Steel Products Prices North America
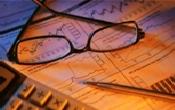
April Industrial Production and Manufacturing Capacity Utilization
Written by Peter Wright
May 15, 2014
Both Industrial Production (IP) and Manufacturing Capacity Utilization are reported in the Federal Reserve G17 data base. The IP index was reported as 102.744 for April, with a three month moving average (3MMA) of 102.83. This was the fifth consecutive month for the index to exceed the pre-recession peak of September 2007. The 3MMA has expanded for 12 straight months and is up by 3.55 y/y. Data is seasonally adjusted. This index is based on the July 2007 level being defined as 100, (Figure 1).
Manufacturing capacity utilization was 76.43 percent in April, down from 76.88 in March but the 3MMA continued to increase and now has a string of three months of improvement, (Figure 2). The 3MMA is now the highest since May 2008.
The Federal Reserve Beige Book released on April 16th reported as follows: Conditions in the manufacturing sector improved since the previous Beige Book. The Chicago and Minneapolis Districts reported moderate growth, with a pickup in new orders and production. The San Francisco District stated that manufacturing activity appeared to gain some momentum. Manufacturing in the Boston, New York, Atlanta, St. Louis, and Dallas Districts grew at a steady pace, while Philadelphia, Cleveland, and Kansas City reported mild growth. Richmond reported mixed conditions in manufacturing. The Boston, New York, Philadelphia, Cleveland, Richmond, Atlanta, Chicago, Kansas City, and Dallas Districts noted that lingering winter weather hampered business activity, but the impact was less severe than earlier this year. The auto, aerospace, and energy-related industries remained a source of strength for the Chicago District. Energy-related manufacturing was also particularly strong in Dallas. The sustained backlog of orders for commercial aircraft supported growth in the commercial aerospace industry in the San Francisco District. The Chicago District indicated that steel production recovered from a weather-related slowdown and capacity utilization returned to its expected levels. Additionally, specialty metals manufacturers reported an increase in new orders and order backlogs. In contrast, food manufacturers in Boston, Richmond, and Dallas reported a decline in demand that was largely weather related, but indicated that production was unchanged overall. Steel shipments grew slightly in Cleveland, with contacts anticipating slow growth in the months ahead. The demand for steel production inputs improved from both domestic and foreign sources in the San Francisco District. Firms expected continued moderate growth in manufacturing, with some increased optimism.
CNBC reported on Monday: more businesses exporting ‘Made in USA’ again.
One bet on the economy is that American manufacturing is staging a comeback. With labor costs rising in China, U.S. companies are taking a second look at operations and incorporating more domestic production. Now in a twist on “Made in USA” and the larger reshoring movement, more small to mid-sized U.S. businesses are making and exporting goods as part of their growth strategy. Six years after the recession began, the U.S. recovery is patchy. A measure of Americans working, and those seeking jobs—the labor force participation rate—has tumbled to near 35-year lows. More business owners are canvassing this new normal and thinking: We need to export. Large multinationals have been exporting for decades. Now, even smaller companies based in smaller cities—thanks to e-commerce and access to ports—are courting international markets. Inside regional U.S. airports, entrepreneurs are boarding international flights to pitch products. Workers at U.S. ports are loading more containers, packed with everything from U.S.-origin lumber to glass. A Pennsylvania company is shipping building materials to Mongolia. It’s one of the coldest countries, where effective home insulation is a big challenge. A Tennessee business is ramping up patterned glass production, destined for churches and homes in South America and Europe. A Florida maker of porcelain lighting is not only exporting but has opened an Australian outpost after orders climbed. Only a handful of U.S. companies make porcelain lighting and opaque patterned glass, with the bulk of such production is in China. More businesses are making bigger bets on exports, as many American consumers spend cautiously. “Every company needs a fallback contingency plan,” said Eric Kerney, president of Heritage Glass in Kingsport, Tennessee. “Our contingency plan is we can diversify.” And this direction of “Made in USA” goods overseas is contributing to the post-recession recovery. “Manufacturing is key to providing jobs and driving the economy,” said Bryan Scott, co-owner of Barn Light Electric based in Titusville, Florida. “Even small companies are participating and exporting their products to China,” said Hal Sirkin, senior partner at The Boston Consulting Group in Chicago.
SMU Comment: prior to the recession there was a reasonable correlation between industrial production and steel supply although steel was very much more volatile in this comparison, just as it is against GDP, (Figure 3). We have many indicators that suggest that steel supply is much lower than it should be at this stage of a recovery and IP is one of them. We believe the main reason for the discrepancy is the continued low activity by historical standards of the major sectors of construction. This includes, housing, non-residential buildings and infrastructure.
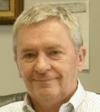
Peter Wright
Read more from Peter WrightLatest in Steel Products Prices North America
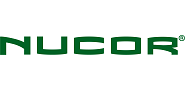
Nucor slows HRC price climb with $5/ton increase
After eight weeks of double-digit price increases on hot-rolled (HR) coil, Nucor slowed the price rise this week with an increase of $5 per short ton.
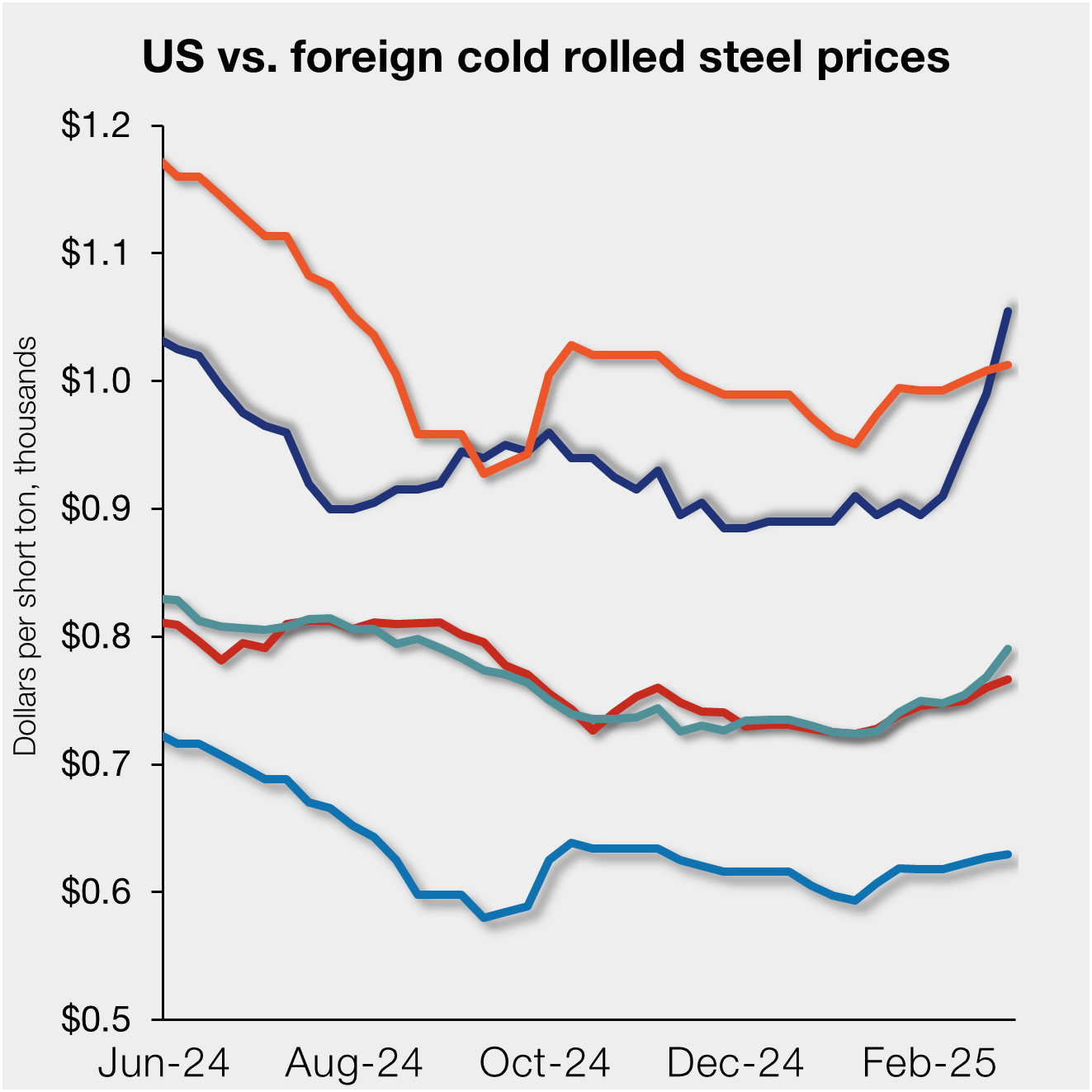
Domestic CRC prices surge ahead of imports
The price spread between stateside-produced CR and imports reached its widest margin in over a year.
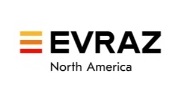
Evraz raises plate prices $160/ton
Evraz North America (NA) has followed Nucor and SSAB with a plate price increase of its own: up $160 per short ton (st). The increase was effective immediately for all new orders of carbon, high-strength low-alloy, and normalized and quenched-and-tempered plate products, as well as for hot-rolled coil, the steelmaker said in a letter to […]
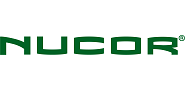
Nucor lifts HR coil to $820/ton
Nucor has increased its consumer spot price (CSP) for hot-rolled (HR) coil for a fourth consecutive week.
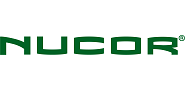
Nucor pushes HR spot price to $790/ton
Nucor increased its consumer spot price (CSP) for hot-rolled (HR) coil to $790 per short ton (st) on Monday, Feb. 10 – a $15/st bump vs. last week. The Charlotte, N.C.-based company has raised its weekly CSP by $40/st over the past three weeks after maintaining tags at $750/st since Nov. 12, according to SMU’s […]