 200 unique steel grades, half of which were introduced in just the past decade.
Around 17 percent of the new A8 body structure will be comprised of press hardenable steel (PHS), some of which will be supplied by ArcelorMittal. These steels have yield strengths up to 1500 MPa after press hardening. The strength-to-weight ratio of these grades outperforms even the most advanced – and costlier – aluminum grades. With the advent of new joining technologies, it has never been easier for automakers to incorporate advanced high-strength steels into their vehicles. As these technologies mature and are adopted by carmakers, the use of PHS in the multi-material vehicles of the future is set to grow rapidly.
“Usibor® is our key product in hot stamping and has been a major commercial and technical success in the global automotive industry,” said Brian Aranha, executive vice president, global automotive, ArcelorMittal. “Looking ahead, the scope of hot stamping products in vehicles will continue to increase with the release of more advanced products like Usibor® 2000, which offers 10 to 15 percent weight savings when compared to existing hot stamping solutions.”
Usibor® is compatible with standard press hardening technologies and processes. Combining Usibor® with Ductibor® into laser welded blanks offers several significant advantages including weight savings, improved crash behavior and cost savings through material and manufacturing optimization.
Dr. Bernd Mlekusch, head of the Audi’s Leichtbauzentrum, or Lightweight Construction Center, said: “There will be no cars made of aluminum alone in the future. Press hardened steels (PHS) will play a special role in this development. PHS grades are at the core of a car’s occupant cell, which protects the driver and passengers in case of a collision. If you compare the stiffness-weight ratio, PHS is currently ahead of aluminum.”
Audi’s switch back to steel is part of a growing trend which is even surpassing the expectations of steelmakers, according to data released by the Steel Market Development Institute (SMDI).
Between 2006 and 2015, the use of advanced high-strength steels in vehicles has grown from an average of 81 pounds per vehicle (36.7 kg) to 275 pounds (124 kg). That’s a threefold increase in just 10 years. What’s more surprising is that over the period 2012 to 2015, the use of AHSS has increased by around 10 percent each year, well above steel industry forecasts.
ArcelorMittal and the steel industry as a whole have been working collaboratively to educate automakers and stakeholders on the importance of life cycle analysis, or LCA. LCA looks at total emissions generated during the three stages of a vehicle’s life – production, drive phase and disposal.
“Right now, regulations only consider tailpipe emissions generated during the drive phase,” said Brad Davey, chief marketing officer, NAFTA and global automotive for ArcelorMittal. “However, each material used in vehicle production contributes to lightweighting and improves fuel economy, but each does so at a different cost to the manufacturer – and to the environment.”
Studies show that aluminum produced in North America emits four to five times more GHGs than steel. Additionally, aluminum requires seven times more energy to produce than steel.
“If we want to know how “green” a vehicle really is, we have to measure emissions over its entire life cycle. Otherwise, choosing an alternative material over advanced steel will result in a huge and irreversible environmental mistake,” said Davey.
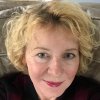
Sandy Williams
Read more from Sandy WilliamsLatest in Steel Mills

Nippon plans to double steel output at USS operations: Report
Now that it has acquired U.S. Steel, Nippon Steel is planning a significant expansion of its US operations, including the construction of a new mill and more than doubling its steel output.
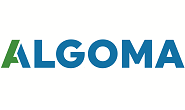
Algoma fires up EAF steelmaking with first arc
Algoma Steel reached a milestone in its transformation from blast furnace to electric arc furnace (EAF) steelmaking, with its Unit One EAF achieving its first steel production this week.
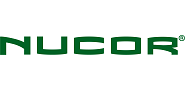
Nucor holds HR list price at $910/ton
Nucor is keeping its list price for spot hot-rolled coil unchanged after last week’s shortened holiday week.
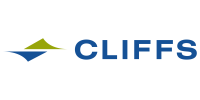
Cliffs unveils new hydrogen-powered stainless line in Ohio
CEO Lourenco Goncalves, flanked by state leaders and union reps, touted the project as proof that US manufacturing is not only alive, but also advancing.
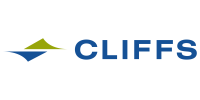
Cliffs idles Steelton, Riverdale, and Conshohocken operations
Cliffs has idled facilities in Riverdale, Ill., and Conshohocken and Steelton, Pa.