Steel Mills
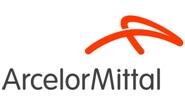
ArcelorMittal Unveils New AHSS
Written by Sandy Williams
September 6, 2014
Developed by research and development teams in France and the USA, the Fortiform™ range will initially be produced and developed at two ArcelorMittal sites in Belgium: Gent and Kessales (Liège).
The new Fortiform™ range of advanced high strength steels (AHSS) for cold stamping could lead to further weight savings of up to 20% in vehicle parts, compared with the weight savings already offered by ArcelorMittal’s current AHSS. This is a crucial advantage as car makers come under pressure to further lighten vehicles and thereby reduce their emissions. Because of its superior properties, the Fortiform™ range is able to absorb more energy in a crash, with less steel. This makes it suitable for use in many structural parts of the vehicle that may be affected during impact, including front and rear chassis members and windscreen A- and B-pillars.
The Fortiform™ range currently consists of three steel grades. Fortiform™ 1050 is the first product of this new range to be available on the market and has already undergone formability and weldability tests with global carmakers who have all approved its use. The first serially produced vehicles to use the new steel will roll off production lines in 2017.
Two other grades, Fortiform™ 980 and Fortiform™ 1180, will be released between 2014 and 2017. Samples will be available to manufacturers for testing later this year, with industrial production set to start in 2015. Other products will follow in various regions, in line with available technology and demand.
The successful launch of the Fortiform™ range of steels is further proof that steel is by far the most sustainable, the most adaptable and the most affordable material to help carmakers produce lighter vehicles – and achieve their weight reduction targets on time without compromising strength and safety. Fortiform™ was developed to complement ArcelorMittal’s existing AHSS offer, which features hot stamping grades such as Usibor® and Ductibor®.
In 2013, ArcelorMittal spent $270m on R&D activities, of which more than 30% was devoted to the automotive market. (Source: ArcelorMittal)
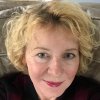
Sandy Williams
Read more from Sandy WilliamsLatest in Steel Mills
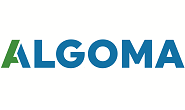
Algoma fires up EAF steelmaking with first arc
Algoma Steel reached a milestone in its transformation from blast furnace to electric arc furnace (EAF) steelmaking, with its Unit One EAF achieving its first steel production this week.
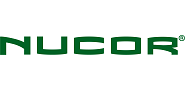
Nucor holds HR list price at $910/ton
Nucor is keeping its list price for spot hot-rolled coil unchanged after last week’s shortened holiday week.
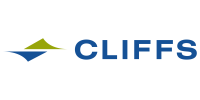
Cliffs unveils new hydrogen-powered stainless line in Ohio
CEO Lourenco Goncalves, flanked by state leaders and union reps, touted the project as proof that US manufacturing is not only alive, but also advancing.
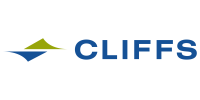
Cliffs idles Steelton, Riverdale, and Conshohocken operations
Cliffs has idled facilities in Riverdale, Ill., and Conshohocken and Steelton, Pa.
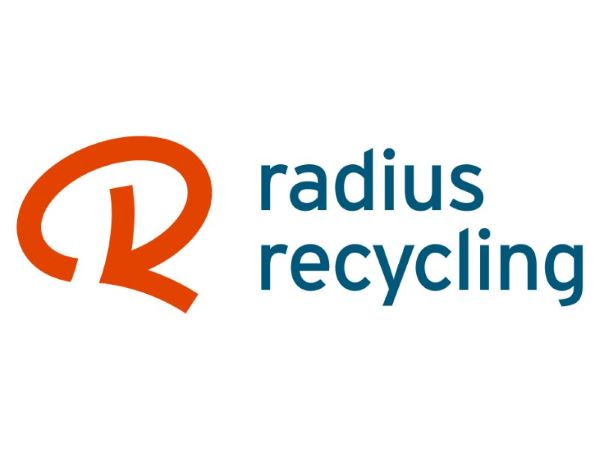
Radius loss narrows, volumes climb in ‘healthy’ West Coast market
Stronger steel demand in the Western US, rising scrap flows, and improved rolling mill utilization drove sequential gains for Portland, Ore.-based Radius Recycling.