Steel Markets
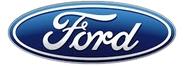
Ford Throws Down Gauntlet Challenging Steel Industry With Aluminum F-150
Written by Sandy Williams
January 14, 2014
The introduction of an aluminum F-150 pickup at the Detroit auto show has the steel industry looking hard at its advanced high strength steels (AHSS) and figuring out how to insure that AHSS is the preferred material of choice for the auto industry.
SMU spoke with Ronald P. Krupitzer, vice president of automotive applications for the Steel Market Development Institute (SMDI) about the recent Ford announcement.
“I’ve never heard anyone at Ford say that aluminum is the material of choice,” said Krupitzer. “What we have seen, and what Ford has said specifically this week, is that Ford engineers are very interested in steel light weighting also.”
Krupitzer cited the F-150 frame which used high strength steel in a redesigned fully-boxed configuration that saved 80 pounds of weight.
SMDI has been involved in research that compares high strength steels with aluminum on a part to part basis that has resulted in car companies choosing steel over aluminum. For example, last year SMDI compared a design for a front motor controller, one forged in aluminum at the lowest weight in the industry at that time, and one a clam shell design made of advanced high strength steel. The steel part weighed exactly the same and saved 30 percent on construction costs. It so impressed General Motors, that the company switched from aluminum to steel for the Malibu, LaCrosse and other vehicles using the same platform and avoided paying the higher cost of aluminum construction.
“We think this kind of experience will repeat itself,” said Krupitzer. It may take a long time for us to replace the aluminum in the F-150. But that would certainly be one of our goals, to put forth better solutions in steel for the next edition F-150 that they can see what would be a lower cost F-150 with all the same attributes but done in steel.”
When asked if other companies are likely to follow Ford in its aluminum design, Krupitzer said the high cost, huge commitment and manufacturing risks would likely make companies hesitant. He said companies will instead study Ford to see if there is a market advantage, whether Ford will be able to handle the manufacturing requirements and if the vehicle will be too expensive to make.
Ford says the aluminum bodied Ford F-150 saves 700 lbs in weight. That results in a reduction of approximately 1000 pounds of steel–a figure that concerns steelmakers when extrapolated over the 763,000 F-series vehicles sold in 2013 for a potential demand loss of around 380,000 tons of steel annually.
“What I really believe is that car companies internally would love to stay with steel,” said Krupitzer. “They just need to be convinced with real data that steel will satisfy their weight requirements.”
Aluminum may be light weight but it comes with a set of problems. Stamping aluminum is more difficult than steel. The spring back in the dies is more severe said Krupitzer, often requiring that dies be designed specifically for the material. Aluminum is difficult to spot weld and manufacturers use a ribbon bonding method that basically glues the vehicle together. It is a slower and more demanding manufacturing process that may reduce the number of trucks that can be made on the same assembly line, thus incurring extra costs.
Aluminum itself is a more expensive material than steel. Saving 20 pounds on construction of a door panel out of aluminum will cost significantly more than saving 15 pounds on door constructed with steel that requires no production changes. Government and industry studies have shown that most effective method of cutting up to 20 percent of weight is with advanced high strength steel. Adding aluminum for weight savings beyond that will drastically increase costs.
Another problem with aluminum is fatigue. Aluminum does not have the same fatigue life as steel and continues to weaken through cyclic loading, something that occurs every time a truck or car is in service. Steel, however, resists fatigue and will not crack.
“In general steel is the better product,” said Krupitzer. “It is the most economic one for mass production of automobiles.
“We have never been challenged quite like this. Ford is definitely throwing down the gauntlet. But I think the steel industry is as ready now as it has ever been. And the beneficiaries will be the car companies and the customers. We are pushing even faster now for continued improvement of steel grade, strength and manufacturing methods. Steel solutions will be improving for years to come.”
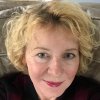
Sandy Williams
Read more from Sandy WilliamsLatest in Steel Markets
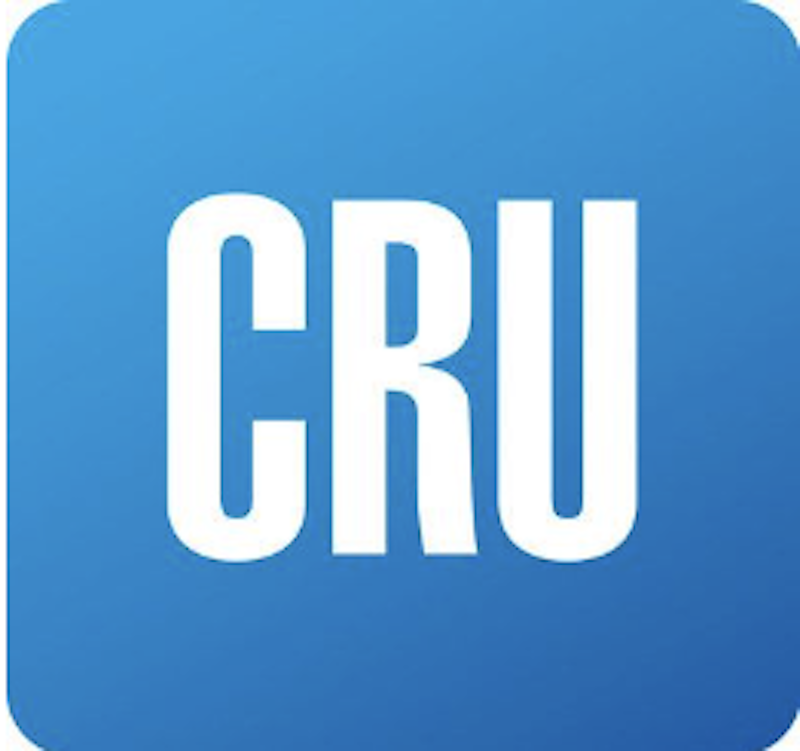
CRU: Sheet import demand softens as domestic price gains have slowed
US domestic sheet price gains have begun to slow as previously pulled-forward demand has led to a decline in orders.
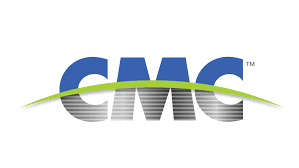
CMC looks beyond Arizona micro-mill woes to long-term viability of construction mart
Despite the economic and geopolitical upheaval of the last five years, CMC President and CEO Peter Matt points out that the construction market has been an essential element of the way forward.
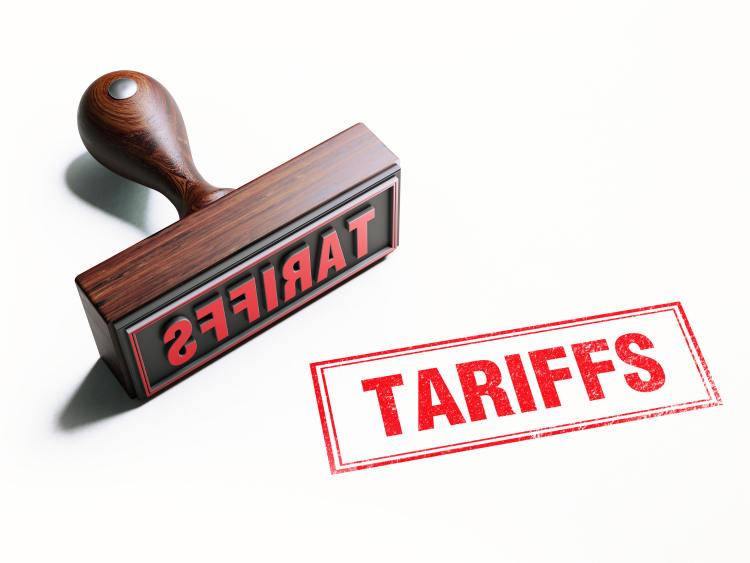
US importers face stricter rules under revamped S232 tariffs
“CBP expects full compliance from the trade community for accurate reporting and payment of the additional duties. CBP will take enforcement action on non-compliance," the agency said in a March 7 bulletin.
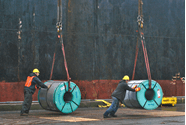
Steel exports rebound in January
US steel exports recovered to a five-month high in January after having fallen to a two-year low in December. This growth follows four consecutive months of declining exports.
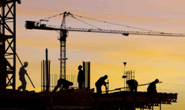
Construction spending drops marginally in January
Construction spending edged down slightly in January, slipping for the first time in four months. The US Census Bureau estimated spending at a seasonally adjusted annual rate of $2,196 billion in January, down 0.2% from December’s downward revised rate. The January figure is 3.3% higher than a year ago. January’s result, despite the slight erosion, […]