Steel Markets
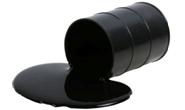
Tank Car Replacements Will Use More Steel
Written by Sandy Williams
April 6, 2014
Steel producers and distributors can expect an influx of orders for steel plate for rail tank cars in the next several years. After several serious tanker accidents involving crude oil transport, the Association of American Railroads Tank Car Committee (AARTCC) and Railway Supply Institute Committee on Tank Cars (RSICTC) have each submitted higher safety standard proposals to the Pipeline and Hazardous Materials Safety Administration (PHMSA).
The proposals outline tougher standards for the replacement of 228,000 DOT-111 tankers during the next ten years. Retrofits are also proposed to improve the safety of those currently in service.
Rail tank cars are huge consumers of steel plate using approximately 32 tons of steel per unpressurized car and 41 tons of steel for pressurized tanks, according to data by the American Iron and Steel Institute (AISI). Volatile chemicals in crude oil, particularly from the Bakken shale deposits, can cause steel corrosion resulting in tank failure during accidents.The RSITC proposal suggests new DOT-111s have the following enhancements:
– PG I and II flammable liquids tank cars to be constructed to 286,000-pound Gross Rail Load standards;
– Heads and shells must be constructed of normalized steel;
– New cars must at a minimum be equipped with one-half inch thick half-height protective head shields;
– For tank cars constructed of normalized TC128 Grade B steel, head and shell thickness must be one-half inch for non-jacketed cars and seven-sixteenths of an inch for jacketed cars;
– For tank cars constructed of normalized A516-70 steel, shells of non-jacketed tank cars must be nine-sixteenths of an inch thick while shells of jacketed tank cars must be one-half inch thick;
– Top fittings must be protected by a protective structure as tall as the tallest fitting;
– Installation of a reclosing pressure relief valve;
The AARTCC proposes similar standards for new non-pressurized tank cars, plus retrofitting of P-1577 cars including:
– an outer steel jacket around the tank car and thermal protection,
– full-height head shields,
– and high-flow capacity pressure relief valves;
– Require additional safety upgrades to those tank cars built since 2011, including:
– installation of high-flow-capacity relief valves, and
– design modifications to prevent bottom outlets from opening in the case of an accident;
– aggressively phase out older-model tank cars used to move flammable liquids that cannot be retrofitted to meet new federal requirements, and
– eliminate the option for rail shippers to classify a flammable liquid with a flash point between 100 and 140 degrees Fahrenheit as a combustible liquid.
There are currently 335,000 tank cars in service (pressure and non-pressure), 228,000 of which are Dot-111 non-pressurized tank cars carrying hazardous and non-hazardous material. AAR says approximately 14,000 of tank cars produced since 2011 were made with improved AAR Tank Car Committee standards that include thicker shells, extra protective head shields at both sides of the car, and enhanced top fittings protection. AAR says approximately 78,000 of 92,000 tank cars moving flammable liquids will require retrofitting or phase out. The 14,000 produced since 2011 will also require some upgrades.
Three of the largest manufacturers of tank cars are American Rail Car, located in St. Charles, Missouri; Trinity Rail, a division of Trinity Industries located in Dallas, Texas; and Greenbrier Companies, headquartered in Lake Oswego, Oregon.
In February of this year, Greenbrier, Co. announced it will design a new generation “Tank Car of the Future” for rail transport of hazardous freight, including crude oil. It will also retrofit the legacy DOT-111 tank cars. Greenbrier can produce 4000 tank cars per year and no longer produces the DOT-111 for use with flammable liquids.
William A. Furman, chairman and chief executive officer of Greenbrier recently commented on the proposed new standards, “As a result of the energy renaissance in the U.S., crude by rail shipments have climbed from 9,500 carloads in 2008 to more than 400,000 carloads in 2013. While 99.97% of these shipments arrive without incident, our common goal should be zero rail incidents. We are pleased that the AAR and DOT have taken steps to make rail transport safer for both our communities and environment with new operating standards.”
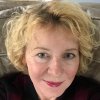
Sandy Williams
Read more from Sandy WilliamsLatest in Steel Markets
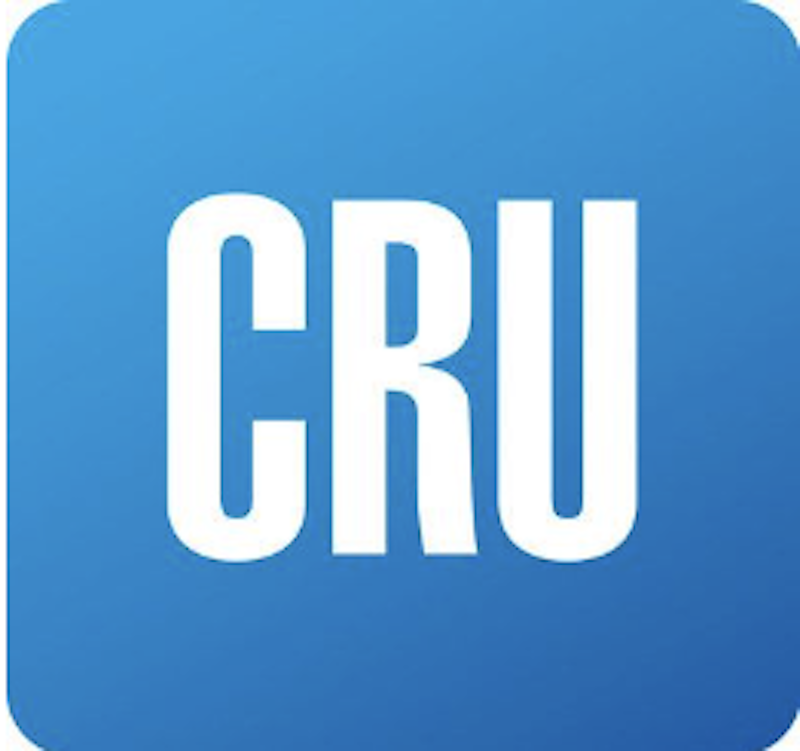
CRU: Sheet import demand softens as domestic price gains have slowed
US domestic sheet price gains have begun to slow as previously pulled-forward demand has led to a decline in orders.
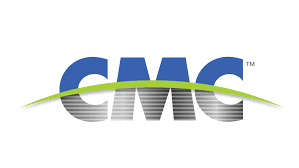
CMC looks beyond Arizona micro-mill woes to long-term viability of construction mart
Despite the economic and geopolitical upheaval of the last five years, CMC President and CEO Peter Matt points out that the construction market has been an essential element of the way forward.
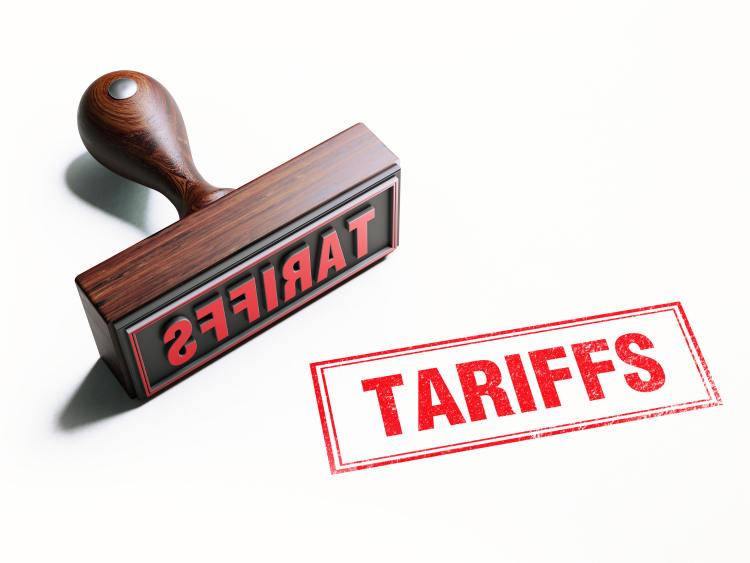
US importers face stricter rules under revamped S232 tariffs
“CBP expects full compliance from the trade community for accurate reporting and payment of the additional duties. CBP will take enforcement action on non-compliance," the agency said in a March 7 bulletin.
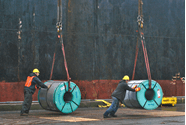
Steel exports rebound in January
US steel exports recovered to a five-month high in January after having fallen to a two-year low in December. This growth follows four consecutive months of declining exports.
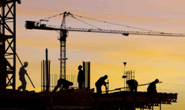
Construction spending drops marginally in January
Construction spending edged down slightly in January, slipping for the first time in four months. The US Census Bureau estimated spending at a seasonally adjusted annual rate of $2,196 billion in January, down 0.2% from December’s downward revised rate. The January figure is 3.3% higher than a year ago. January’s result, despite the slight erosion, […]