Steel Products
Pricing is Hard Work and it Should Be Hard Work
Written by John Packard
February 18, 2013
Written by: John Packard
Steel Market Update (SMU) ran a number of articles concerning the tepid support service centers were giving spot price increases into the manufacturing segment of the industry. SMU surveys the industry twice per month and our most recent steel survey was capturing a very modest push by service centers to take their spot prices up – which is not normal after the domestic mills announce a price increase (usually service center will move their spot prices in strong support of the mill price increases if they believe they will “stick”).
As we looked back at the historical data we had gathered, we found a pattern which shows service centers will either support or not support mill price increases and that support is translated through their efforts to raise prices to their own customers.
We heard from various service centers during the course of the week that the issues could be related to index-based purchasing and better information flow which provides service centers more data and, in turn, allow them to make pricing decisions not to disrupt their customer base. The theory being the peaks and valleys are smoothed out by the indexes. (SMU 2/13)
SMU heard from another service center who basically said their business was not strong enough to allow for the loss of any orders. “…While we’ve all more or less adjusted to our circumstances we don’t get a sufficient number of sales opportunities to knowingly pass on too many of them because we think the price is too low.” (SMU 2/15)
We spoke to a distributor who looked at the market differently. In his opinion the duty of every organization is to understand the values the organization brings to their customers and to make money for their company. He quoted another steel executive when he told us, “You’ve got to put steel in the hands of people who want to make money with it.”
In the case of their organization, they had made a decision to centralize both the purchasing and pricing functions under his direction in order to focus on keeping the company profitable and making sure they understood who they were competing against, and, strategically pricing product as opposed to throwing numbers against a wall to see what sticks.
“Pricing is hard work and it should be hard work,” is what he told me. “The problem is not on the buy side, the problem is on the sell side of the business.” He went on to explain too many companies were not spending the time necessary to do the research on their customers, the competition, the potential for growth in that industry, the cost of doing business – such as the impact on your other customers.
This particular distributor lamented over steel mills when they front load their order books with service centers he deemed “irresponsible.” By irresponsible this distributor was referring to those service centers who use the low pricing they have and not put that advantage in their pocket in a potentially rising market.
He told me, “Understanding your customers, their value drivers, what keeps their executives and purchasing team up at night, the cost to service their business – is hard work. Pricing your customers based on the cumulative value your organization brings to theirs is even harder work. Steel distributors who take a cost plus approach – and by this I mean cost plus some minimum return – take the easy way out, ignoring the market, ignoring the customer’s value needs or even discounting your own company’s value because your sales professional can only communicate a low price. A wise man once told me, ‘business won on price will likely need to be maintained on price.’ Conversely, business won on value will be maintained on that value. Steel mills who sell steel distributors with a cost plus approach simply limit their ability to raise prices – to recover rising costs or otherwise….”
To comment on this article: John@SteelMarketUpdate.com.

John Packard
Read more from John PackardLatest in Steel Products
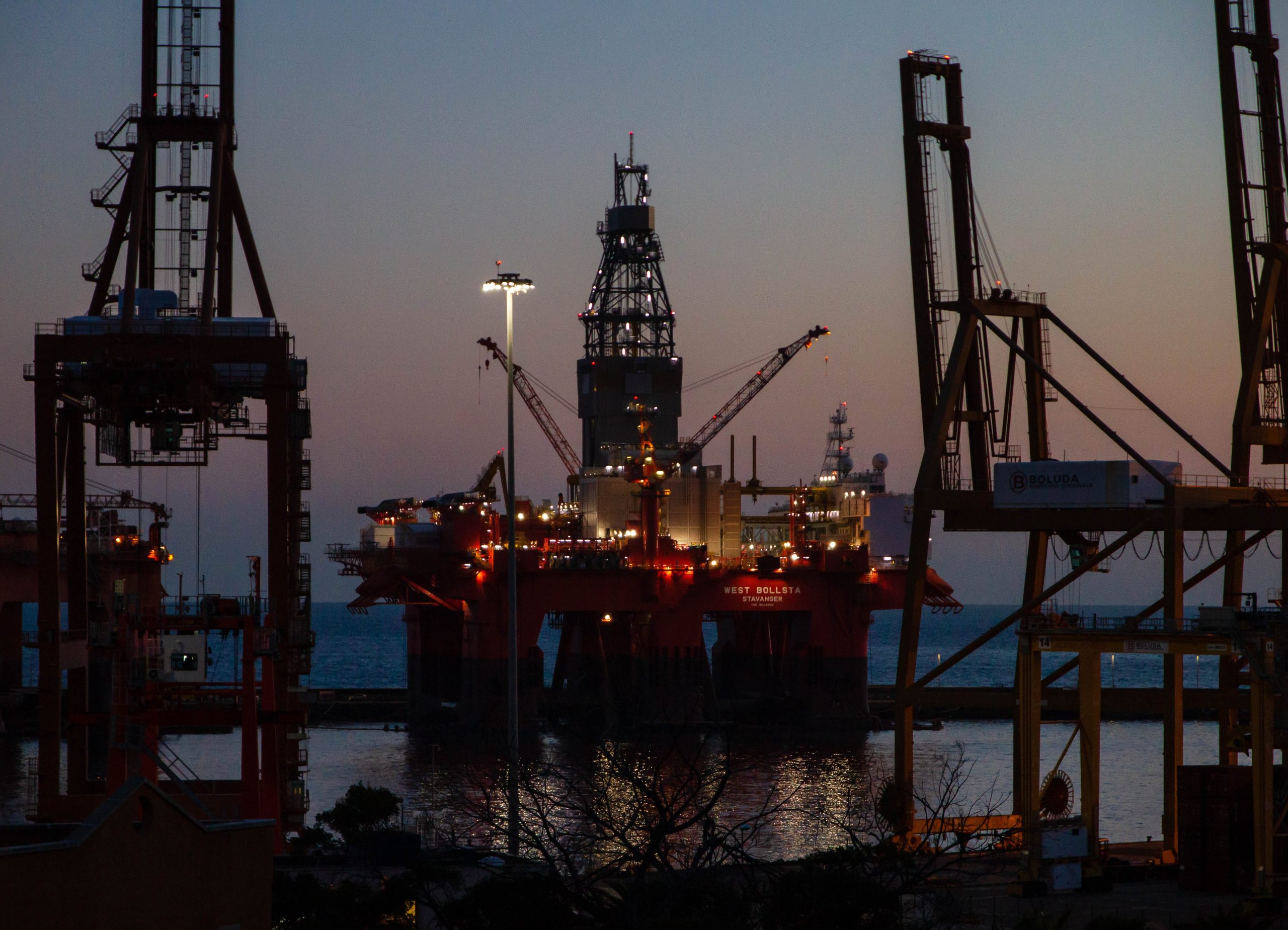
US rig count up, Canada declines
Oil and gas drilling activity was mixed this week, according to Baker Hughes. US rig counts expanded for a second straight week, while Canadian activity continued its seasonal slowdown of eight consecutive weeks.
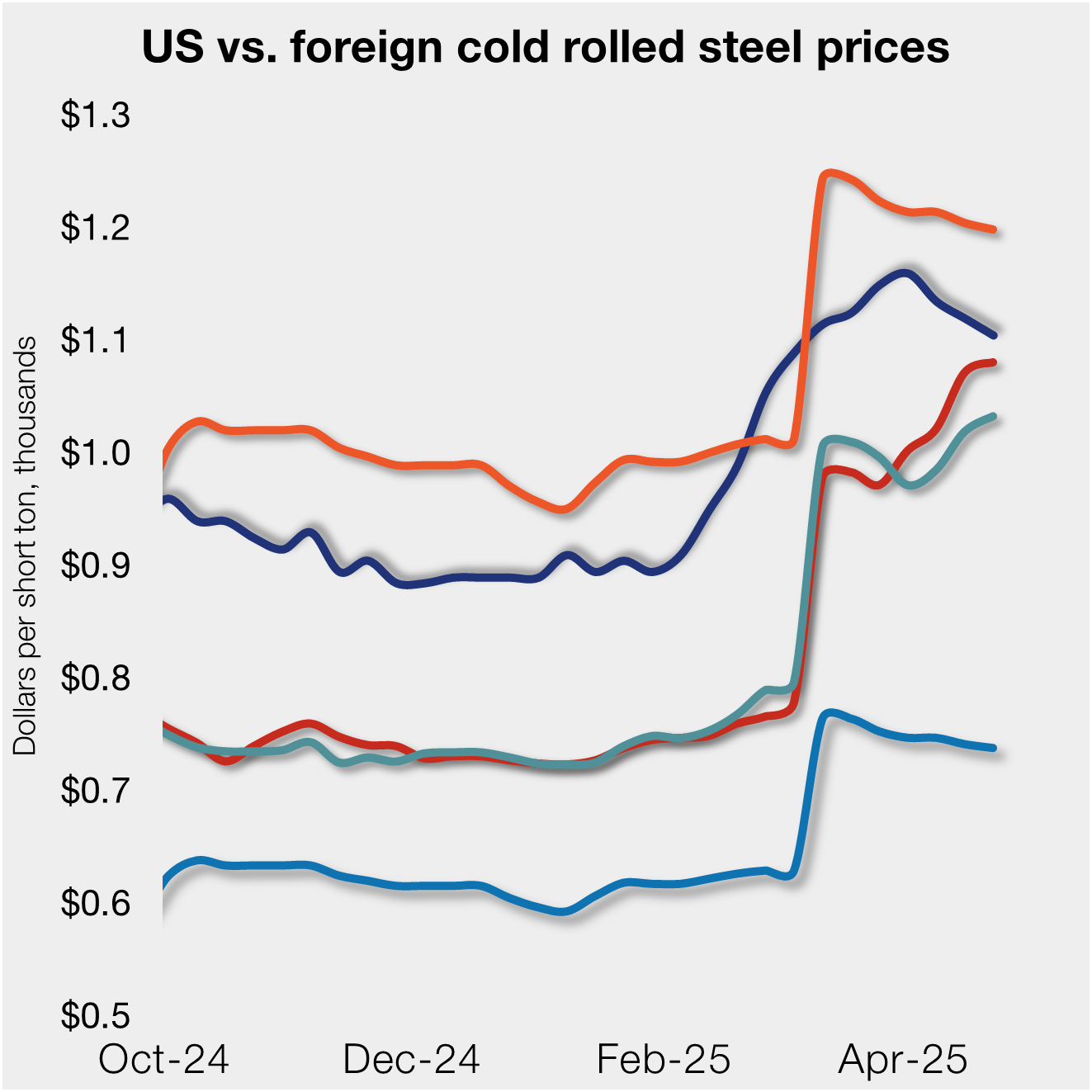
US, offshore CRC prices continue to diverge
US cold-rolled (CR) coil prices declined again this week, slipping for a third straight week. Most offshore markets did the opposite, moving higher this week.
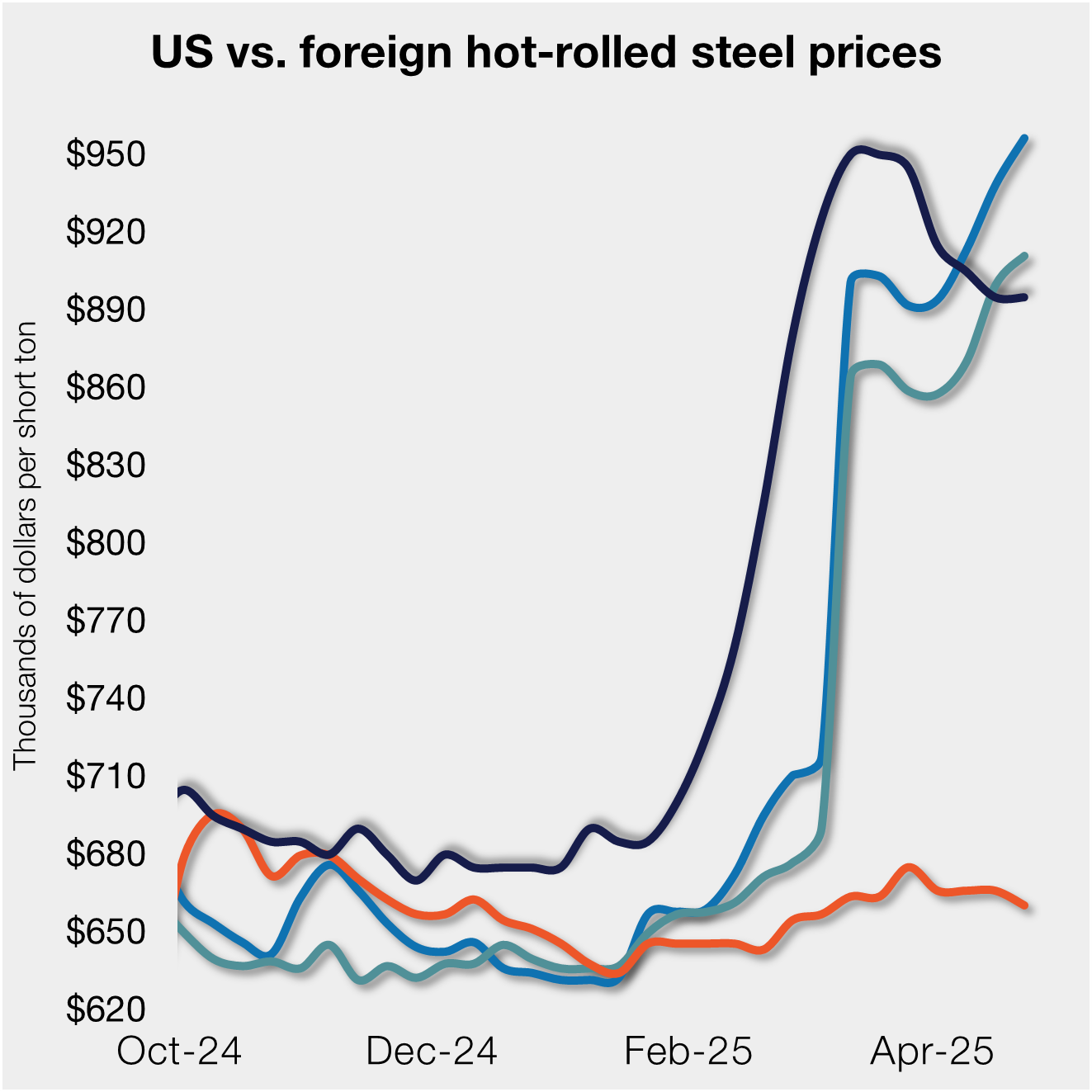
S232 lifts EU HR price over US, Asian HR still well behind
Domestic hot-rolled coil prices were flat this week after dropping for four straight weeks. Most offshore markets bucked the trend and gained ground.
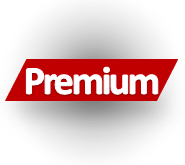
SMU Steel Demand Index dips into contraction
SMU’s Steel Demand Index has moved into contraction, according to late April indicators. The slowdown comes in response to growing tariff uncertainty after the index reached a four-year high in late February.
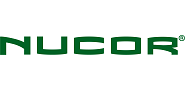
Nucor selects Fives Group for new galv line at CSI
Nucor Corp. has tapped Fives Group as its partner in designing and manufacturing the new continuous galvanizing line being added at its California Steel Industries (CSI) joint venture in Fontana, Calif.